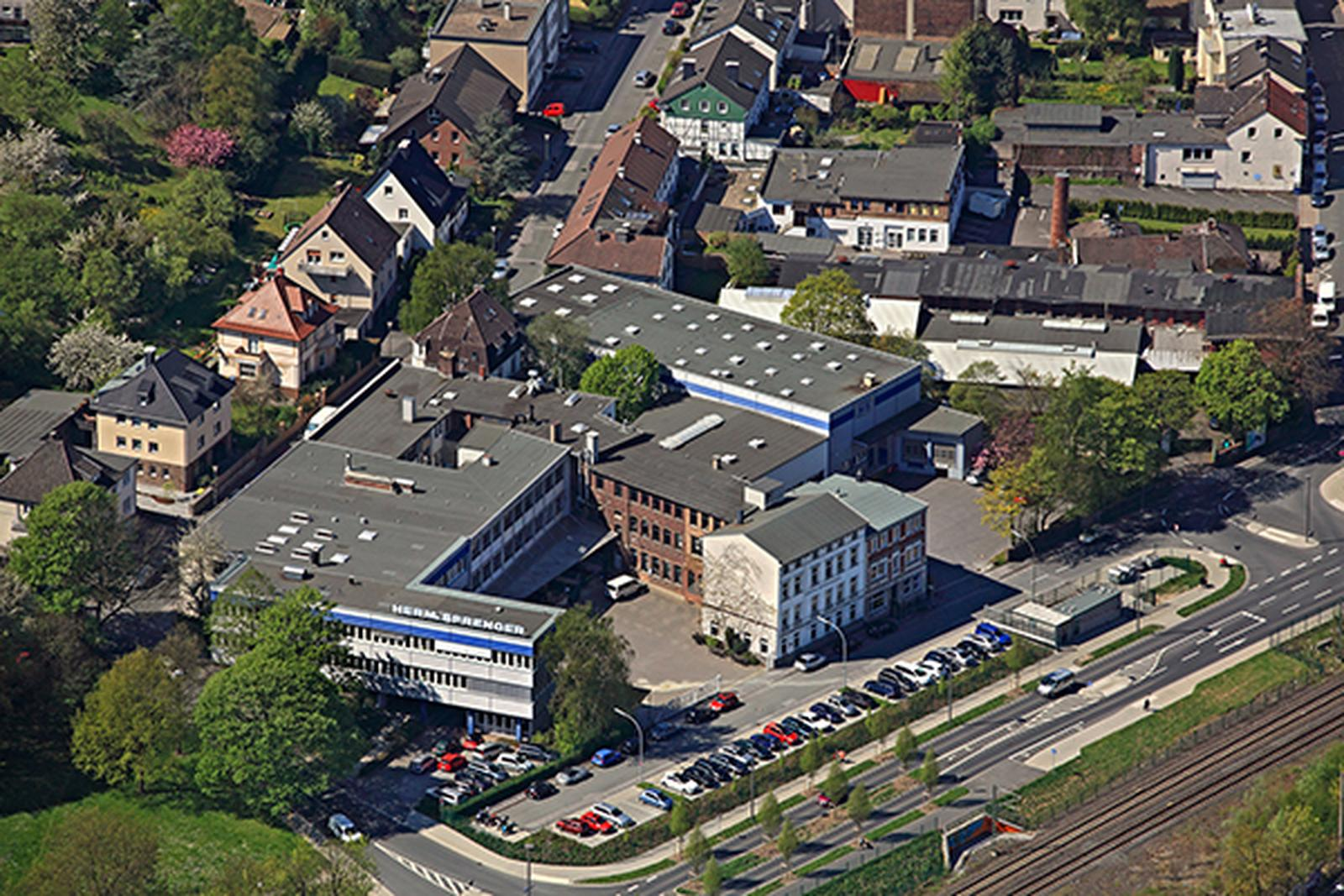
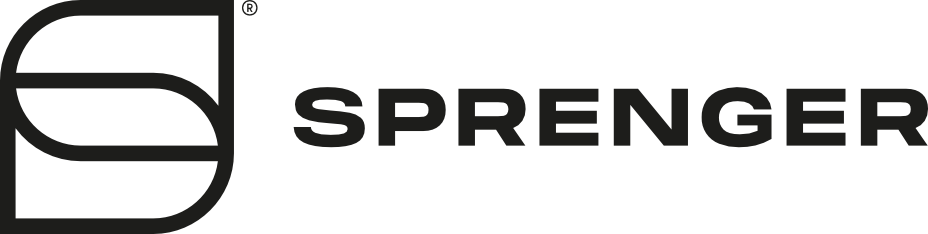
Our history, vision and values
SPRENGER has been manufacturing high-quality products for the equestrian, dog and boating sectors for 150 years. Founded by Hermann Sprenger in Iserlohn in 1872, we still operate as a family business today, now with around 200 employees worldwide.
Our products are still produced at our site in Iserlohn.
Quality and innovation
Behind each of our 3 divisions is a dedicated team of experts with unique know-how developed through decades of manufacturing experience. In order to continue to grow and develop new products, we rely on our long-standing cooperation with our partners in medicine, research and professional sport.
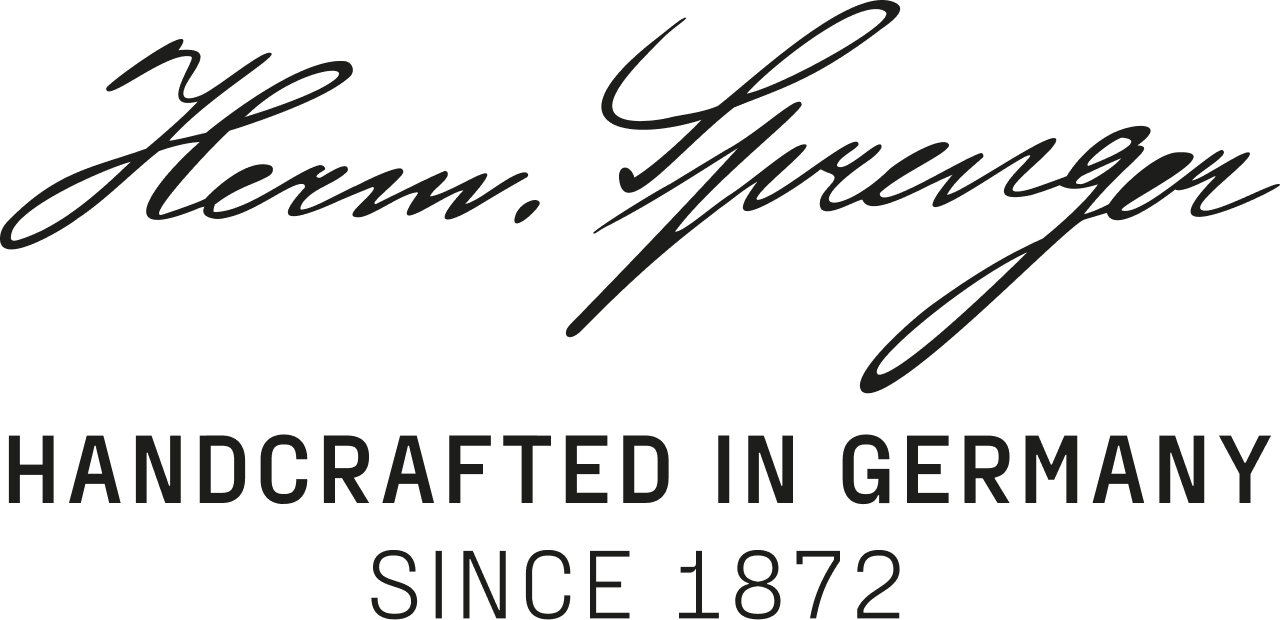
The history of the family business
In 1872, Hermann Sprenger founded a factory for horse and harness fittings in Iserlohn. Over the years, the production program was supplemented with boat fittings and dog sports articles. Today, Herm. Sprenger Metallwarenfabrik GmbH Co KG is a globally active family business with 170 employees, which is now successfully managed by the fourth generation. But we are not resting on our more than 150 years of experience: We strive to optimize our products and to develop innovative solutions for equestrian sports, dog sports and boating, with which our customers will continue to be successful in the future.
This is where our story began
1872 - 1949
The origin of everything
Ore is a material that only gains value through artful processing. In Iserlohn, people have always made use of this knowledge and forged. Even in the Middle Ages, the city's armored wire shirts were known throughout half of Europe. 800 years later, it was the spurs of the Hermann Sprenger company that found favor from Bosnia to Paris, from Vienna to Warsaw. Because, as we all know, the greatest happiness on earth lies on the back of a horse. But riding not only requires a horse, but also accessories from the saddle to the spurs. And our story begins with spurs.
1872
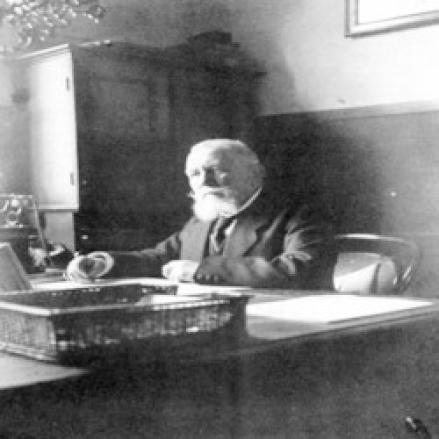
The foundation
In 1872, Hermann Sprenger founded the "factory store" Herm. Sprenger. He was involved in the sale of spurs, so he bought the forged blanks from Julius Ruck & Sohn, Westig, and sold them on at a profit. The spurs were ground in the Wilutzki grinding shop in Iserlohn.
This type of split production, further processing and storage on different sites led to all kinds of difficulties. A lot of goods were lost and one day the grinding store burned to the ground.
1872
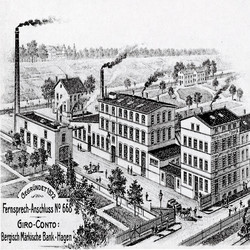
The new address
In 1887, the ground sank in Luisenstraße. The underground mining of ore made itself felt in Iserlohn's earth crust. First there was a crackling in the beams, then the walls collapsed. The Sprenger company moved. First to Hagener Straße and later again. Alexanderstraße 18-19 was the new address, which is still the company's location today.
A boiler house for the steam engine and a forge for spurs and horse bits were built on the first floor. The factories (management), filing shop and the "Cornptoir" were located on the second floor. The boiler house, which was built later, was the power source for the entire factory. A "locomobile" heated with coke generated high-pressure steam, which was transported to the steam engine in the factory building via a pipe at a height of approx. 3 meters. This drove a large disk wheel. This was used to drive all the larger devices and machines on the 3 floors via transmissions. The fast-moving leather drive belts for the rolling mill and the electroplating shop, as well as the lathe in the metalworking shop, all ran at a rapid speed that could only be regulated by dangerously switching the transmissions on and off.
Long iron bars were used for forging, which were heated in a coal fire. The heat of the forge fire was conveyed to the white heat with the help of a bellows operated by foot. The red-hot bars, 17-30 mm thick, were hammered under the drop hammer between the die halves, e.g. to form a bit or spurs. The drop hammer was pulled up to the roof of the forge with a leather strap and then brought down with a loud roar to shape the red-hot iron. The iron bar cooled after just 2-3 blows, so that multiple annealing was necessary until the shaped piece was in its raw state. The shaped pieces were punched out under a screw press, which were then ground, polished and coated with a protective layer of nickel.
The grinders were always thirsty and sang a lot, including the melody:
"Wir sind die Sänger vom finster'n Walde, Wir sind die Sänger von Herm. Sprenger's singers.
We grind spurs for the fatherland and if you dress up with spurs, they must be original Sprenger spurs."
1899
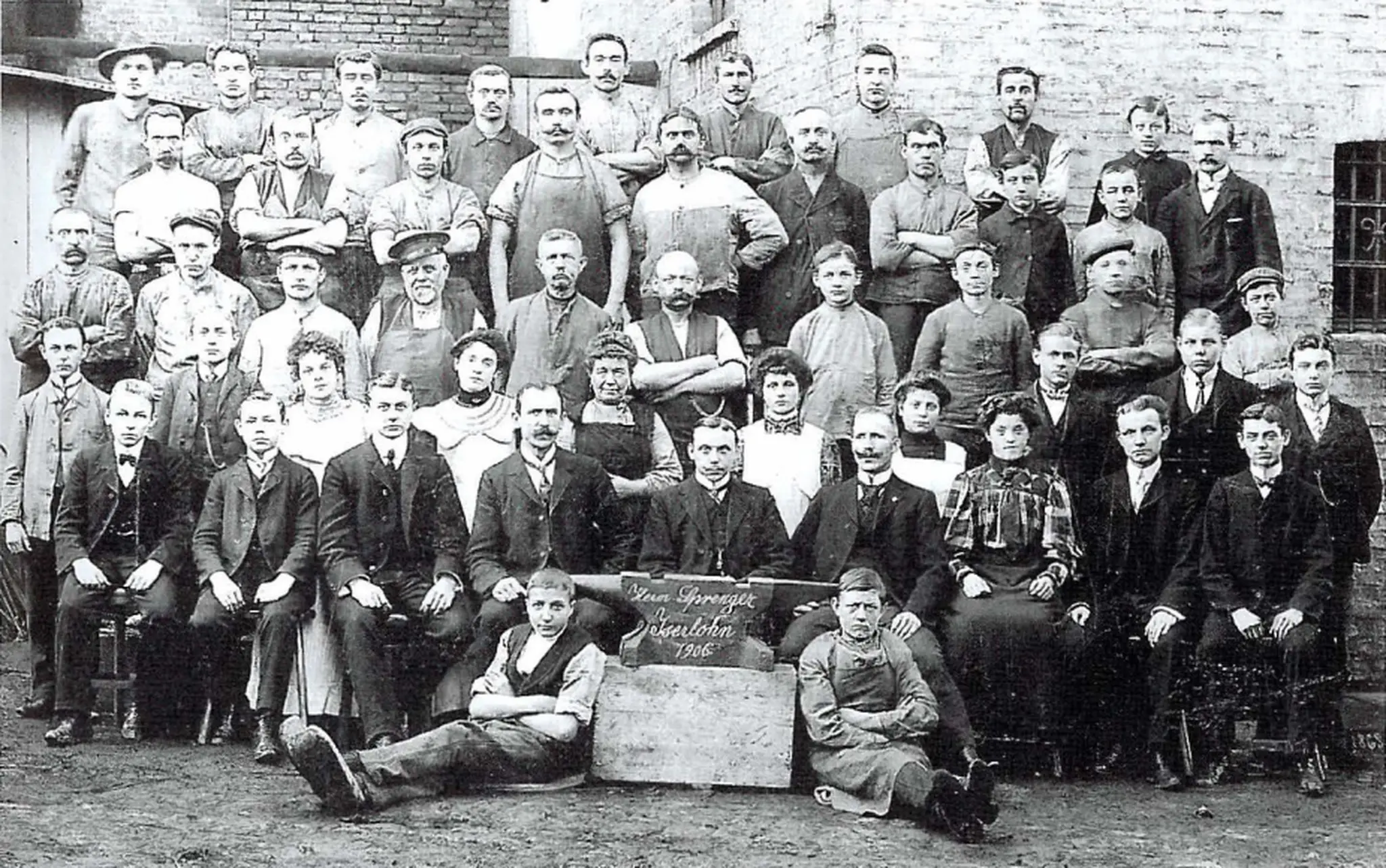
the new office building was constructed, which was more accurately referred to as the "Comptoir" or Kontor. The new office and warehouse building had three floors plus basement and ground floor, as well as a manually operated elevator for transporting goods.
1915
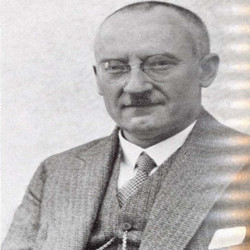
Heading
Use this text to share information about your brand with your customers. Describe a product, share announcements, or welcome customers to your store.
1918
In addition to snaffles, curbs and spurs, the manufacturing program included a wide variety of buckles made of wire and cast iron. Alfred Sprenger already offered and sold a wide range of merchandise. Trade kept the company afloat, while there was often trouble with the company's own production. A patent was filed for a "hand-washing case for car drivers". The contents consisted of a water tank with an external tap, soap, towel and nail brush.
1919
the company Herm. Sprenger supplied saddleries and canteens of the "100,000-man army" and the police with spurs, stirrups, snaffles, curbs, harness buckles and buckles of all kinds from its own production. But most of the turnover came from merchandise. These included all items bought by soldiers and officials in the canteens: Combs, scissors, soap and soap dishes, nail brushes, clothes brushes, pocket knives, shoe polish kits, shoe polish boxes, sewing kits, etc.
1922
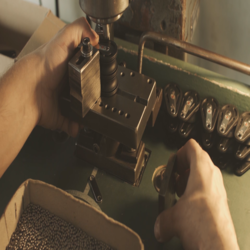
The post-war years demanded a change. Long-standing foreign customers were lost. Motorization replaced the cavalry. The production program had to adapt to the new times. Cactus stands and car wash cases were to bridge the gap. Sprenger even produced a hairdresser. Weft forks and weft rakes for weaving mills were added to the production range. Suitcase and folder locks were also among the new items.
But despite many efforts, not all jobs could always be filled. Times were bad. Of all the new products, only one area proved to be viable and promising: the manufacture of boat fittings. This has been maintained to this day and helped the company to new success.
In the factory, the old transmissions and machines were now running at full speed again.
1928
According to the company report of the South Westphalian Chamber of Industry and Commerce in Hagen, Sprenger manufactured spurs, stirrups, bits, carriage fittings, military supplies, snap hooks, dog sports articles, bridle buckles, belt buckles, belt buckles, suitcase locks and mass-produced articles of all kinds with great success.
Sprenger had 76 employees at the time, 48 of whom were blue-collar workers and 12 white-collar workers.
1932
Sales to Wehrmacht canteens after the rearmament increased merchandise sales many times over. Alfred Sprenger also bought a press, which was connected to the existing transmission to press side plates for cable drums. This was used by soldiers to lay telecommunications cables and power cables on foot.
1939
The drop forge was only put back into operation during the Second World War. Weapons and ammunition parts were now forged here.
1942

After the death of Alfred Sprenger, his two sons take over the business. Herbert Alfred Sprenger is responsible for the technical management and Reinhard Sprenger takes over the commercial management.
The company was converted into a limited partnership. Original Sprenger spurs, stamped with the well-known company logo "Anchor and Snake" had a worldwide reputation, so to speak.
However, the further development of the company was uncertain for the time being. This was not only due to the inadequate coal production, which meant that there was a shortage of electricity and iron, but also to the completely unclear currency conditions for deliveries already made to friendly foreign countries.
1944
Due to a company audit, a closure notice was issued for the entire Sprenger company on February 26. This decision was based on the fact that the drop forge was shut down on the day of the audit due to a repair. Furthermore, the company was completely outdated and had an inorganic structure. The working methods were inefficient and in some cases too manual. After lengthy negotiations, it was agreed that the drop forge could continue to operate unchanged and the production of spurs could continue.
The last three months saw serious changes to the production facilities. Air raids destroyed the transportation routes, the mines and the rolling mills. As a result, only very small quantities of coal and coke could be delivered, and even then only slowly. More by chance, two wagons of 17 mm round iron were delivered, while no other material came in. Work at the company suffered due to the many air raid alarms, which only abated in the last days of March. The electricity allocation was also reduced to 50% of the previous level. Gas had not been available since the end of February. Some goods were only received from nearby suppliers for the trading business.
The manufactured goods, in particular harness & rope sets, spurs and many other urgent items could not be delivered as all shipping was paralyzed. However, it was still possible to sell goods on the square to a certain extent, especially military articles, canteen goods, etc.
The trading business continued to decline as supplies of raw materials became increasingly scarce. A production instruction was issued for the manufacture of tableware fittings with a Wehrmacht order number for urgent completion.
The order backlog had not changed. Occasionally, during a company audit, the relatively extensive spur production was criticized. It was therefore intended to include the manufacture of snaffles, which were currently in particularly urgent demand, in the infantry armaments program.
Reinhard Sprenger did not yet receive a reply to his objection to the closure notice. However, three further audits were carried out. The company was left in the dark about the results of their deliberations.
The trading business had also continued to decline, as incoming goods were getting smaller and smaller. Efforts to secure urgent trade orders were only occasionally successful.
1945
There was no longer enough coal or coke to continue production. They made do with sludge coal. This was wet coal dust that was more liquid than solid and was "spooned" into the furnace with a coal shovel.
On March 13, air damage was caused by a bomb that fell on the Reichsbahn track diagonally opposite the office building at a distance of about 30 meters, as well as by airborne weapons fire from enemy low-flying aircraft. In addition to most of the window panes in the factory and the office building, the skylight roofs over the press shop and Scheuerei as well as the roof of the drop forge were damaged. Most of this damage was repaired by our own staff, which unfortunately brought the business to a complete standstill for four days.
There were now only minimal supplies of coke and coal. The supply of electricity was to be stopped completely in the next few days. As a result, it was impossible to continue working. In the factory, a toolmaker was busy making tools while other permanent staff tidied up, carried out machine repairs and made changes that had been due for a long time. Due to the priority given to the production of war-related products, they had not been carried out.
Due to the worsening of the situation, business operations at Sprenger had already been suspended on April 13, 1945. A resumption of production was dependent on approval from the Military Government Office, which only issued a few "permits" for urgent production. The relevant priority list also included fittings for agriculture, meaning that the production of tableware fittings formed the basis for a requested production permit to resume manufacturing.
A corresponding application was submitted as soon as possible, but approval was not forthcoming due to the amount of coal required to produce electricity.
The intention was now to manufacture household items such as frying pans, coal shovels, etc. In addition, the production of ashtrays in the shape of spores was started, which seemed interesting because they were highly coveted by the soldiers of the victorious powers as a souvenir of the defeated Germany.
In the last few months, tableware fittings were produced on a larger scale. Leather goods fittings had to be produced for retail outlets. Increasingly, customers were visited who showed great interest in all stocks, so that considerable sales could be made from stock.
A new manufacturing goal was attempted through the production of household articles.
Around September 1945, the British occupation granted the so-called "small permit". The company was now officially allowed to manufacture and trade. Sales were based on the last 1938/15 catalog, which also included some dog sports articles. The small stocks were soon sold.
Despite efforts to obtain direct orders from the British Army of Occupation, Sprenger did not yet receive a production permit, the requested "large permit", but small items were produced by hand, including aluminum ashtrays. In the trading business, Sprenger received larger orders for leather goods fittings as well as steel goods and other items. The financial situation had improved because some of the goods originally produced for the Wehrmacht were sold elsewhere.
There was an intention to manufacture electrical appliances such as waffle irons and cooking appliances in collaboration with the ROTI company (Ober-Ing. Rohrmann and Ing. Tillmann), but the project initially failed due to the unsecured procurement of the necessary accessories and the electricity restrictions imposed by the military government.
The drop forge resumed regular production of snaffles. In September, a gas furnace for gravity die casting arrived. It was to be used to produce aluminum mane combs and other light metal gravity die castings.
1947
In the spring, we received iron purchase vouchers. Although this made it easier to procure materials and ironware, we were increasingly "compensated", i.e. the goods were invoiced "normally", but an additional amount was paid "in the black", or we received food in exchange, which was distributed among the workforce. Some customers gave us products they had made as "freebies": Suitcases, briefcases or purses. These were passed on to the suppliers in exchange for new raw materials.
The unrestricted production permit finally arrived on January 3, 1947. This was followed by the first coal allocation in February. This was of great importance, as the winter was extremely cold and long. In addition, there was a complete blackout of all electricity for about 4 weeks. During this time, only assembly work could be carried out.
The production of wooden sandals was started in mid-June. The necessary machines, in particular a band saw, were manufactured in-house.
Sales of manufactured goods continued to improve, which was also due to the well-developing sandal production. However, there were great difficulties due to the lack of labor and suitable wood. It did not seem necessary to obtain a production permit for this, as no further production permits were currently being issued due to a lack of materials.
The company Herm. Sprenger manufactured wooden sandals for men and women and advertised this footwear with flyers. Anyone who wanted to have a pair of sandals made had to deliver suitable leather for the upper material of the sandals, such as old leather from briefcases.
The production time was about 14 days after delivery of the leather to the factory management. This sandal production only succeeded because most of the wood required for the soles was supplied by the wood sawmill of Mr. Dürr, Herbert Sprenger's father-in-law. This production did not generate much profit. Nevertheless, it provided the entire company with the orders that were temporarily lacking.
It was also possible for the first time to produce small cast buckles, for which there was a particular demand. Small quantities of brass harness fittings could also be produced; however, the production of carriage harness fittings made of argentan failed due to a lack of material.
In the long term, the production of horse harness fittings in its present form did not promise full utilization of the company. The intention was to produce further fittings for the leather goods industry itself.
1948
The trade fairs in Hanover and Leipzig were visited in the spring to examine the opportunities for export and international business. The sandals remained popular "barter items".
From June 21, 1948, the day of the currency reform, everything changed.
Until then, customers had come to ask for goods, but now "the suppliers were running us ragged". After just 14 days, nobody was asking for iron coupons any more. The coveted new German mark regulated the movement of goods. We introduced a stock register, as the stockists' demand reports often arrived too late, sometimes only when there was nothing left in stock. With the currency reform, the production of wooden sandals was discontinued.
In September, the supply of production materials improved. In particular, it was possible to purchase brass and nickel silver for the manufacture of horse harness fittings.
The backlog in the supply of dressage necklaces purchased from Wilh. Naumann in Iserlohn was unbearable. In order to better meet demand, the company came up with the idea of manufacturing these items itself. The company set up a production system for dressage necklaces made of 3 mm wire.
1949
The company manufactured and traded under the motto: "Everything for the dog!" There were hardly any horses left and, of course, only a few riders. Corresponding orders were received, but it was not easy to fulfill all requests. Straight pieces of wire, rounded at the ends, were required for three different link sizes. These pieces of wire were bent into links in four to five operations, an expensive and difficult process, but it was soon possible to fulfill all the dog owners' wishes. The modernization of the factory facilities was now the main goal of the management. An iron will, the courage to take risks and the personal thriftiness of the owners made further purchases for the factory and its modernization possible. Soon a powerful electric motor could be used to drive the transmissions instead of steam power. After many years of detailed work, all machines were gradually equipped with electric motors by the beginning of 1949.
Herbert Sprenger received pleasing orders on his trips to the USA. Customers ordered large quantities of chains of various lengths and features. Reinhard Sprenger in particular received large orders for riding and dog sports on his travels through France.
The exhibition at the Leipzig Spring Fair was very well received by customers. As part of a special agreement for the Leipzig trade fair, official business was conducted with the Eastern zone for the first time.
Sales to the Eastern zone and to Berlin were insignificant. The financial situation of customers in Berlin was very weak, so that sales could only be made with great caution. On the other hand, due to the low exchange rate of the Ostmark, it was now possible to buy the portfolio locks that had previously been purchased there from the Eastern zone via Berlin. Our company was therefore in a position to undercut the West German manufacturers.
1950
The end of the 1940s saw Germany's first economic upswing. The word "economic miracle" is used. Those who work hard also need leisure. Another magic word of the 50s becomes a term: hobby.
Sprenger recognizes the trend early on and reacts: Articles for dog sport and care.
Then one day came a big shock for sales to America. The company from which the chains were welded and purchased ready to bundle was offering similar processed, nickel-plated and chrome-plated chains in the USA at prices at which we were selling the unprocessed raw chains.
We then had to look for ways to obtain cheaper chains. Herbert Sprenger brought an electric welding machine into the company. This could be easily adjusted to different welding thicknesses and welding times. The electric welding of rings was quickly successful. Individual chain links could also be welded.
Sales of dog chains continued to improve. The newly created attachment chains in particular, especially the 2.0 mm thickness, became a real hit. The production of dog leash tongs began. For several years, malleable cast iron served as the basic material, which was sourced from foundries in the Solingen area. Eventually, the key factories in Solingen supplied more precise and easier to process castings. The disadvantage, however, was the greater fragility of this material. During use, the gripping parts often broke off at the front. For this reason, attempts were made to stamp the dog lead tongs from wire.
Time and again, efforts were made to commission items that would be of more important and lasting significance. For example, Herbert Sprenger succeeded in obtaining an order for the electrification of the railroad. These were cramps made of Kuprodur, which held the railroad's overhead power lines. An unusual degree of precision was required. This could only be achieved through several work steps. Gauges were used to measure piece by piece. The Kuprodur material had to be purchased from the same company that was already manufacturing these cramps. This company also took delivery of the finished goods and delivered them to the Federal Railways.
1951
exhibited Herm. Sprenger at the Frankfurt trade fair. It was there that Mr. Arthur L. Rosenei, head of Reliance Intern. Pet Supply from New York, discovered our company. Mr. Rosenei was impressed and ordered larger quantities. Reliance Intern. Pet Supply is still a customer of ours today.
The order for knotted chains justified the purchase of the first and only knotted chain machine. It was designed for wire thicknesses of 1.4 to 1.8 mm and could already be put into operation in the second quarter without any problems.
In the summer, the first trials were carried out for the production of dog metal combs, both for dog grooming and for the worsted yarn industry. A pensioner from the Bavarian Forest, who had produced such combs in a Thuringian factory until the end of the war, explained the soldering process and the trick of preventing the liquid solder from bonding with the metal back when dipping. We had bought these combs there ourselves in the past.
1952
The manufactured nickel-plated brass combs were too expensive. A cheaper solution had to be found. They wanted to make the needles themselves. The idea of chafing both wire ends round was the right one, but the first attempts were disappointing. Most of the needles came out of the barrel bent. Nevertheless, it was enough to make several hundred combs that could be shown as samples at the Frankfurt trade fair. The iron combs rusted easily and there were complaints. The management then heard about a paper factory in Aschaffenburg that produced rust protection paper. The paper was coated on one side. This coating gradually evaporated and what it released into the surrounding air prevented rust from forming.
1953
There was increasing demand for HS products from abroad.
In spring, a new, larger bright nickel bath was installed in the electroplating shop. Another chrome bath was added. As a result, the old transmissions were gradually dismantled. Presses and machines were individually driven by electric motors. Towards the end of the year, AEG delivered the first electric welding machine for pull-through chain rings.
1954
The cramped conditions on the 2nd floor of the production building meant that the old grinding facilities had to be demolished; the new grinding blocks took up considerably less space. As a result, chain assembly was able to expand further. Herbert Sprenger, always on the lookout for something new, developed a double chain.
1955
As the chain suppliers of Herm. Sprenger increased their prices by 25%, the management decided to manufacture all the chains themselves. The walls of the Scheuerei and the Galvanische Anstalt were raised up to the 2nd floor. These structural changes expanded the electroplating department and created clearly laid out rooms on the 2nd floor, which then made it possible to expand chain production.
1956
There were two chain manufacturing machines for light and thicker chains and two electric chain welding machines in a special room that was always locked. This facility overcame the great danger of the company's dependence on suppliers. The newly developed manufacturing process was not patented. There was a fear of imitation with minor modifications. In fact, there was no other manufacturer of electrically welded dog chains for many years.
1958
The long-standing difficulties with the metal foundries were alleviated by the addition of two further suppliers, which was particularly important because orders for boat fittings were received on a much larger scale than in previous years.
The many delivery problems in recent years were due to insufficient stocks. Now that appropriate stocks had been acquired, it became apparent that there was a lack of space everywhere in the factory and warehouse. The purchase of an automatic chrome plating system was also planned. However, the number of staff could not be increased so easily. There was no longer sufficient space available. So the decision was made to build another extension along Weidenstrasse.
Engravers in Lüdenscheid produced the first tools for dog lead tongs with a service life of 50-100,000 pieces. A spark erosion and professional surface grinding machine were also purchased.
In the third quarter, employment increased even more. This was due not only to the extensive chain business, but also to larger buckle orders from the USA. The season for boat fittings remained unchanged and demand for equestrian products also remained strong. New workers were hired on a large scale, so that the number of workers and employees exceeded 100 for the first time. Space was at a premium, especially in the packing room and dispatch department. There were plans to build a hall in the garden between the locksmith's shop and the drop forge and to extend the washrooms to the east next to the drop forge.
1959
was characterized by a boom in boat fittings. Although sufficient raw materials and semi-finished goods were available, not all customer requirements could be met. Bottlenecks arose above all in the recruitment of workers because the employment office was unable to offer any more employees for placement due to the generally good employment situation. Increasing the workforce was also ruled out because there was no longer enough space in the factory. The problem of a new building became more and more urgent, so that the construction of a three-storey building with a built-up area of around 900 square meters was carried out next to the Scheuerei.
1960
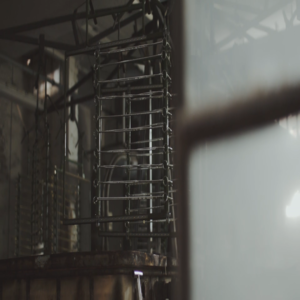
In the meantime, customers knew that Sprenger chains were now being electrically welded. Suspicious buyers initially complained that the welding was not complete. A device was therefore constructed with which the chains could be torn and at the same time the tensile stress under which the breakage had occurred could be determined. The result was very satisfactory; the breaking strength of the electrically welded chains was always higher than that of the autogenously welded chains.
Plans were made to purchase additional chain and welding machines. The existing plant was working to capacity and additional skilled personnel were no longer as easy to come by as before. As a result, a new, automatic chrome-plating plant had to be built in the metalworking shop, in which the various sinks and the actual chrome bath were arranged in a circle. In the middle was a column with a rotating ring, from which spoke-shaped arms extended to the individual basins, which held the racks with the goods to be chrome-plated. The racks were moved from basin to basin in a certain cycle, dipped in and then lifted out again until the process was complete. The system looked like a carousel, which is what it was and still is called today. Above all, it was very practical. There was no need to walk from basin to basin. One worker was enough to operate the system.
To solve the transportation problem in the factory, an electric goods elevator was ordered.
As orders for dog chains from the USA declined somewhat, the heavily depleted stocks were replenished. In the summer, the chain business picked up with orders from Europe and Germany. However, new difficulties arose. The malleable iron foundries, above all the Vereinigte Schlüsselfabriken, delivered only sparingly. The foundries ran out of molders because they could earn more in construction or industry. Sprenger was no longer able to accept orders for cast buckles and rings. All this was unsatisfactory and such a situation was not sustainable in the long term.
Herbert A. Sprenger therefore returned to his "old" idea of producing the pliers blanks under the press (cold forging). Initial tests had already been carried out in the old press shop with a double toggle press and a beating press. Wire sections were cut off under an eccentric press, placed in an embossing tool, pressed and the burr removed with a cutting tool. At the time, these tests did not yet produce a final result. The hinge pins had not yet fully emerged - but showed that it was feasible. There was still no shortage of raw castings, which were still very cheap at the time. But the situation quickly became precarious. The foundries had to increase wages to stop staff turnover. Above all, however, there was a shortage of raw materials. This threatened the existence of the dog sports business and even the entire company.
Sprenger was now seriously considering switching to a new production facility. Engravers in Lüdenscheid were commissioned to produce the first tools with a service life of 50-100,000 pieces. Meanwhile, the toolmakers were to prepare the subsequent steps for sliders and swivel eyes, followed by the deburring tools.
It was not until the second quarter that production of the pressed tong hooks got underway. HS found that not every tool was able to withstand the intended service life. The toolmakers were working at full speed. To make things easier for them, a spark erosion machine was commissioned, which automatically worked the engravings into the tools. A new press with 160 tons of pressure was also ordered for the production of tong hooks.
Chain production worked in two shifts from the third quarter onwards in order to meet the increased demand. Cast swivels for the dressage necklaces were also no longer available. They had to be bought in and produced on a welding machine set up especially for this purpose.
1963
The first flat shackles made of 4301 stainless steel were purchased from the Höcker company. One year later, these shackles were manufactured by machine at much better prices.
1964
Sales of dog articles increased to such an extent that chain and welding machines had to work in two shifts. Two new chain and welding machines were ordered, as well as a new wire bending machine with a much larger capacity for the production of links for dressage necklaces. A new automatic surface grinding machine was also purchased for the tool shop.
The Messmann company became the best customer, a Grökaz (biggest customer ever). The new brand name "Kessi" also brought great success. The pliers hooks, almost all chains and many other accessories were purchased from Sprenger.
1966
New stainless steel and plastic boat fittings have been developed in recent weeks and were presented at the boat show in Friedrichshafen in October. These were yacht blocks made of 4301 stainless steel with plastic rollers.
1967
The harness fittings went quite well. Complaints about the nickel plating of the argentan fittings, which had been carried out for several years, became so frequent that the process had to be abandoned. As a result, the fittings were supplied in skin packaging, which provided extensive protection against tarnishing.
In equestrian products, a bridle and stirrup made of stainless steel were launched. In boat fittings, the selection of stainless steel fittings increased considerably.
1971
The production of hollow snaffles made of stainless steel began and was patented. With the DGBM application (German utility model application) of March 1971, Herbert Sprenger registered water and olive head snaffles made of stainless steel, cut from wire and sleeves. However, Japan and Taiwan copied this world first at a lower price.
The work preparation department began to work with an Ormig machine. This printed the work plans and provided the skeleton for the calculation.
1972
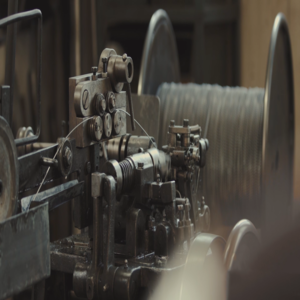
the year of the 100th anniversary.
Almost every competition rider knows the quality products from Iserlohn. Yacht and boat fittings also remain a specialty of the company. Thanks to many years of experience, this sector has been continuously expanded. The sales curve has risen steeply, especially with stainless steel items, which are preferred for equipping regatta boats due to their corrosion resistance and lightness.
So it is not surprising that Sprenger products were also included when it came to Olympic medals in 1972. We supplied the riding shoes for the modern pentathlon and the shoes for the Finn boats.
However, the sector of dog sports articles and snap hooks of all kinds became the leader in Sprenger production. Almost four million meters of dog chains have been manufactured and delivered in recent years.
Further processing up to the packing room could only be accomplished in two shifts. The electroplating shop was expanded with three new nickel baths, a centrifuge and a rectifier. In addition, new polishing barrels were installed in the intermediate hall built in the atrium of the Scheuerei. To expand the production facilities, work began on another new building in October. Two storeys were to be added on top of the plant management and the last gap in the building on Weidenstrasse was to be closed with three storeys.
There were further increases in production, so that more and more home workers were employed throughout the area.
1973
The new IBM System/3 computer was put into operation at the beginning of January.
1974
Business with harness fittings was particularly good in Germany. Stainless steel snaffles showed an above-average increase in sales.
In exports, boat fittings saw an increase, with the biggest rise in sales of stirrup bars.
This year, Sprenger launched a new bow made of zamak injection molding in a chrome-plated version, which was so inexpensive that it could now compete with all imports.
1976
For the production of bridle buckles made of stainless steel wire, a Bieler wire bending machine with electric welding was purchased, with which other articles could also be produced.
The company Julius Huck & Sohn had decided to withdraw from the equestrian market. Sprenger took over sales to its customers.
1978
The new high-bay warehouse was completed and occupied from October 15. It is 40 meters long, 18 meters wide and 10 meters high. The shell provided space for three small parts warehouses, with 2,750 compartments that can hold loads of up to 250 kg. The cycle time of the order picking devices is less than 60 seconds for each goods drawer for outward and return transportation.
1982
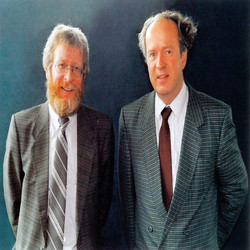
Klaus Rainer Sprenger and Peter Sprenger took over the management of the company. Herbert A. Sprenger and Reinhard Sprenger stepped down and only acted in an advisory capacity.
Despite the general recession, which forced many companies to reduce working hours or even close down, Sprenger's sales had held up. There were only slight declines, which were offset by increases in other departments.
A patent application was filed for the new pulling cramps.
1983
A rope brake was developed and successfully tested at the Admirals Cup under the name "Diad Stop" (Dieter Adomeit, Berlin). This brake held the rope with normal force and could be released again without great effort. The sailor could control the opening and closing of the brake. Furthermore, the safety against unintentional opening and thus release of the rope was guaranteed. Sprenger quickly introduced a complete surfing program from the Dutch company Kubus, Naarden.
In addition, the "Nopp bit" was developed, which caused the horse to play with the inserted copper parts. This stimulated salivation and the horse chewed better. This chewing was necessary for the horse to be able to ride consistently. This is comparable to "warming up" an athlete.
A patent application was also filed for the Meroth multi-purpose safety stirrup with a single joint.
1987
In boat fittings, the new sheet clamps with roller bearings were now also to be added to the product portfolio in 8 mm.
Fax transmission was recently introduced to speed up contact with customers and suppliers. The Miacs software was also introduced. This was a product planning and control system (PPS) from Honeywell Bull with inventory management, parts list management, standard costing and cost simulation, order requirements management, net requirements calculation, work plan and production equipment management.
Mr. Reinhard Sprenger died on June 4.
1988
The International Equestrian Corporation (IEC), which also included Cottage (GB), Skan Horse (DK), Foxwood (USA), Cavallier (CAN), International Saddlery (AUS), Ukal (F), Ageco Weco (B), Zaldi (E), Tattini (I) and Jansen (NL), elected HS as a member. It was hoped that this would lead to improvements on the supplier and customer side.
1989
Sprenger received an order from the German Armed Forces for boat fittings.
1992
Sprenger exhibited a new ball-bearing traveler at Mets (Amsterdam).
The company also bought Kannemeier & Koch in Langenhagen and now sold the KK bits exclusively and directly.
The new high-tech plastic sheet clamp was well received by the boat builders Mader and Hein. The larger Traveller II was tested in Holland and was to be presented to German boat builders in October.
Sprenger held his 1st Western Seminar with 150 people. Mr. Risley, a Foxwood employee who builds western saddles, came from the USA for the demonstration. Two tents were set up and four horses were used in the yard to demonstrate Western saddles.
1993
The newly developed metal alloy Aurigan was registered as a patent. According to the expert opinion of Professor Dr. Happke and a toxicological report from the University of Veterinary Medicine Hanover.
1994
Distribution of paints from International as one of 8 paint wholesalers.
At the Interzoo in Nuremberg, which takes place every two years in May, HS presented the new K-Collar, from the US licensor Klein as K-Collar, which was well received.
A modern rolling mill was set up. In addition to savings through reduced travel times, better working conditions were also expected. A new paper press was purchased.
1995
an equestrian seminar for 100 retailers was held at Sprenger. The main focus was on product training, including western saddles and bridles, and a tour of the factory and warehouse.
New stainless steel hinges and tie-downs were presented at the Mets (boat fittings trade fair).
At Interzoo in Nuremberg, the protected Wings toggle and the patented Curogan chain, which protects against discoloration of the dog's coat, were presented as new products.
1997
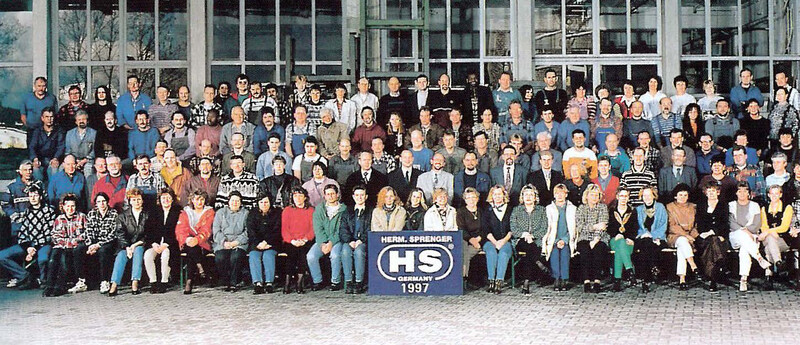
New sheet clamps and micro-blocks were successfully presented at the Hanseboot in Hamburg and at the Mets in Amsterdam.
1998
the System 4 stirrup with double joint was introduced. The stirrup has a movable tread surface that automatically moves the rider's heel into the desired low position. In addition, the rider can get out of this stirrup much more easily in the event of a fall.
1999
The Kannemeier & Koch bits were further developed into the new KK Ultra series. The anatomically adapted mouthpiece is particularly comfortable for the horse and promotes suppleness, as the rider can work more sensitively.
2001
Conversion of the dance hall into a connecting hall between the packing room and warehouse.
2002
Book publication "leading with feeling".
2005
Klaus Rainer Sprenger stepped down from the management team.
The Dynamic RS bits were also added to the product portfolio. These bits can be the solution for horses with leaning problems. Thanks to the ergonomic shape of the mouthpiece, it sits very well in the mouth, gentle pressure is evenly applied to the tongue and tongue edges and optimum chewing is encouraged.
2006
Bow Balance is the new addition to the Sprenger product catalog. The BOW BALANCE stirrup combines several aspects that make for good and safe riding. Thanks to the special balance and the curved shape in the upper stirrup area, it sits even better on the horse and is therefore easier to pick up. The proven System 4 joint can support the release of the foot in the event of a fall.
2009
The patent-pending NeckTech is the first stable and reliable alternative to the traditional training collar. By imitating the dog's canine teeth, this chain collar exerts a natural influence on the dog.
2010
prompted SPRENGER's research and development department to design its own stainless steel buckle. The patent-pending ClicLock offers advantages such as a sturdy stainless steel housing, a high-quality, seawater-resistant plastic part and a guaranteed breaking load of 200 kg. Other companies are now also using the ClicLock in their production.
2012
Purchase of Alexanderstrasse for additional employee parking spaces.
2013
With the SENSOGAN® bit material, SPRENGER has succeeded in consistently further developing the Aurigan material mix. In the new alloy, the positive properties of Aurigan have been enhanced and even greater compatibility with the extremely sensitive horse's mouth has been achieved. The special feature lies in the balanced composition of copper, manganese and zinc. The amount of copper released into the horse's saliva is greatly reduced by manganese, which means that the noble white gold color is retained for much longer. Manganese is an important trace element that is important for the development of connective tissue and muscle and energy metabolism, among other things, and can have a positive effect on stress reduction. Manganese also breaks down histamine and can therefore help to prevent allergic reactions.
2014
Introduction of the S-block series. The type of bearing used and the maximum cordage strength can be seen at a glance on the dimensionally stable stainless steel tab.
2016
Martin Sprenger supports his father in the management.
2017
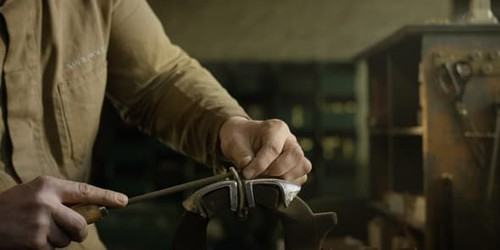
Our company has been working with the Iserlohn workshops for many years, with the result that a separate department has been set up within the company this year.
In terms of product technology, the Flexcite complements Sprenger's articulated stirrups. The latest generation of articulated stirrups is perfectly balanced for an optimal and safe thigh and foot position and has a shock-absorbing and gentle effect on joints, ligaments and menisci. It also makes it easier to release the foot in the event of a fall. The modern design makes the Flexcite stirrup in elegant silver/black the top model of the articulated stirrups.
However, it is not only our products that are becoming more modern, but also our sales department. Since this year, our customers have been able to place their orders in the new B2B online store.
In addition, new high-bay warehouses and a more modern and therefore faster order picking system are being added to the warehouse.
Despite all the difficulties, Herm. Sprenger managed to become and remain a well-established company thanks to the hard work of its loyal workforce and the great commitment of its shareholders. Even today, the company in Alexanderstraße in Iserlohn still manufactures its products, traditionally by hand.
The SPRENGER Magazine - Guide for dogs, horses & boats
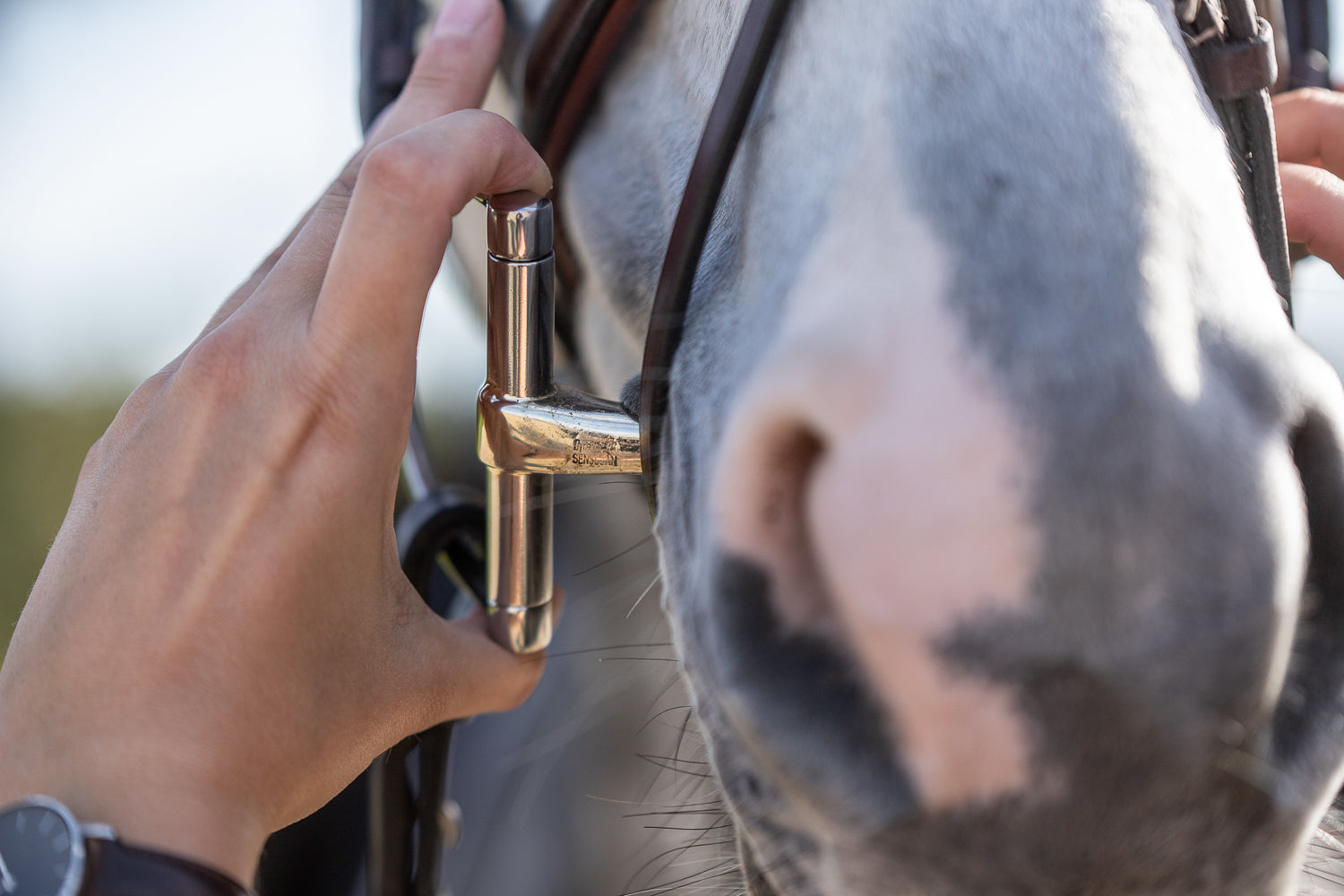
Why is choosing the right bit size so important? And how do I know which size is right for my horse? We answer these questions in this article.
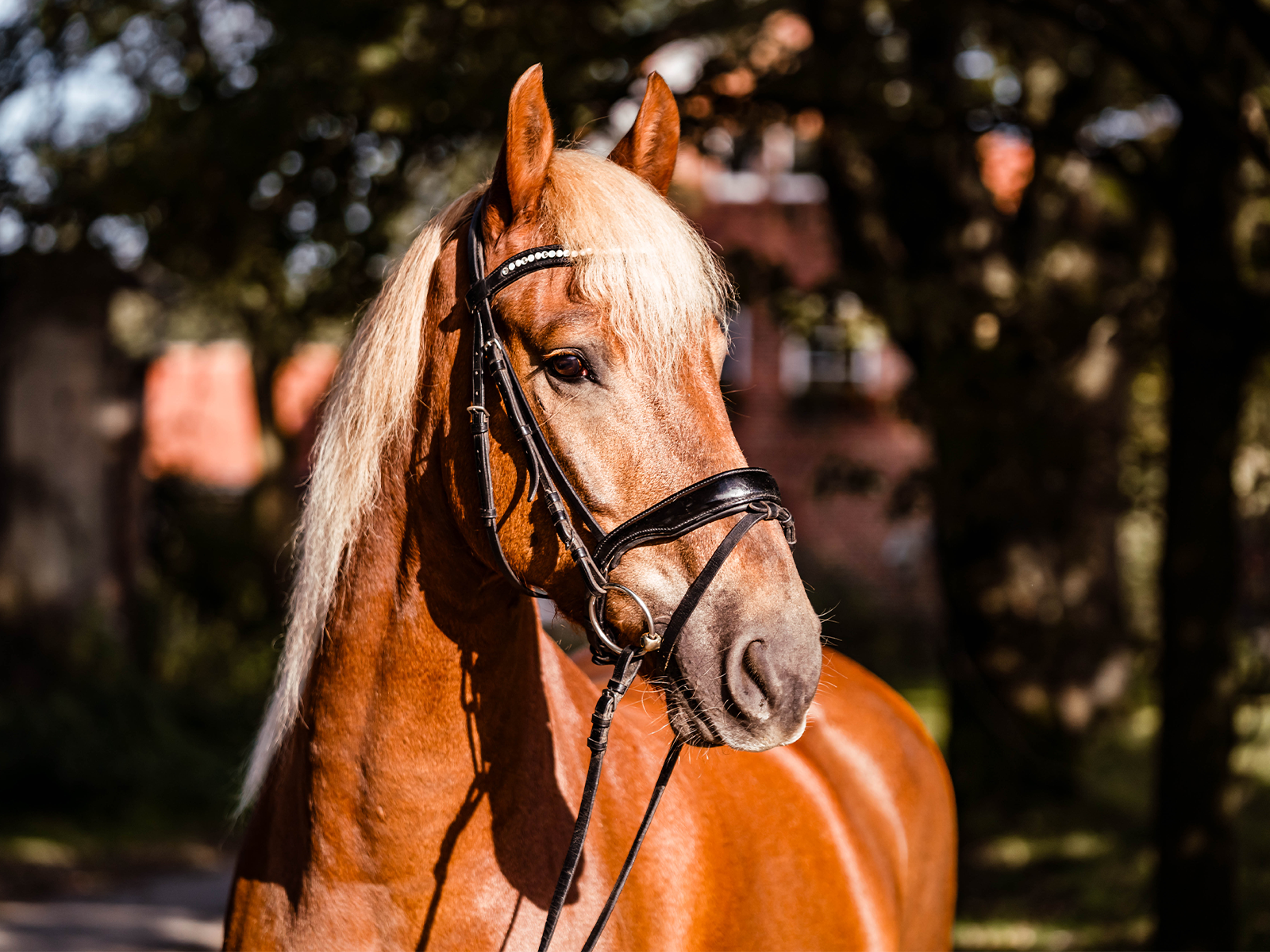
The Many Benefits of Equestrian Sports: A Holistic Approach to Personal Growth
Equestrian sport is much more than physical activity - it strengthens fitness, mental health and social skills and has a particularly positive effect on the personal development of children and you...
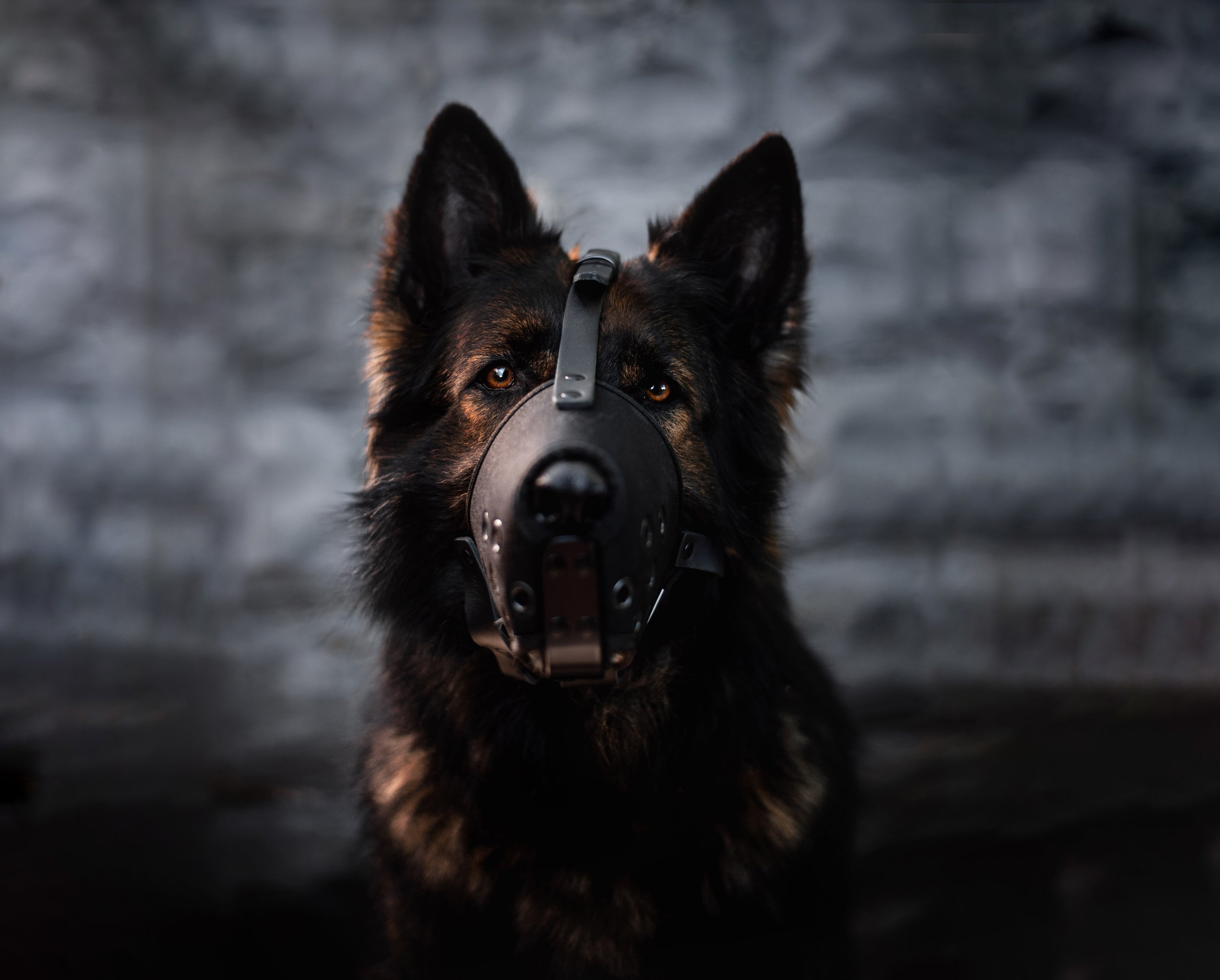
Muzzles for dogs often have a bad reputation and are associated with negative stereotypes. Find out everything you need to know about muzzles here!

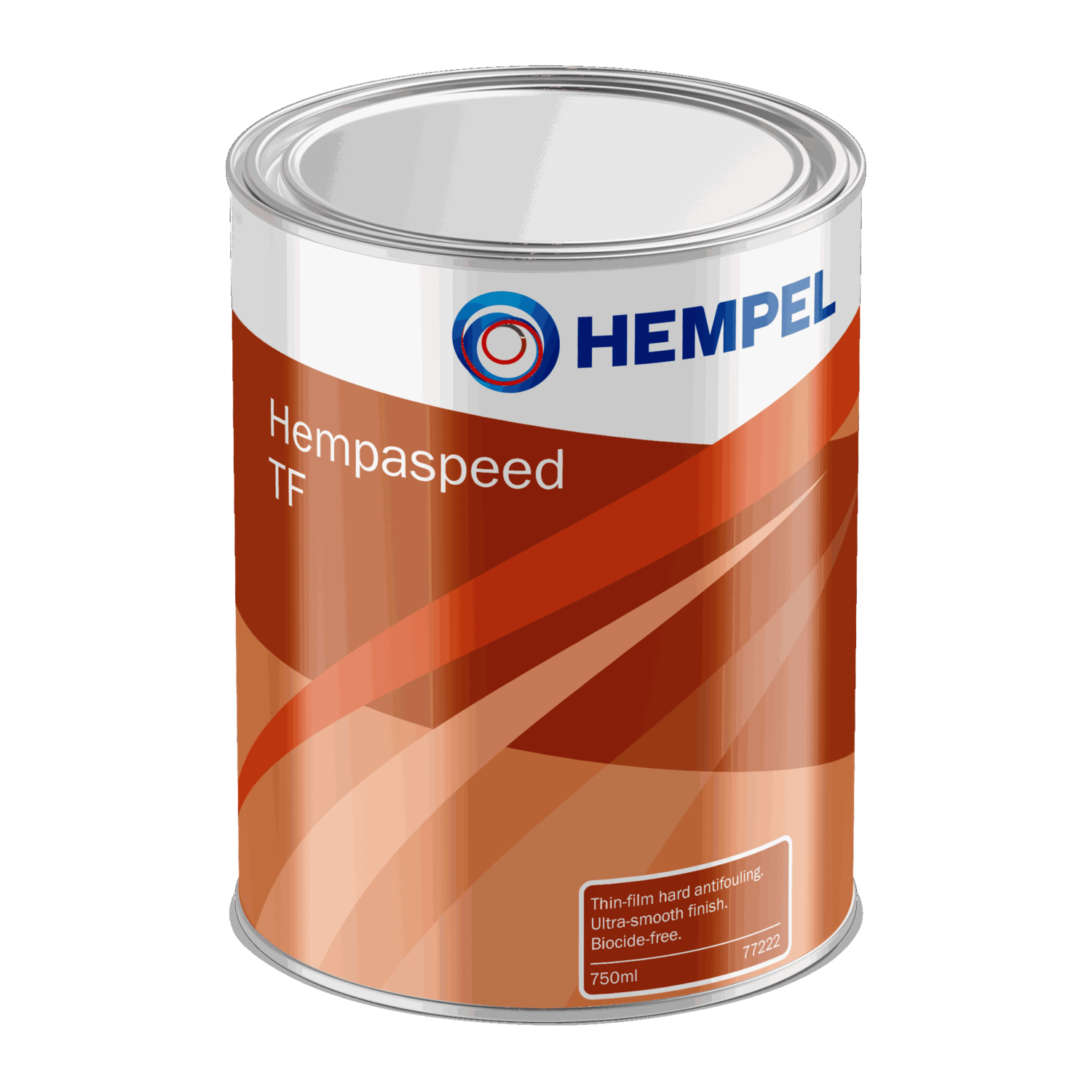
Hempaspeed TF - The innovative solution for antifouling coating according to VC 17m
How can VC® 17m be simply painted over? And what options do I have if I want to apply a sustainable, biocide-free fouling protection? In our article, you can find out everything about the VC® 17m b...
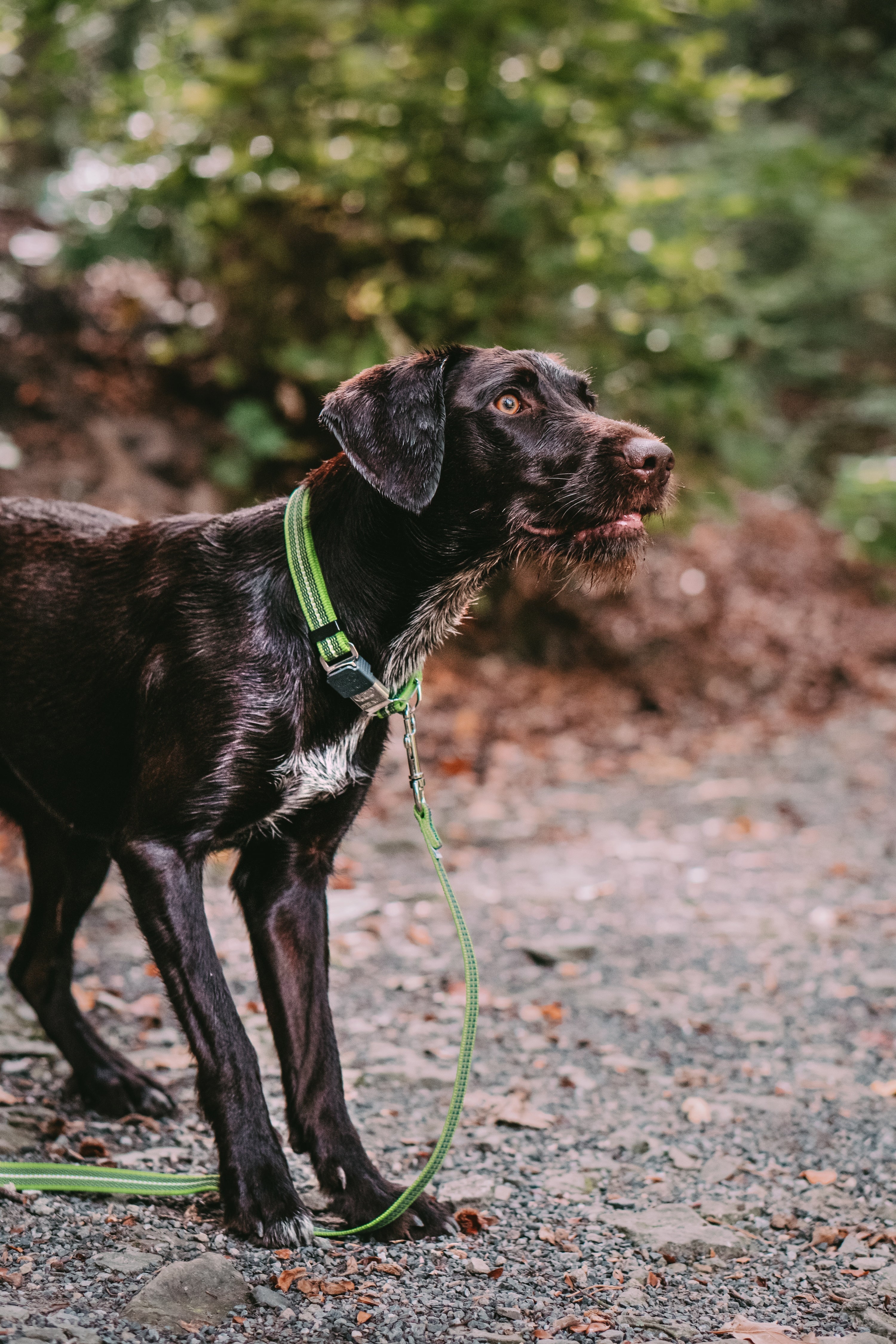
Unsicher wie Du die Halsbandgröße Deines Hundes herausfindest? Unser Blogbeitrag verrät es Dir!
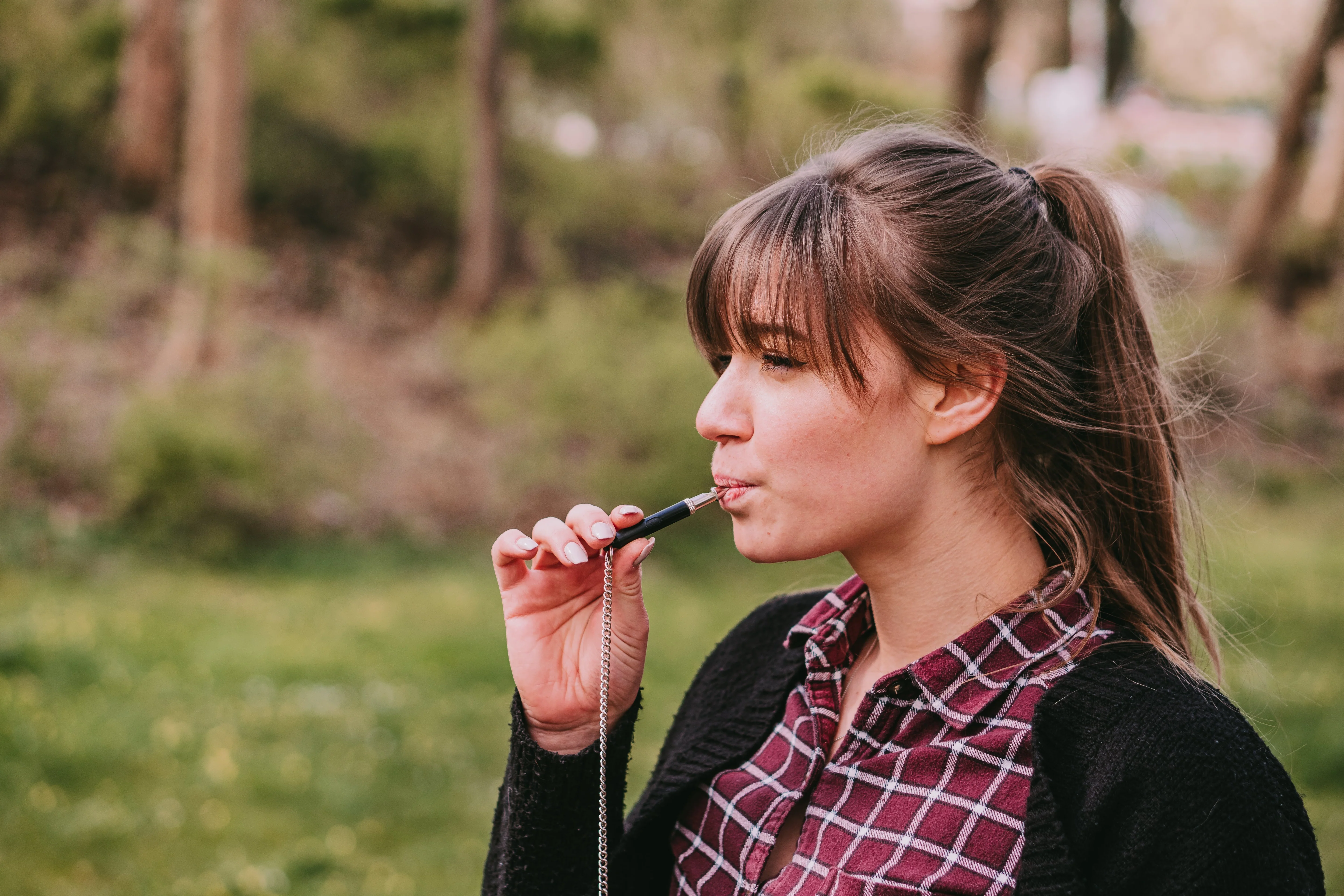
The dog whistle - your perfect training tool
The dog whistle is a great tool for dog training. Find out exactly how it works and what you need to know about the dog whistle here!
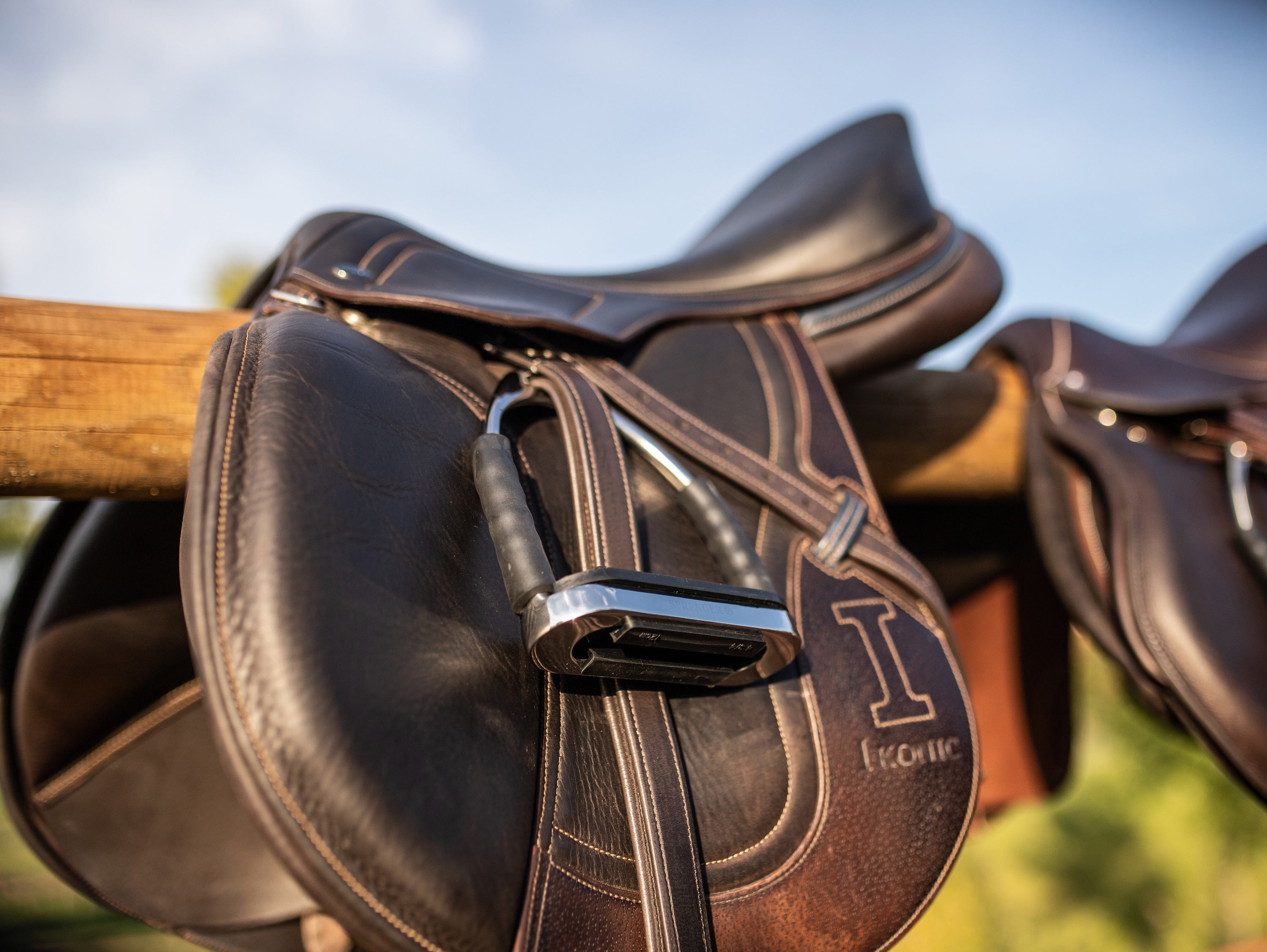
SPRENGER System 4 Steigbügel im Praxistest
Caro von dem Account sunny_kiss hat die SPRENGER System 4 Steigbügel getestet und ihre Erfahrung auf eine sehr besondere Weise beschrieben: "Ein ganz normaler Reitplatz an einem Tag wie jeder ander...
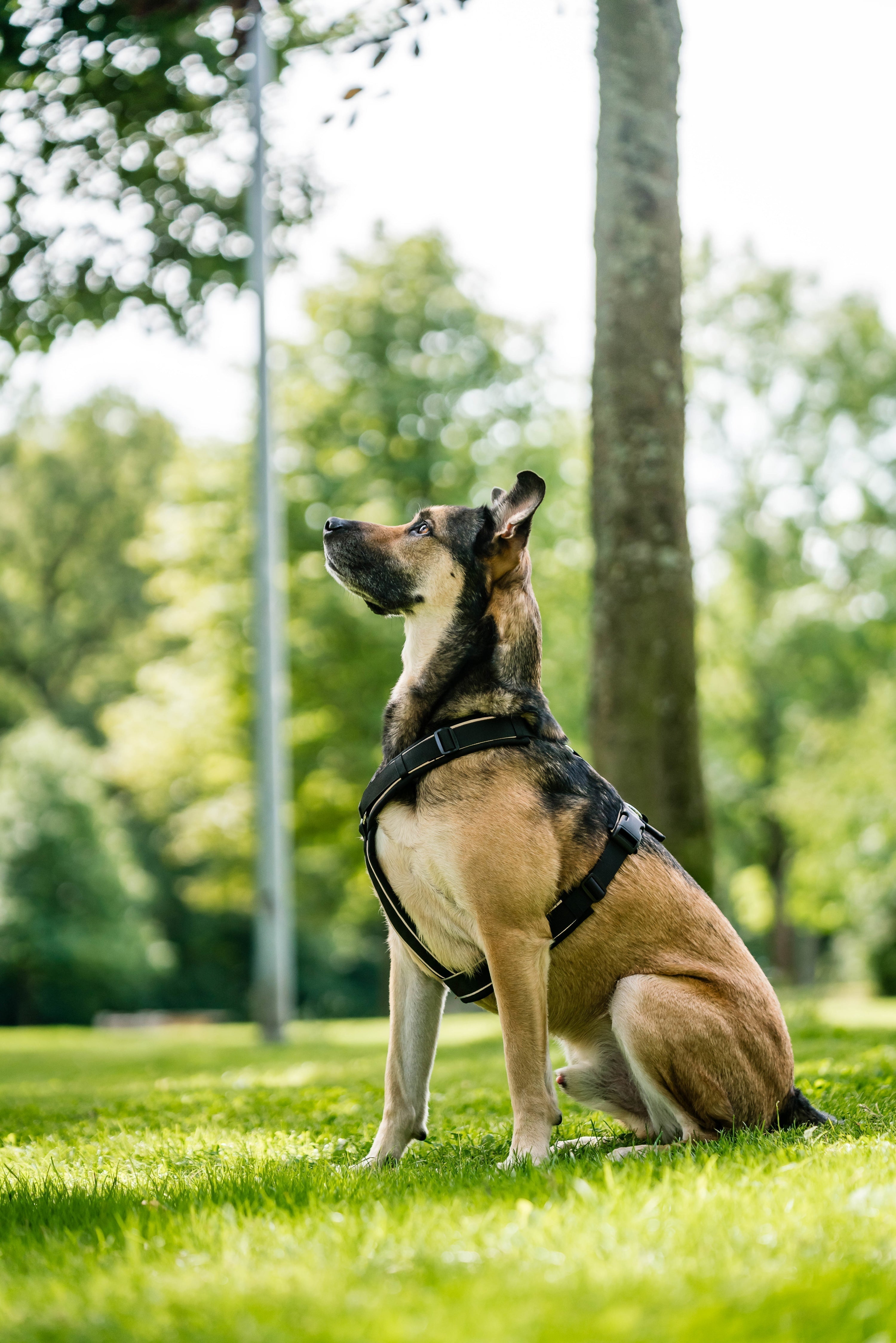
Measuring for a dog harness can sometimes be a real challenge. We have summarized what you need to know about dog harness fit and dog harness size in this blog post!
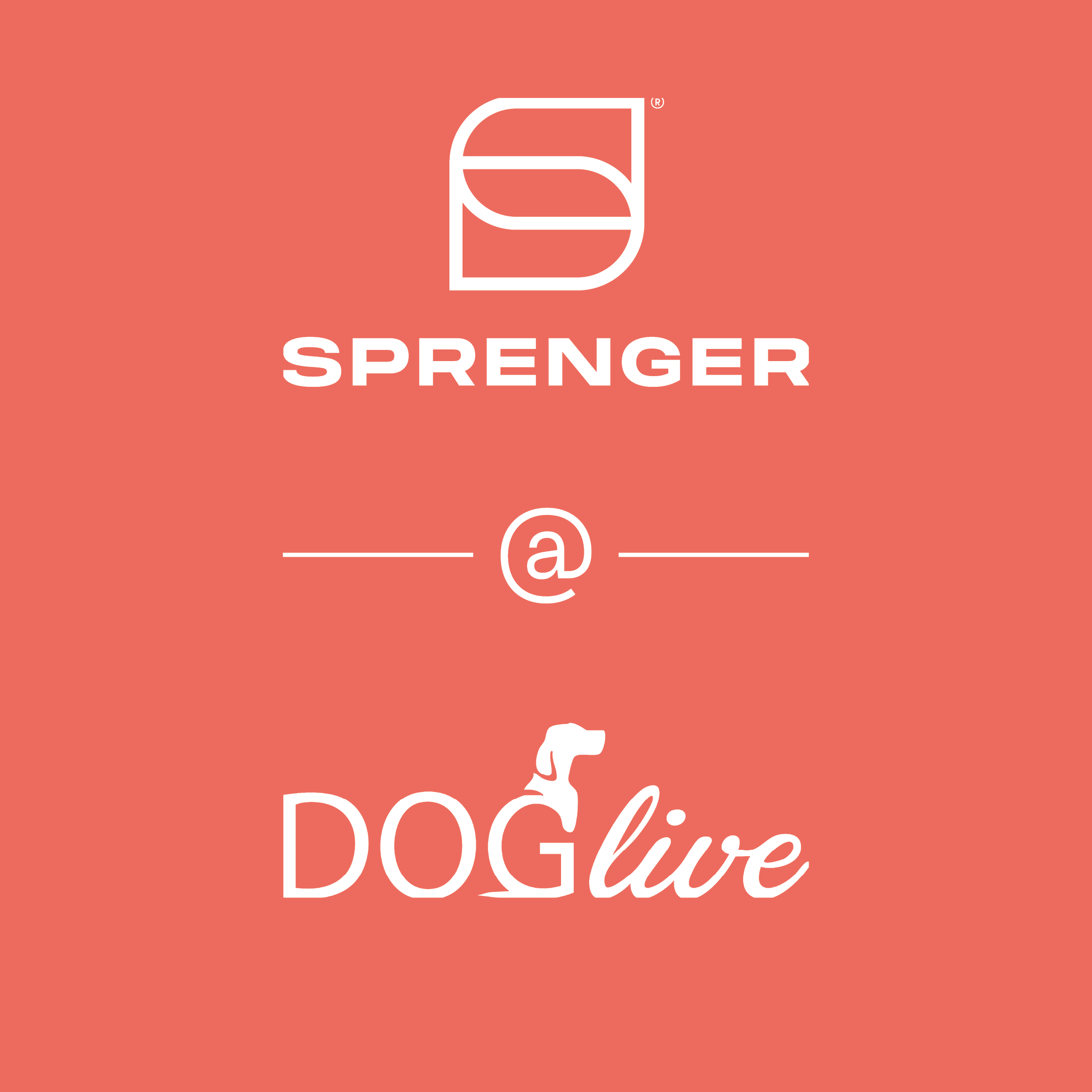
DOGlive Münster – Messe & Event
Die DOGlive ist die Hundemesse in Münster und für alle Hundebesitzer genau das Richtige. Teil des unglaublich breiten Angebots auf der Messe ist diese Jahr auch SPRENGER. Erfahre hier mehr!
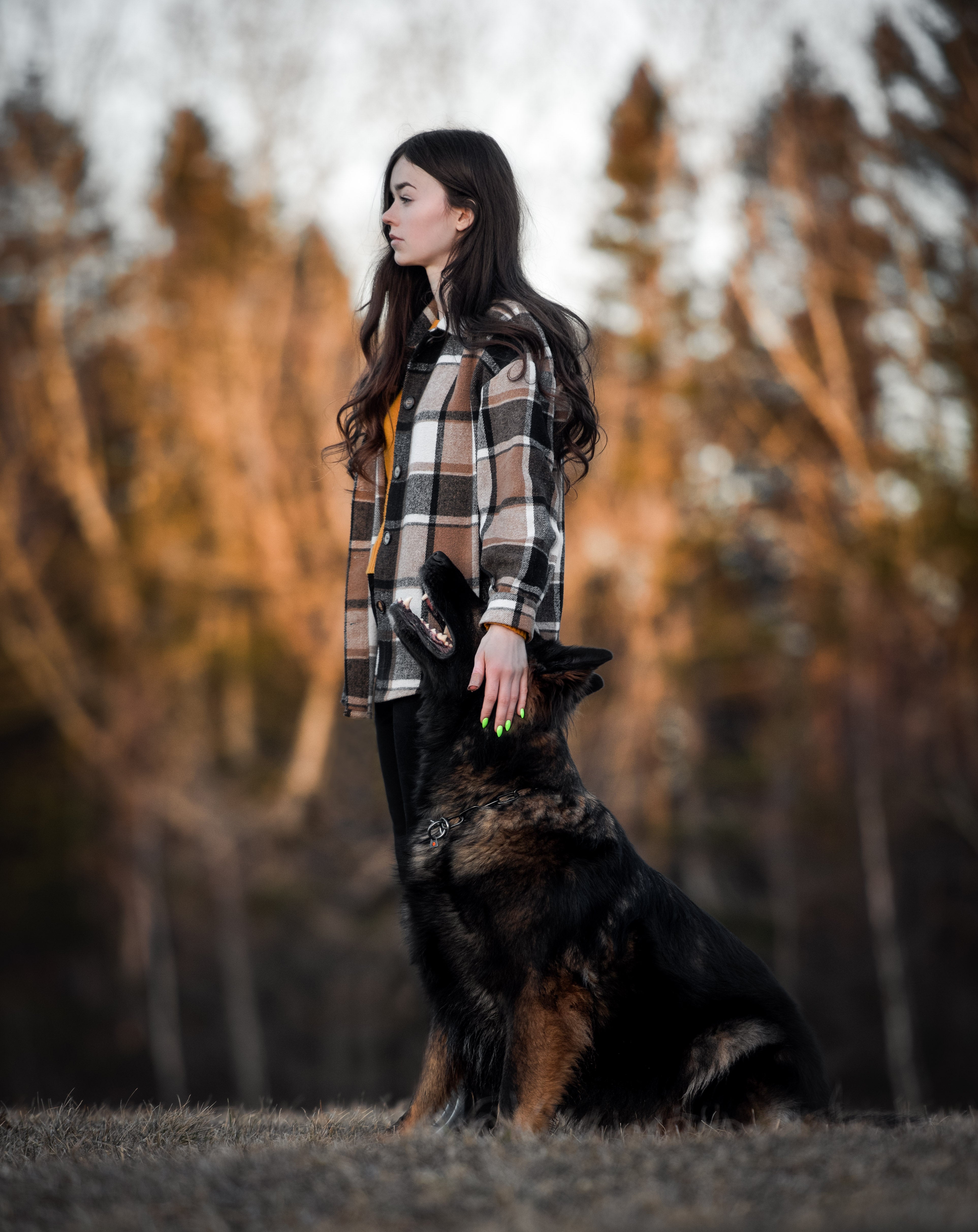
Looking for the right dog sport for you and your dog? Discover the most popular dog sports here!
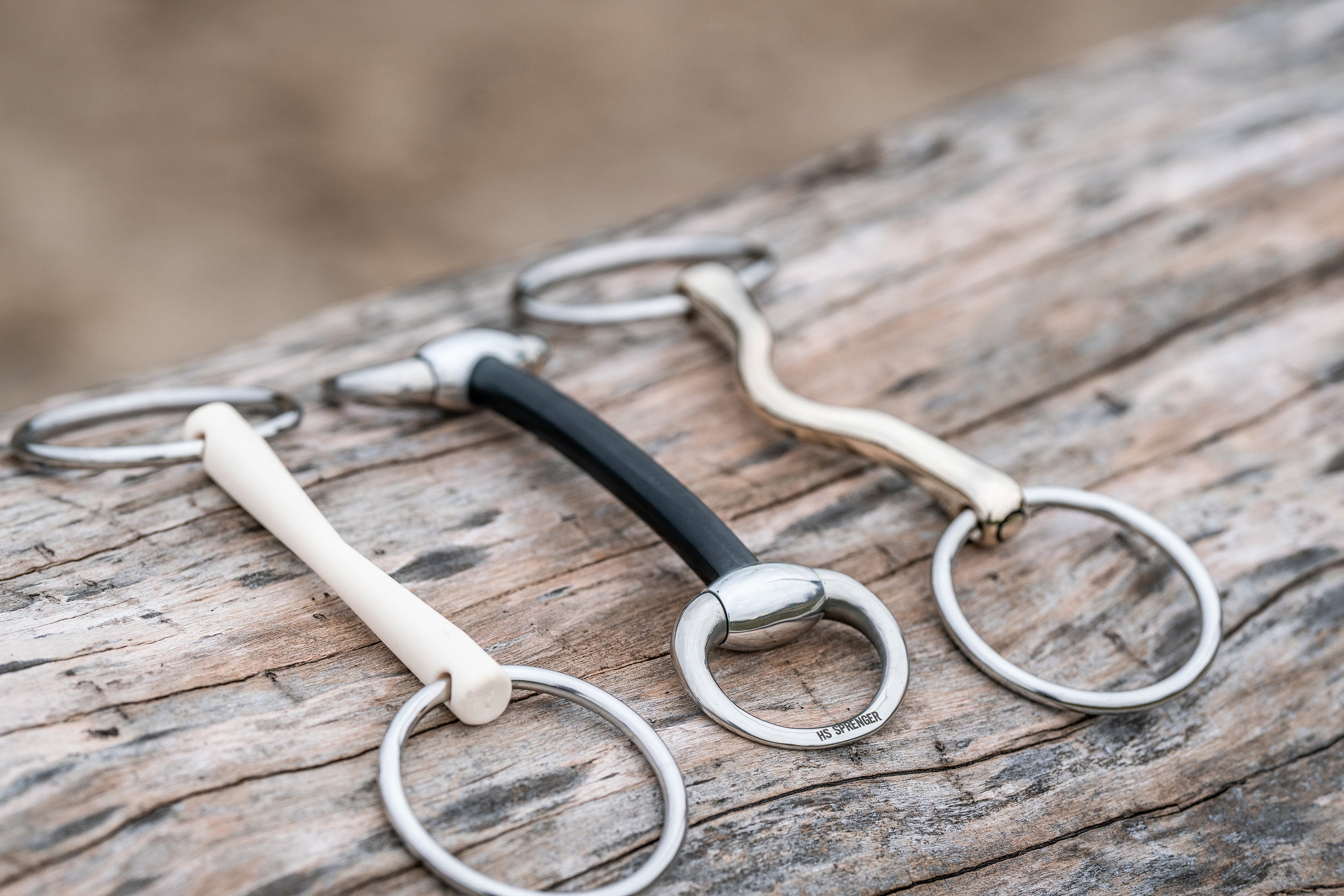
Find out all about mullen mouth bits! What advantages and disadvantages do they offer and for which horses are they a good option? We shed some light on the subject!
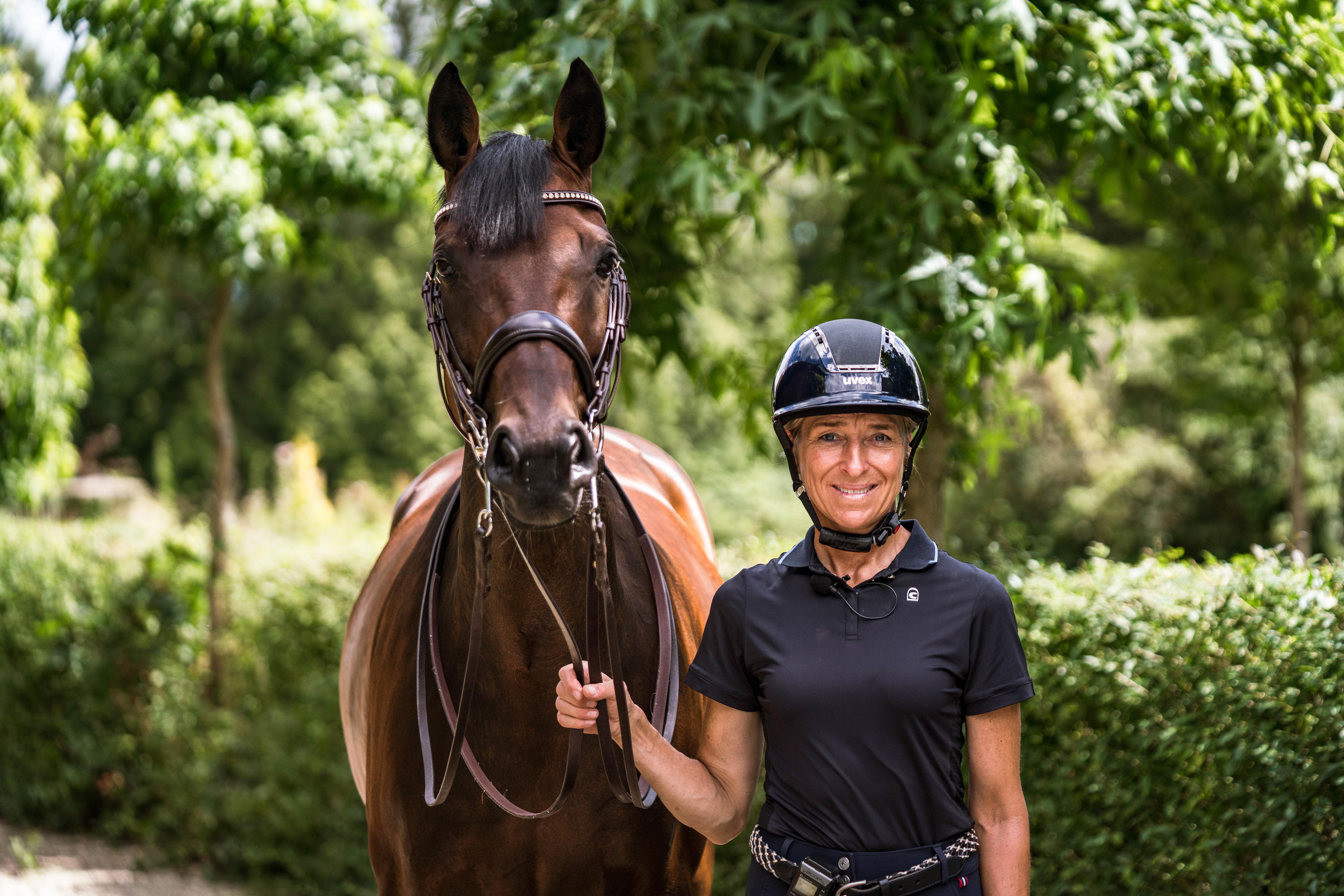
SPRENGER x Ingrid Klimke Collection
Together with our longtime partner Ingrid Klimke, we have designed a unique collection with our and your favorite products! Find out all about the collection here.
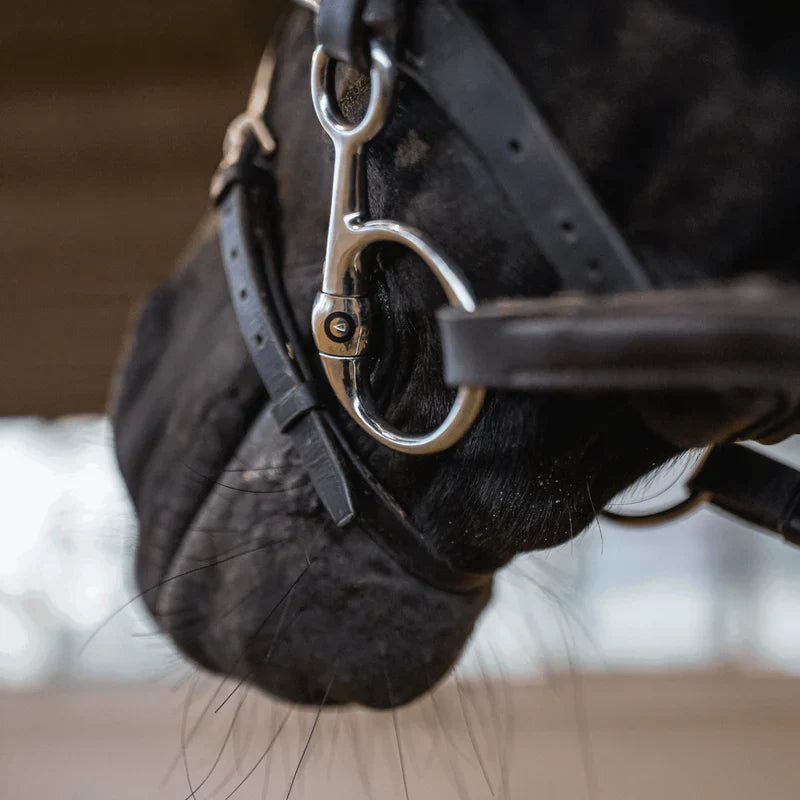
In this blog, we will introduce you to the advantages of our Baucher bits - the popular bit is known to have a special effect in the horse's mouth thanks to its special side parts and buckle, and t...
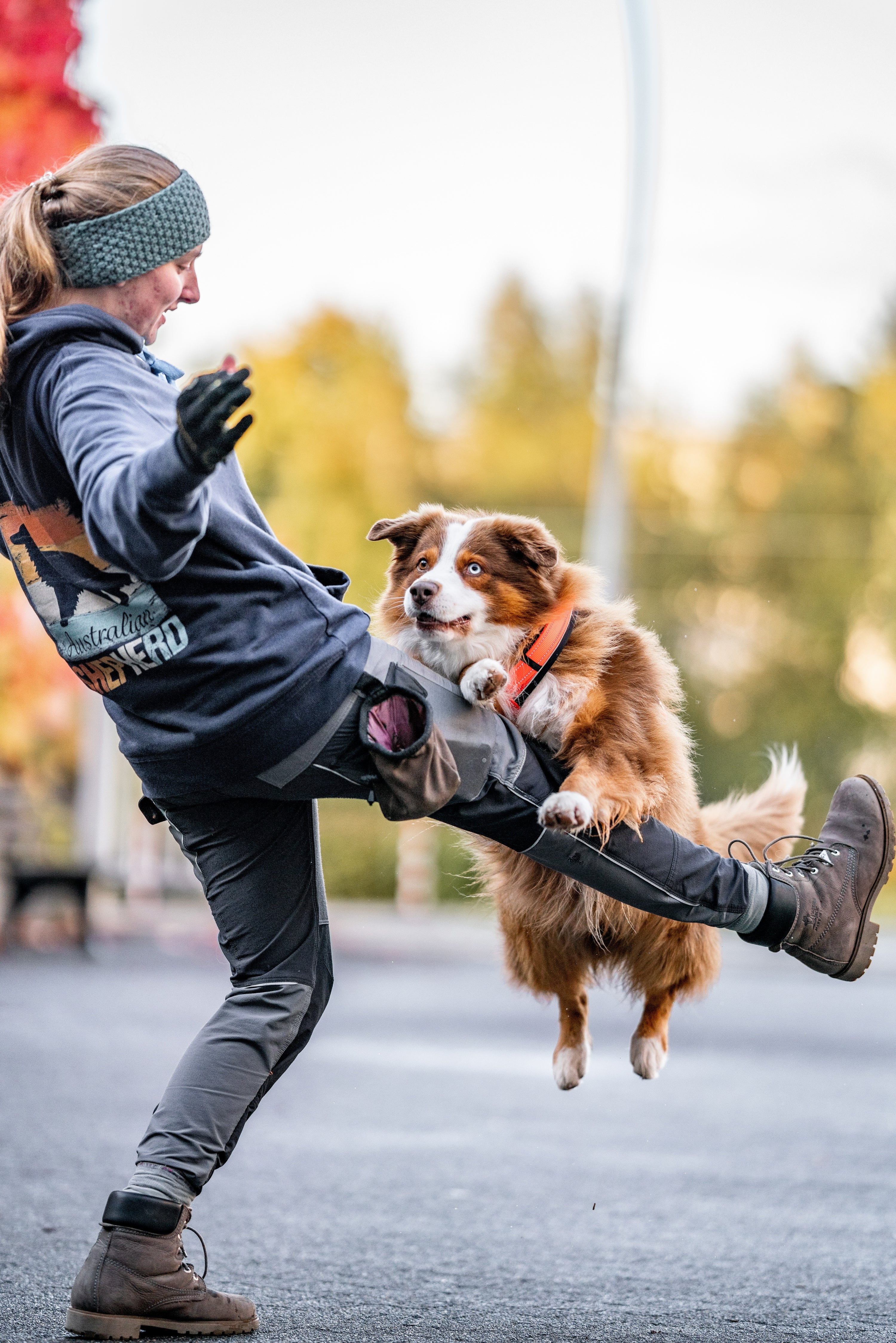
Looking for inspiration for new dog tricks? Whether you're a beginner or advanced, there's something for everyone in our blog post!
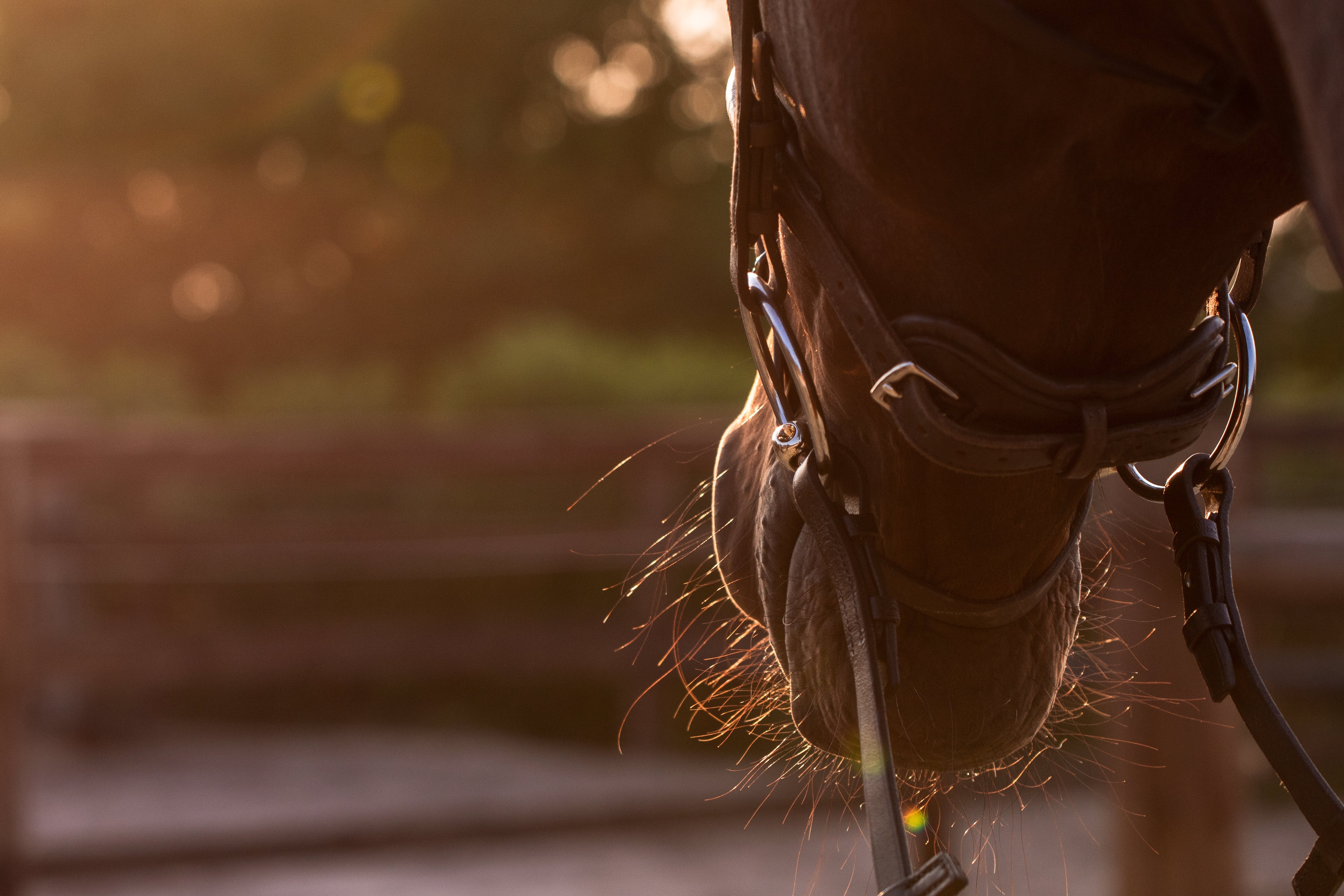
Does your horse tend to be mouthy? Put an end to it! We offer you the best tips and recommendations so that you and your horse can master this challenge together. With SPRENGER, you two are perfect...
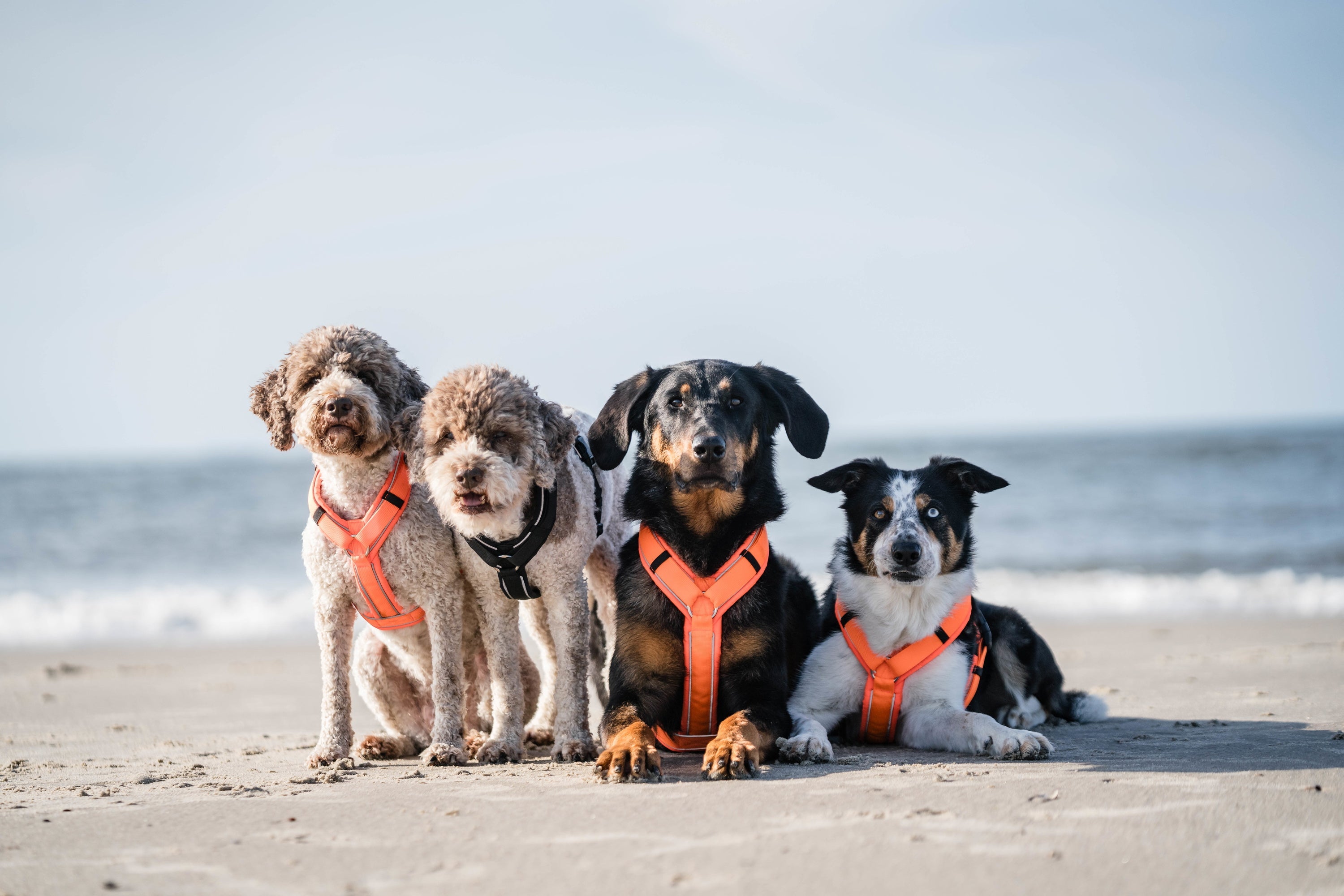
So many dog owners wonder: dog harness or dog collar?Find out everything you need to know about dog harnesses in our guide!
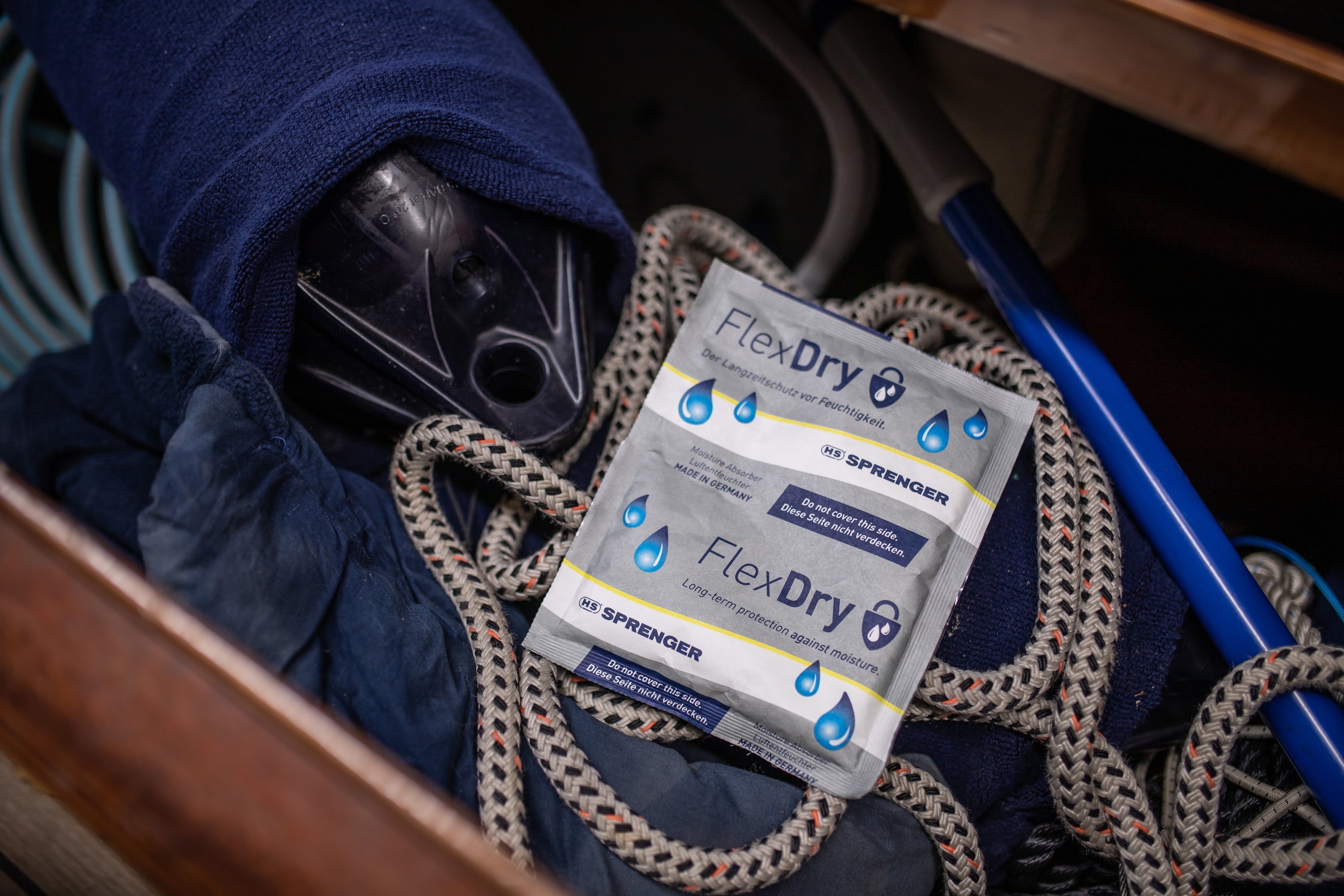
Put an end to steamed-up car windows, mouldy leather equipment in the stable or musty smells on your yacht - the FlexDry dehumidifier from SPRENGER was designed to efficiently remove excess humidity.
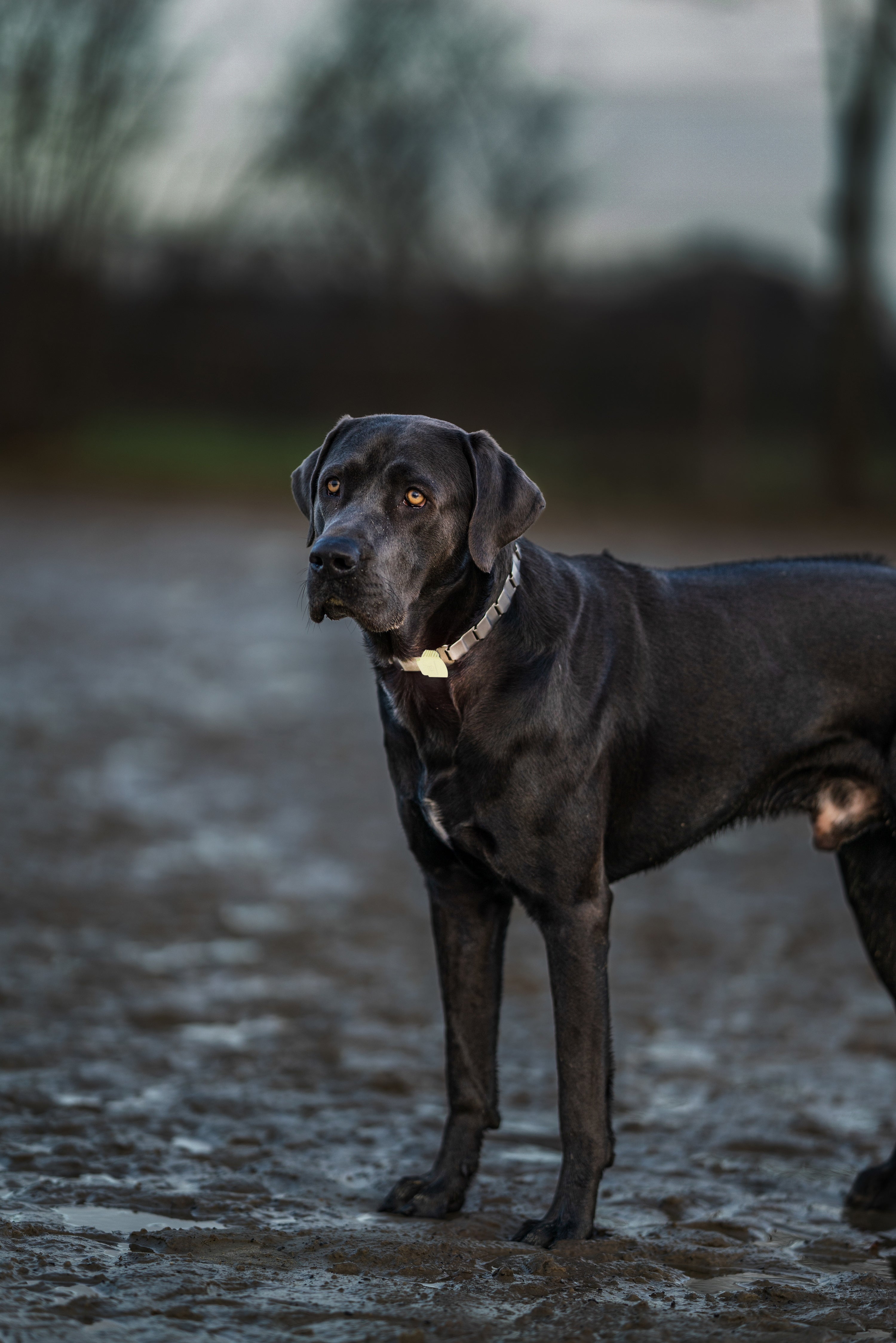
Our tips: stay safe walking your dog in the dark
The dark season has begun: The perfect time to share tips on safety for dogs in the dark and the best ways to make your dog visible in the dark!
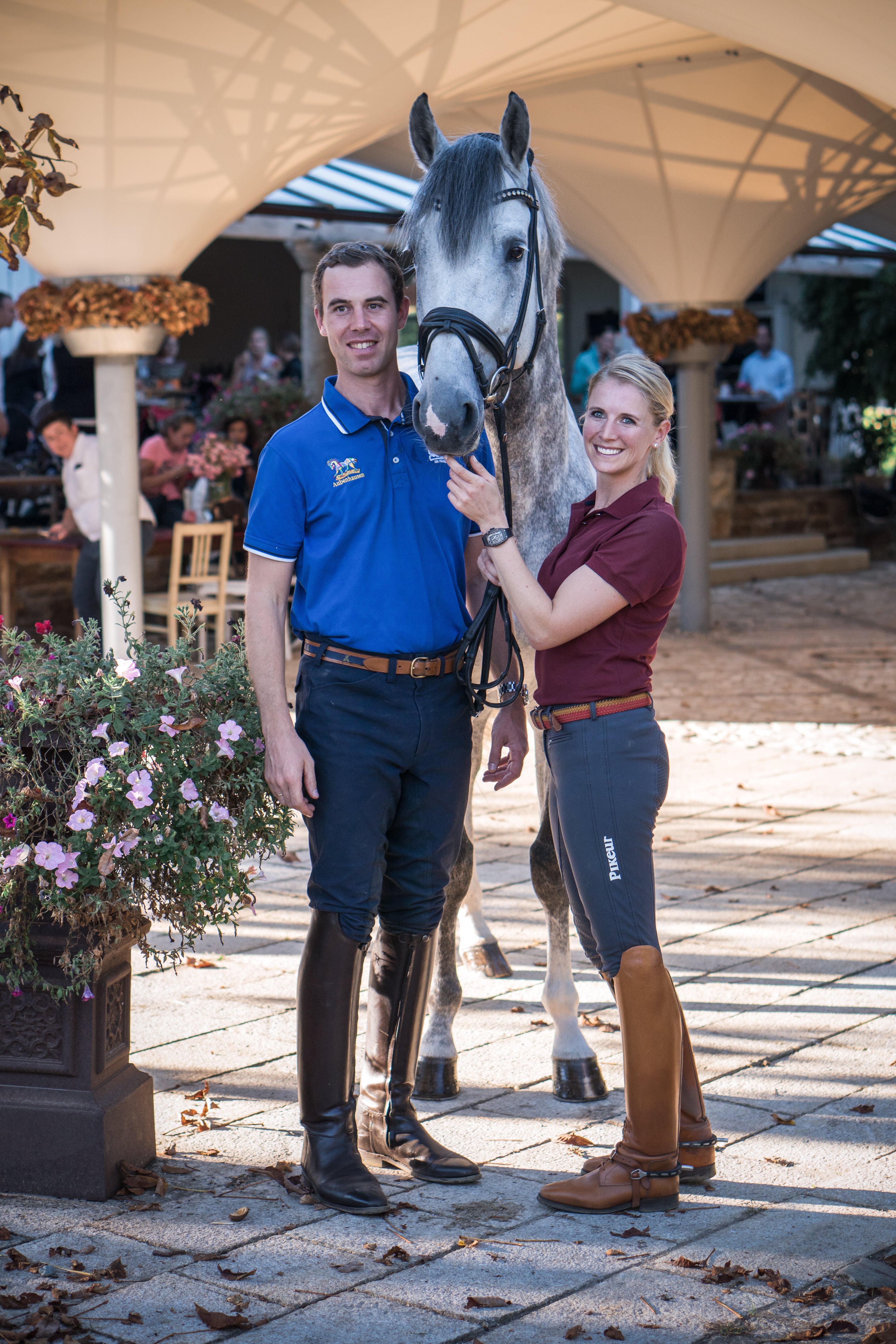
In this blog, we present our new PRONAMIC bits - a bit developed by bit expert Heiko Schmidt-Sentek and the highly successful equestrian siblings Jessica von Bredow-Wendl and Benjamin Werndl. The P...
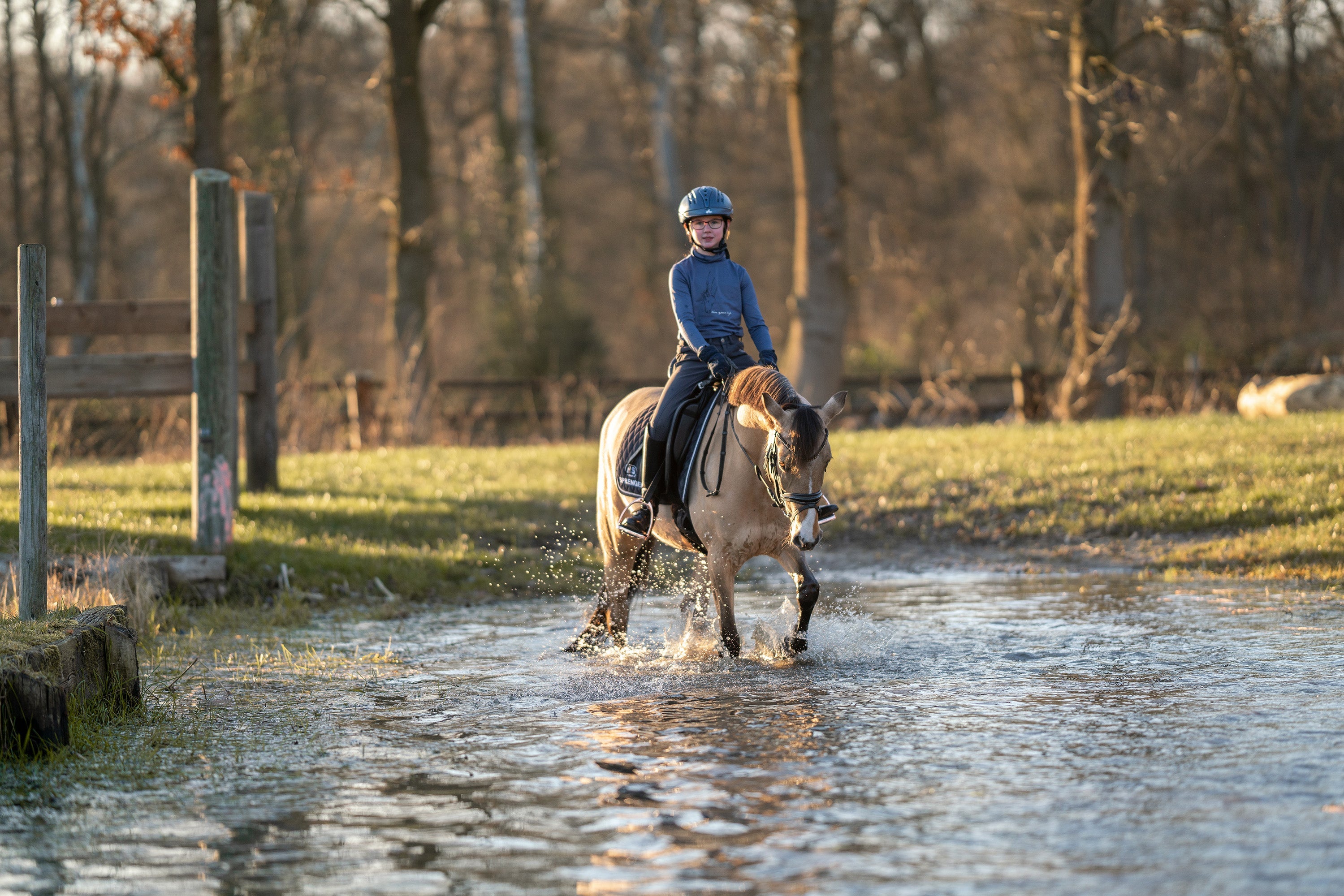
Especially for small shoe sizes: our spurs and stirrups in children's sizes. Why are there children's stirrups and what are the advantages? You can find out this and much more in the article.
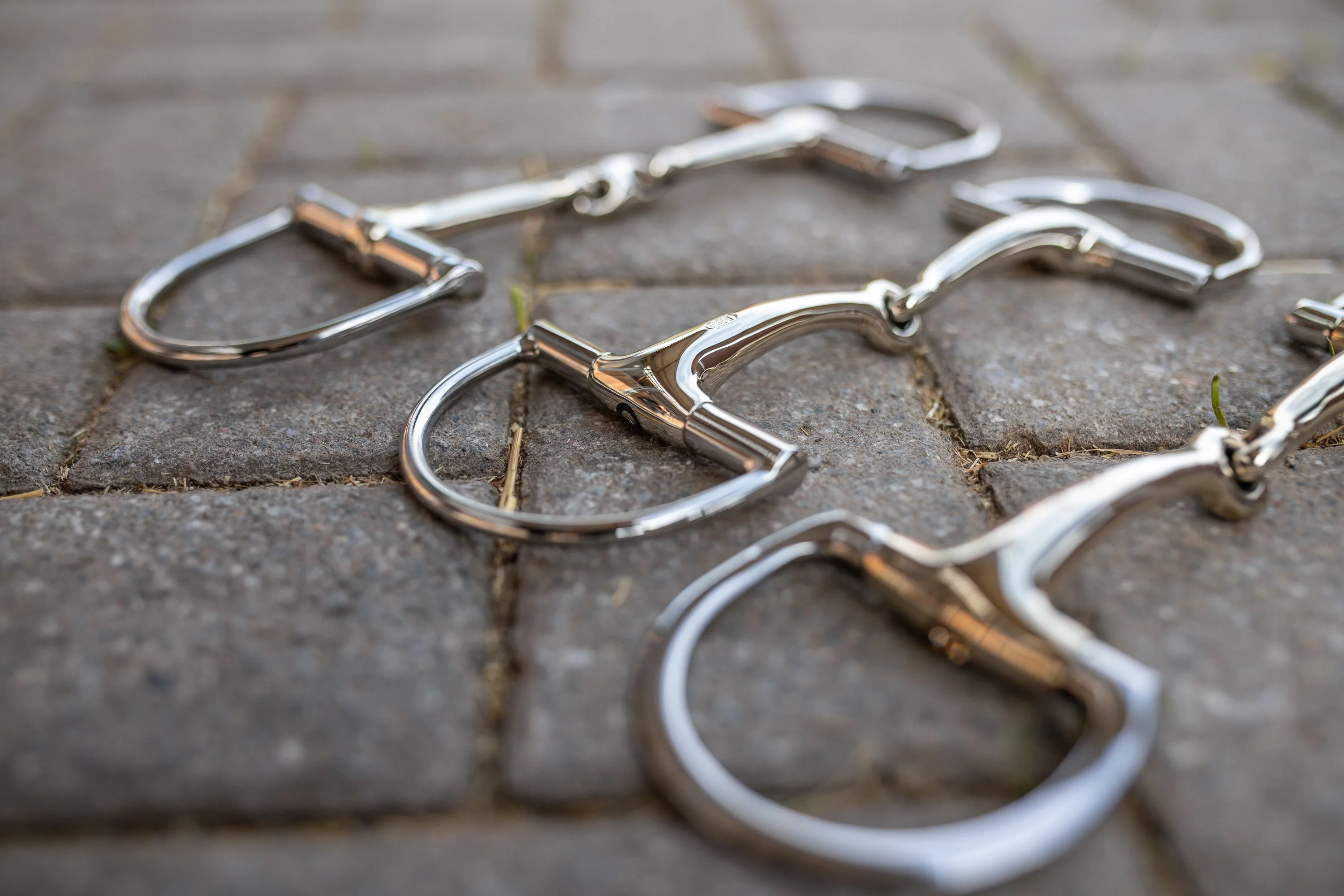
Which Cheekpiece should I Choose?
How exactly does a loose ring snaffle work? What is the difference between eggbut, D-ring and full cheek snaffles? When should I use a 3-ring bit and when should I opt for a Pelham?
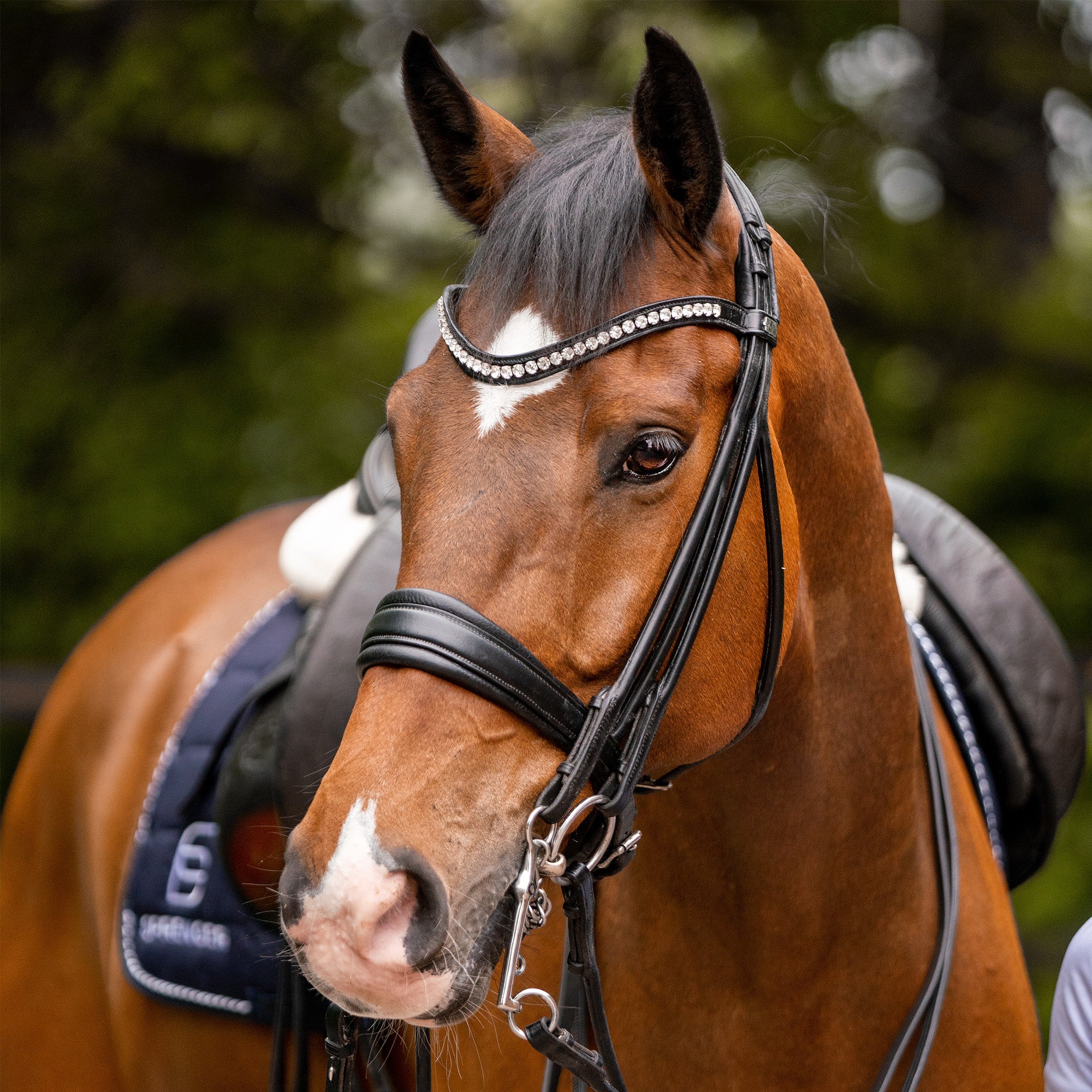
Correctly Fitting the Double Bridle
How is a weymouth bit correctly buckled and what do I have to pay attention to when choosing the two bits? Our tips will help you make the switch to a double bridle.
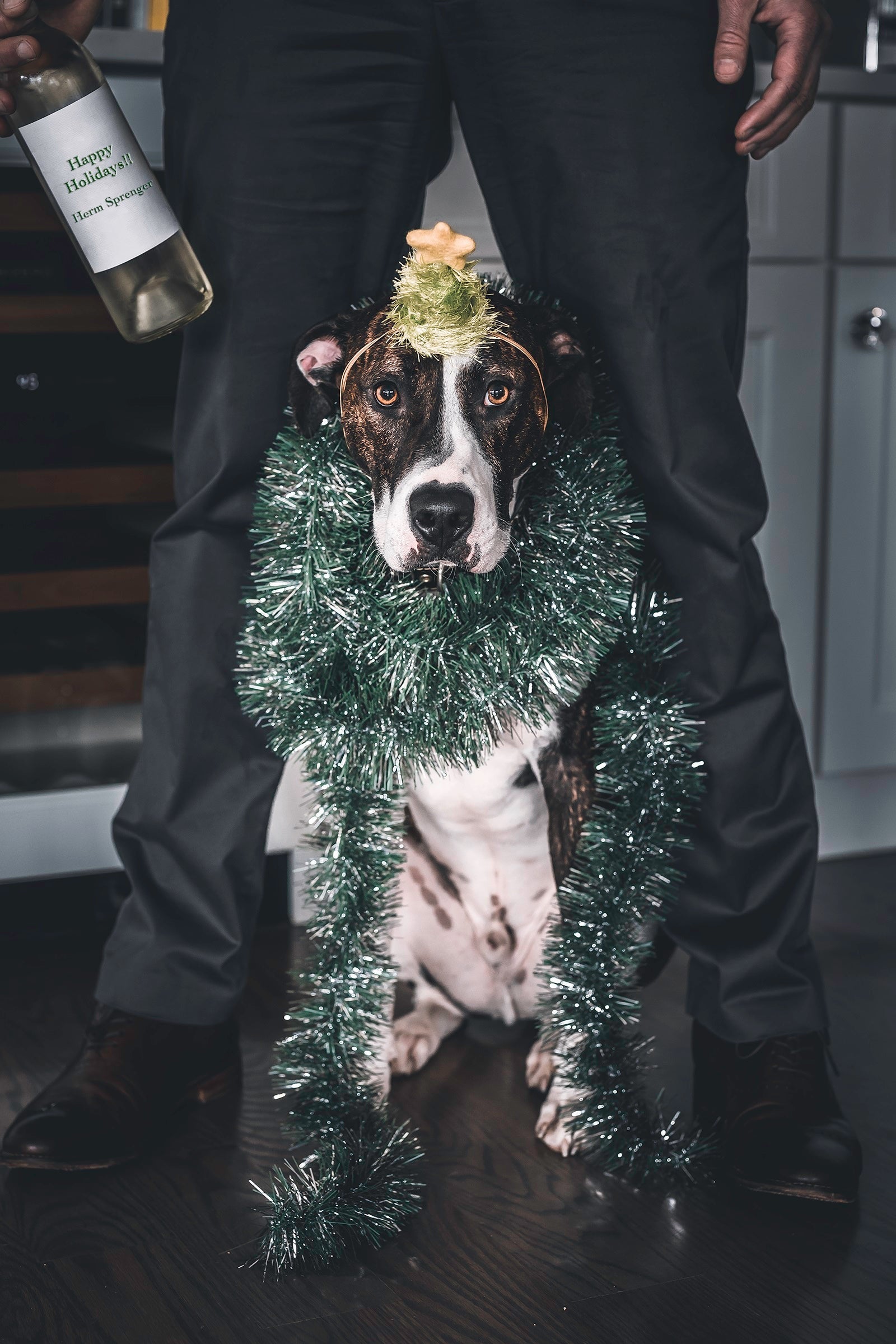
Looking for a gift for the dogs and dog owners in your life? Then check out our SPRENGER gift guide!
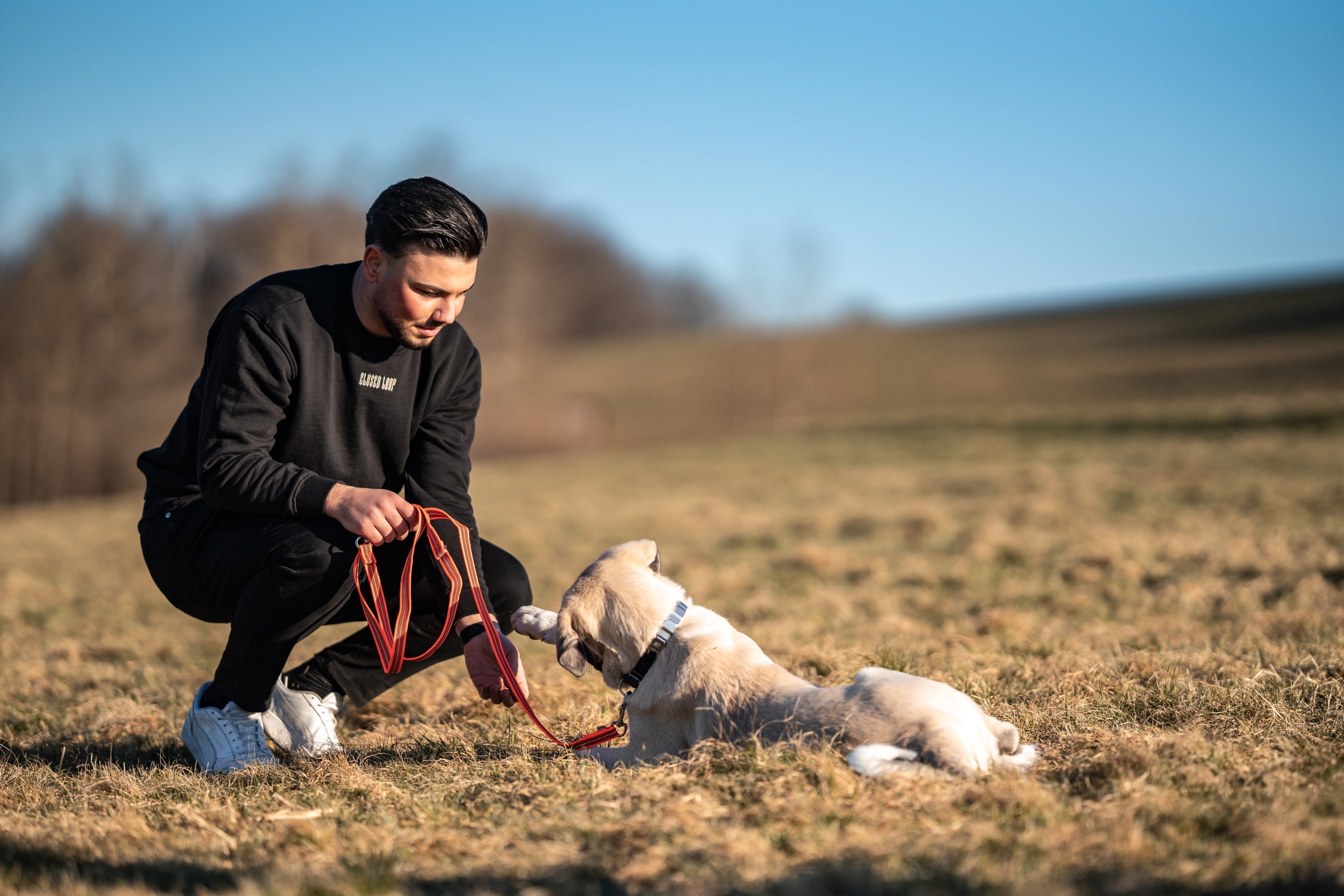
You’re getting a dog! What is essential equipment for dogs?
With a new dog moving in the excitement is huge. The right equipment helps you and your dog get off to the right start. Discover everything you need here including a PDF checklist for you to download!
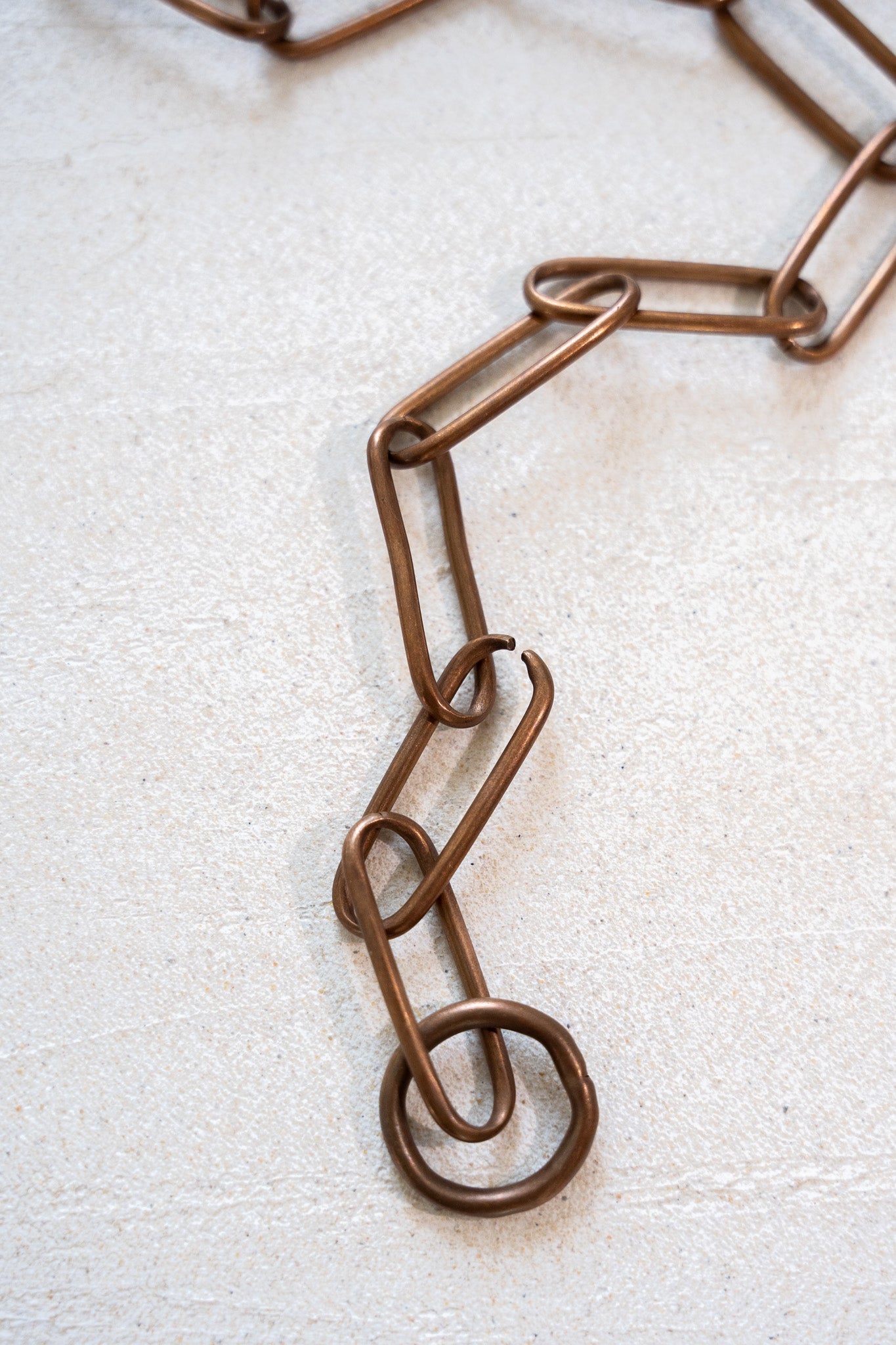
When to replace a chain collar?
There comes a time when your chain collar needs to be replaced. Find out here how to know when it's time to replace your chain collar!
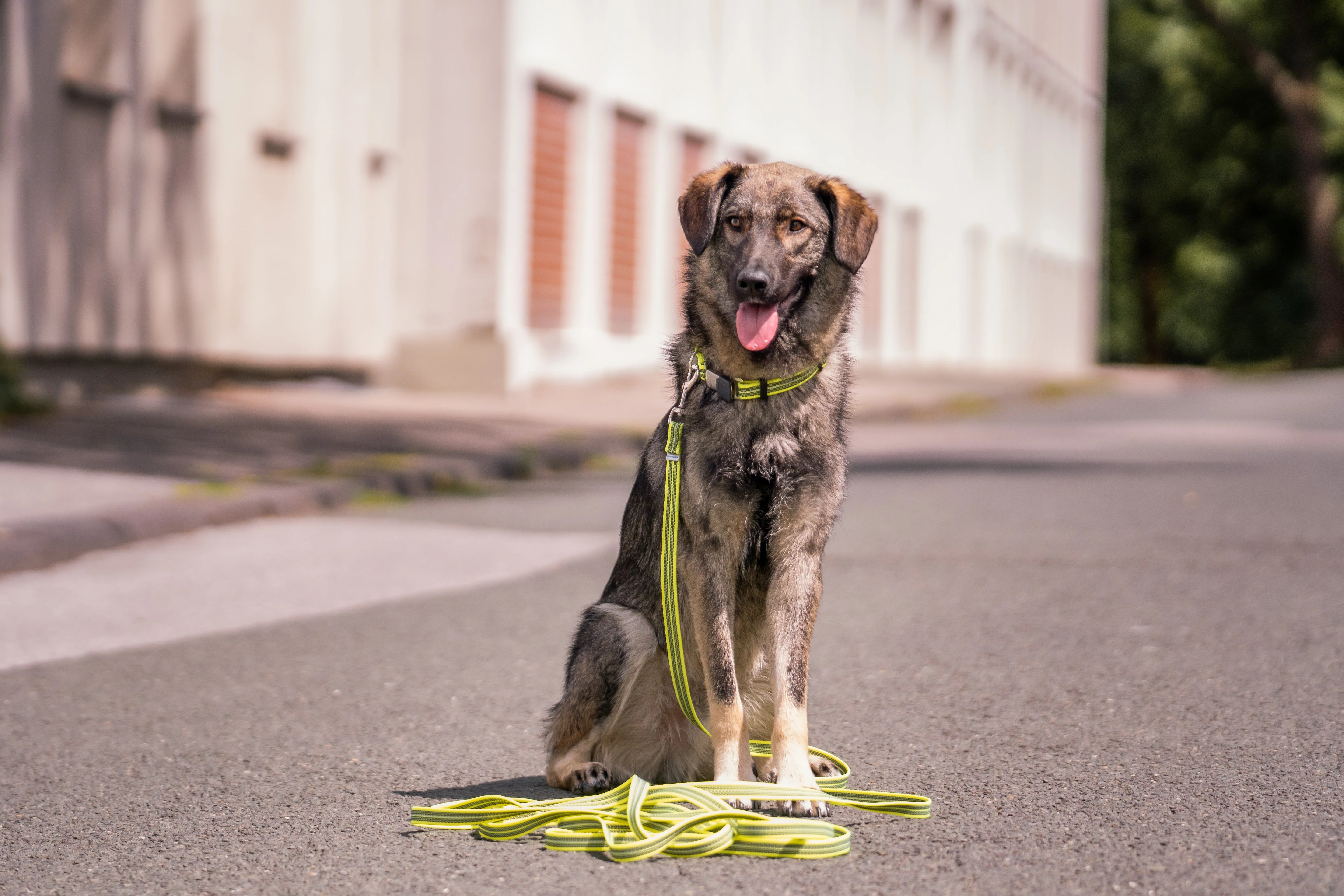
Tracking leashes are equally popular for large and small dogs. There are many different designs and possible applications - find out everything you need to know about tracking leashes here.
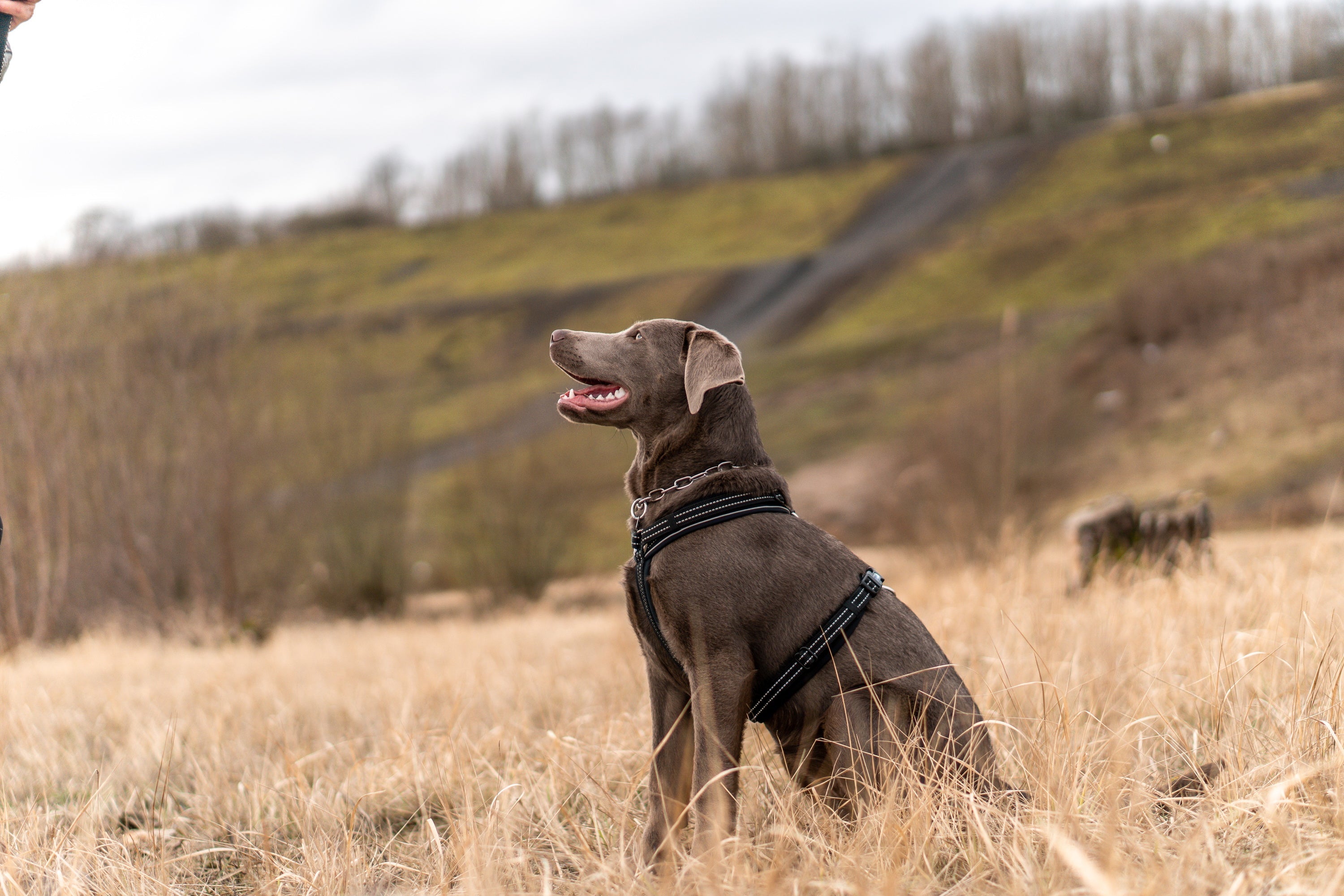
If you want to enjoy your dog equipment for a long time, besides quality proper care is important! Find out what you need to know about maintaining dog chains, collars, harnesses and co:
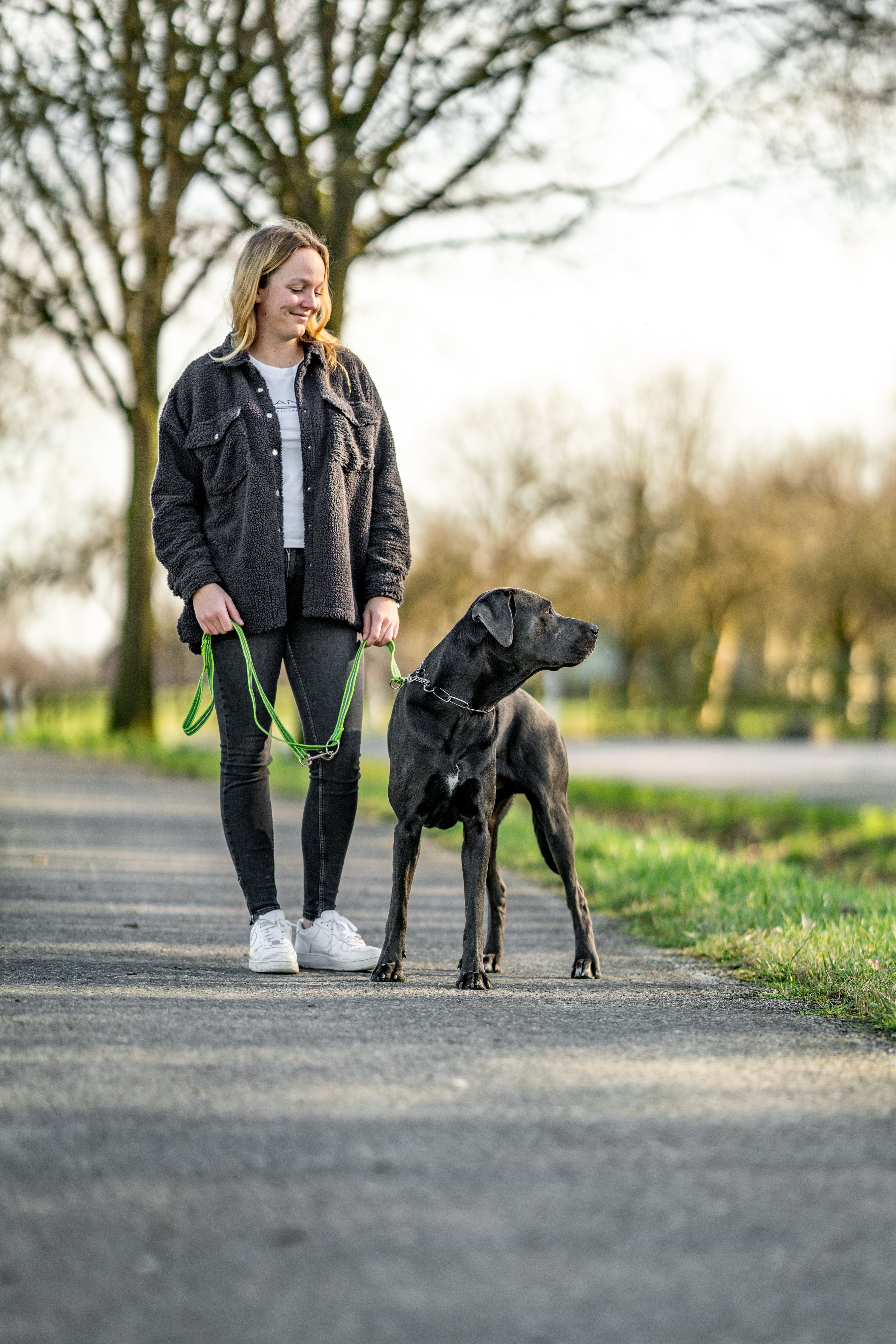
Why use a chain collar for dogs?
Unfortunately, there are still many prejudices surrounding dog chain collars today, and yet they are often done an injustice. Find out here what you need to consider when buying a chain collar for ...
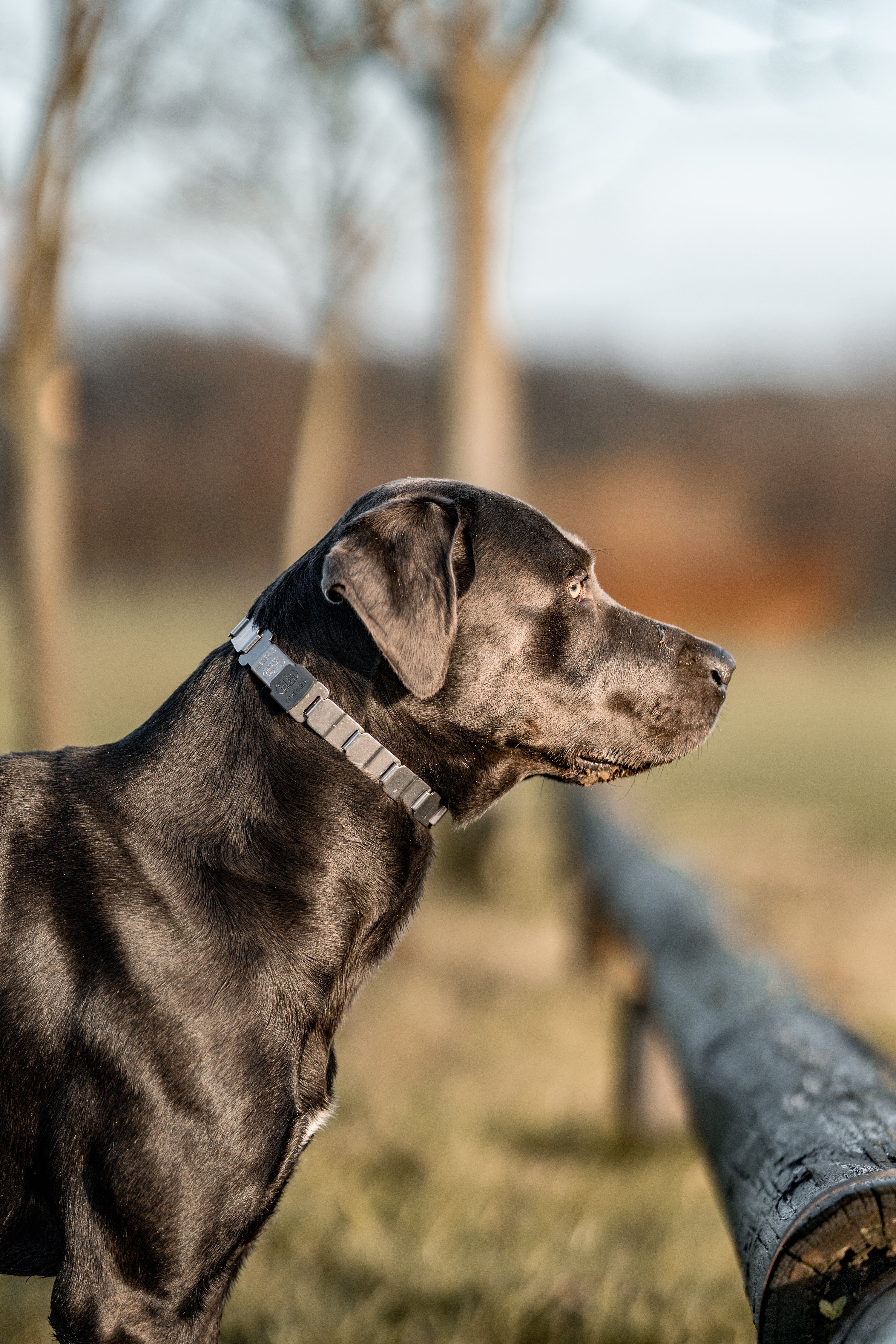
Our NeckTech collar combines the best of both worlds: It has the material advantages of stainless steel chains and the comfort and look of flat dog collars!
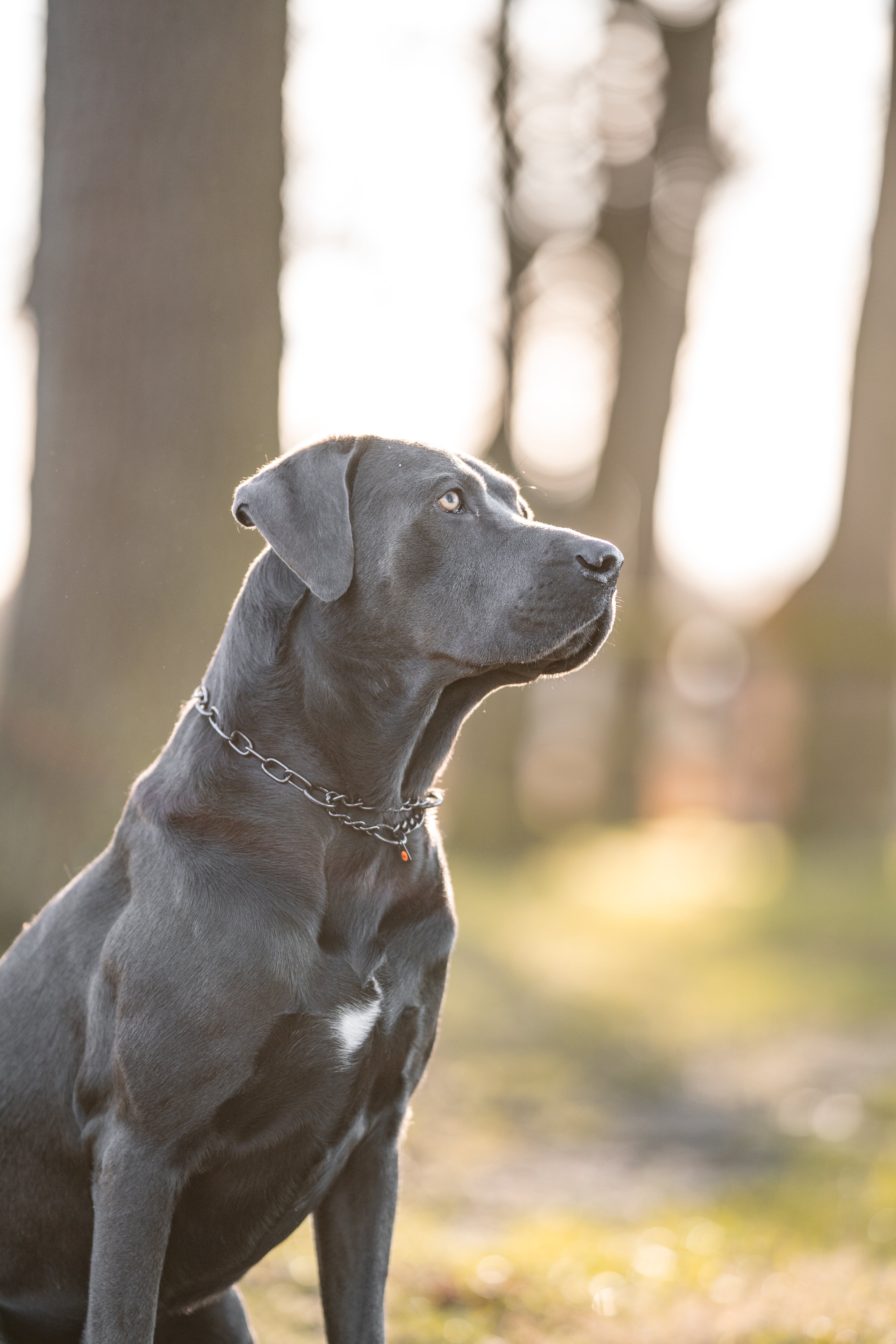
SPRENGER chain collars come in different materials. But it is not just the look that differs. Find out all about the material properties here!
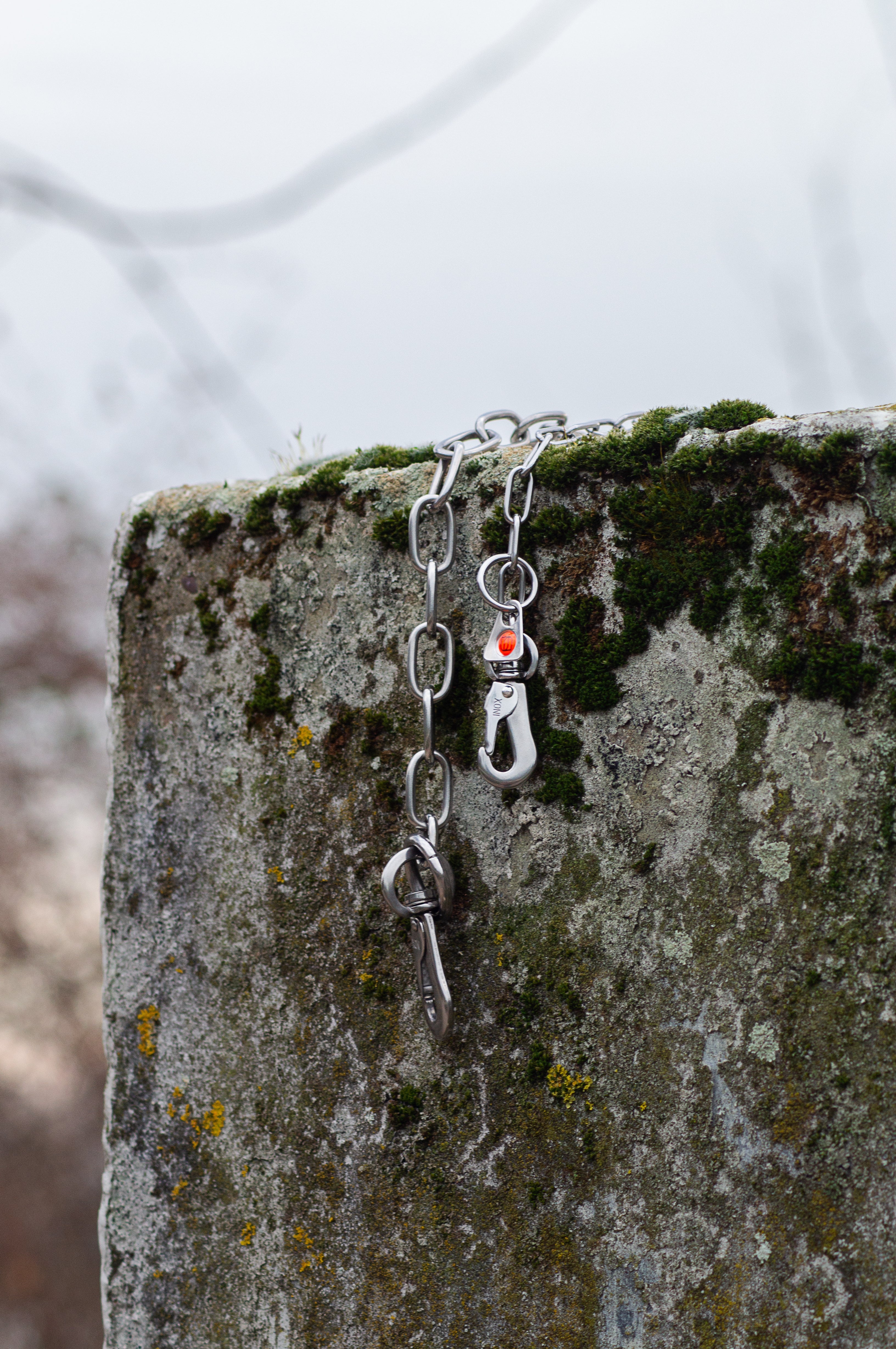
The right wire gauge for your dogs chain collar
The wire gauge of a chain collar is important for the longevity and safety of the chain and the comfort of the dog. Find out here which wire gauge fits you!
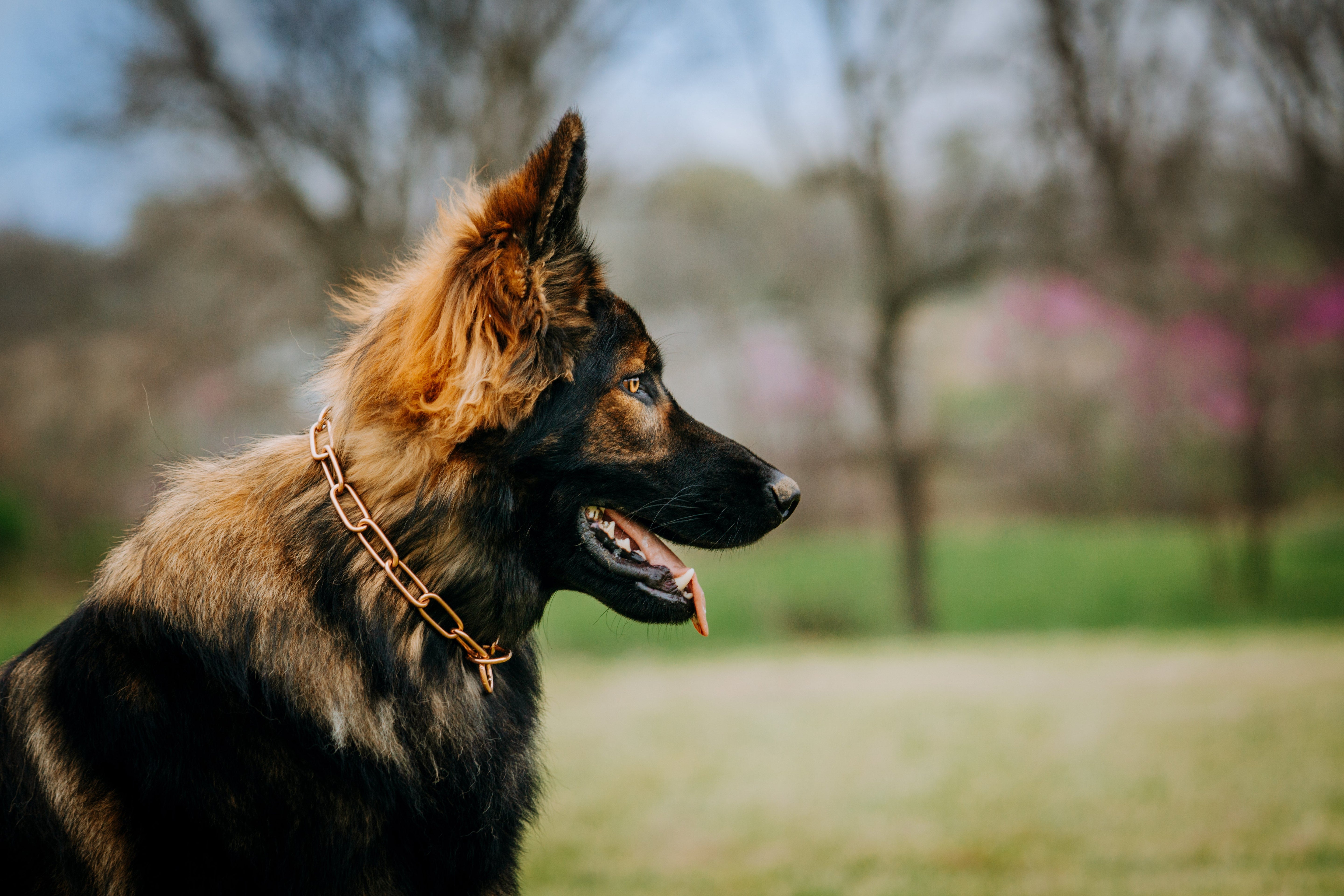
Dogs with long or fine coats are often affected by broken hair, hair loss or other hair thinning. Find out what helps!
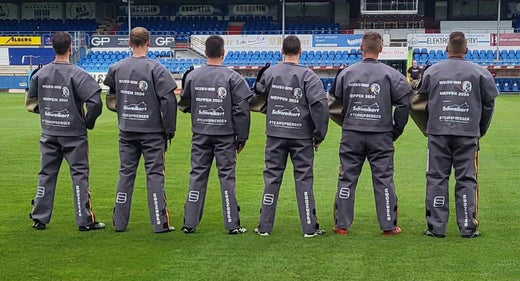
The WUSV World Championship for IP and Agility is taking place here in Germany this year. Find out everything you need to know about the event and the world of dog sport here!
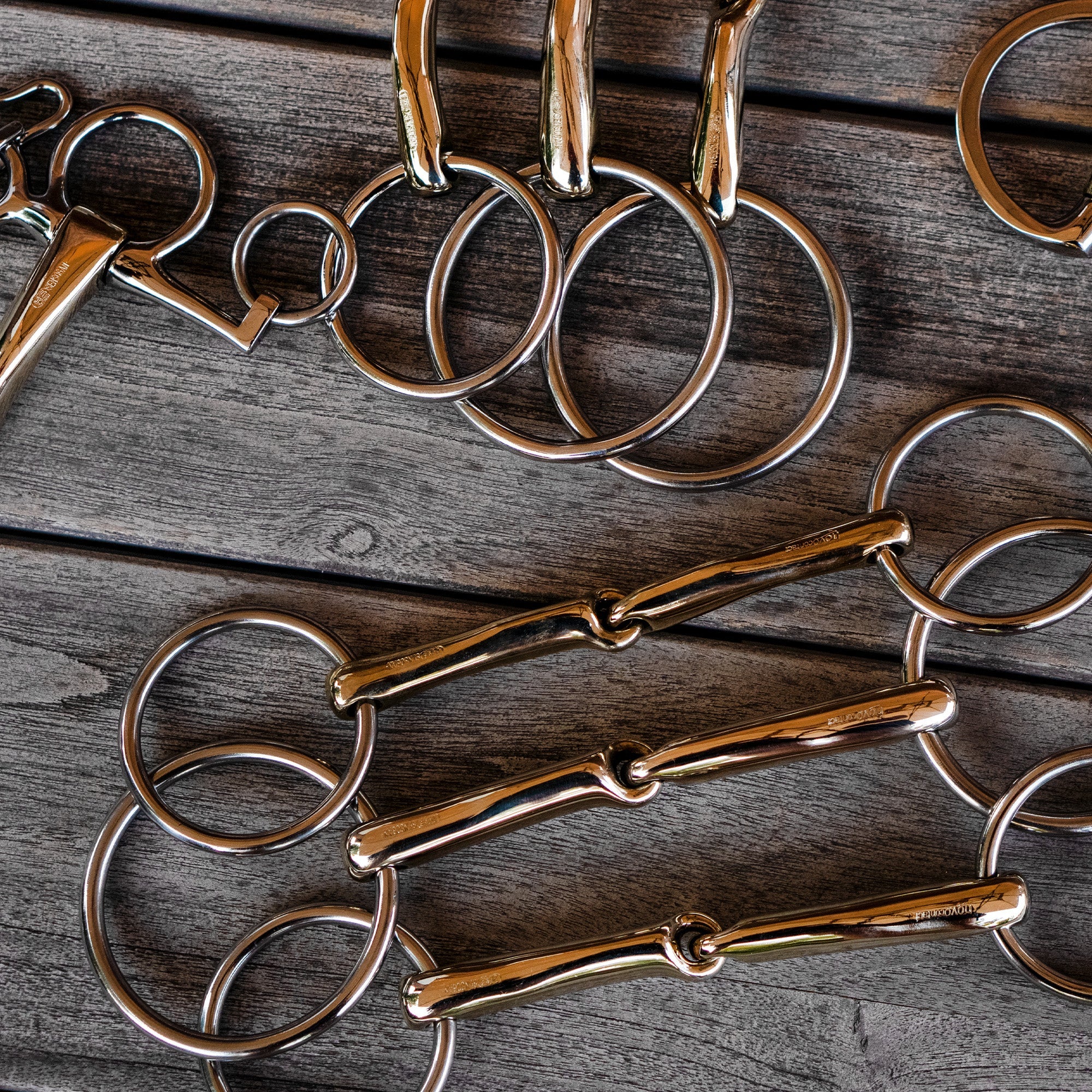
The SPRENGER range also offers anatomically shaped bits for ponies and Icelandic horses, which are specially designed for the conditions in the horse's mouth and connection problems.
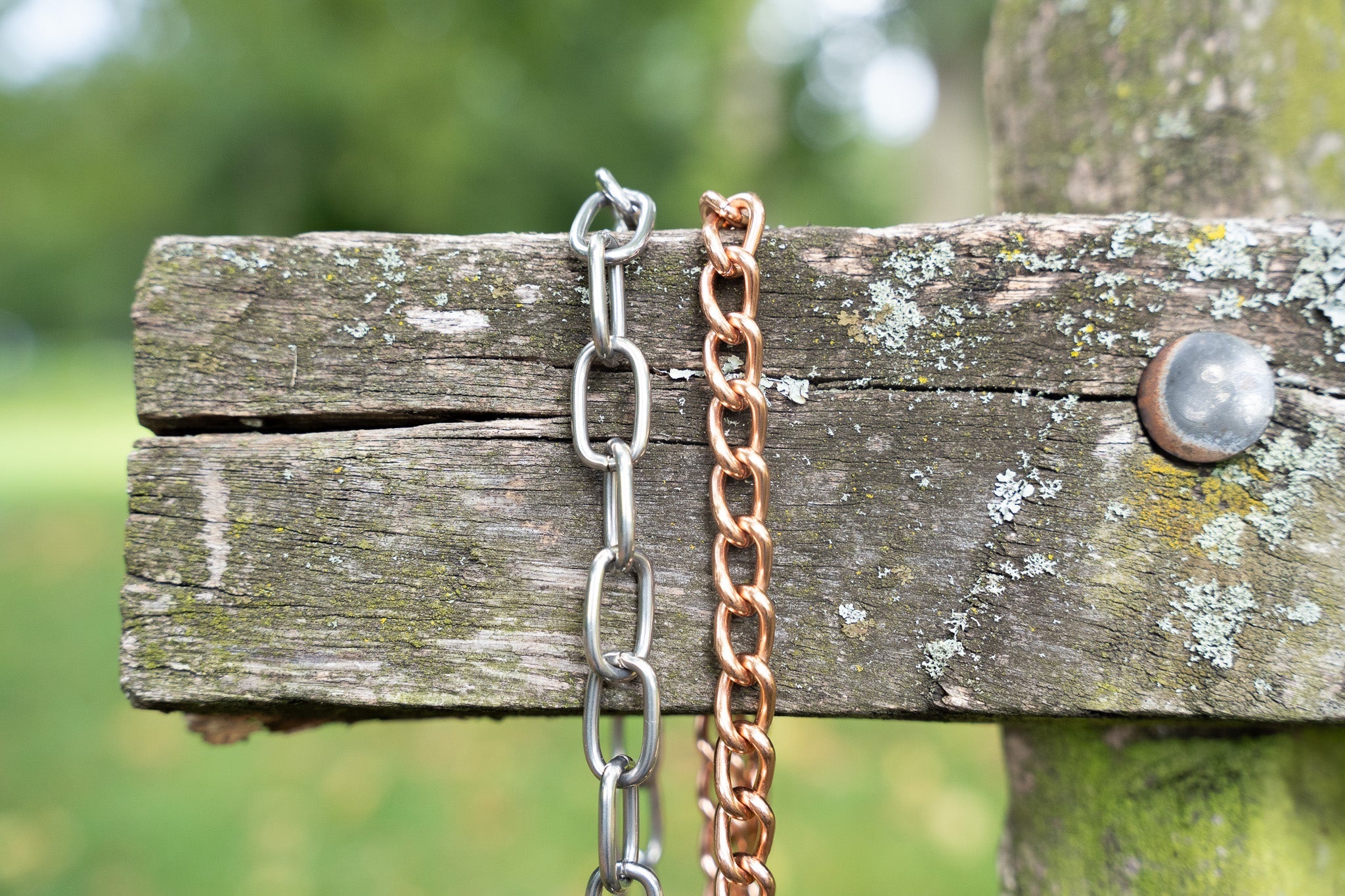
Choosing the right type of link for your dog's chain collar is not just a matter of taste. You can find out which link type you should choose in this blog post!
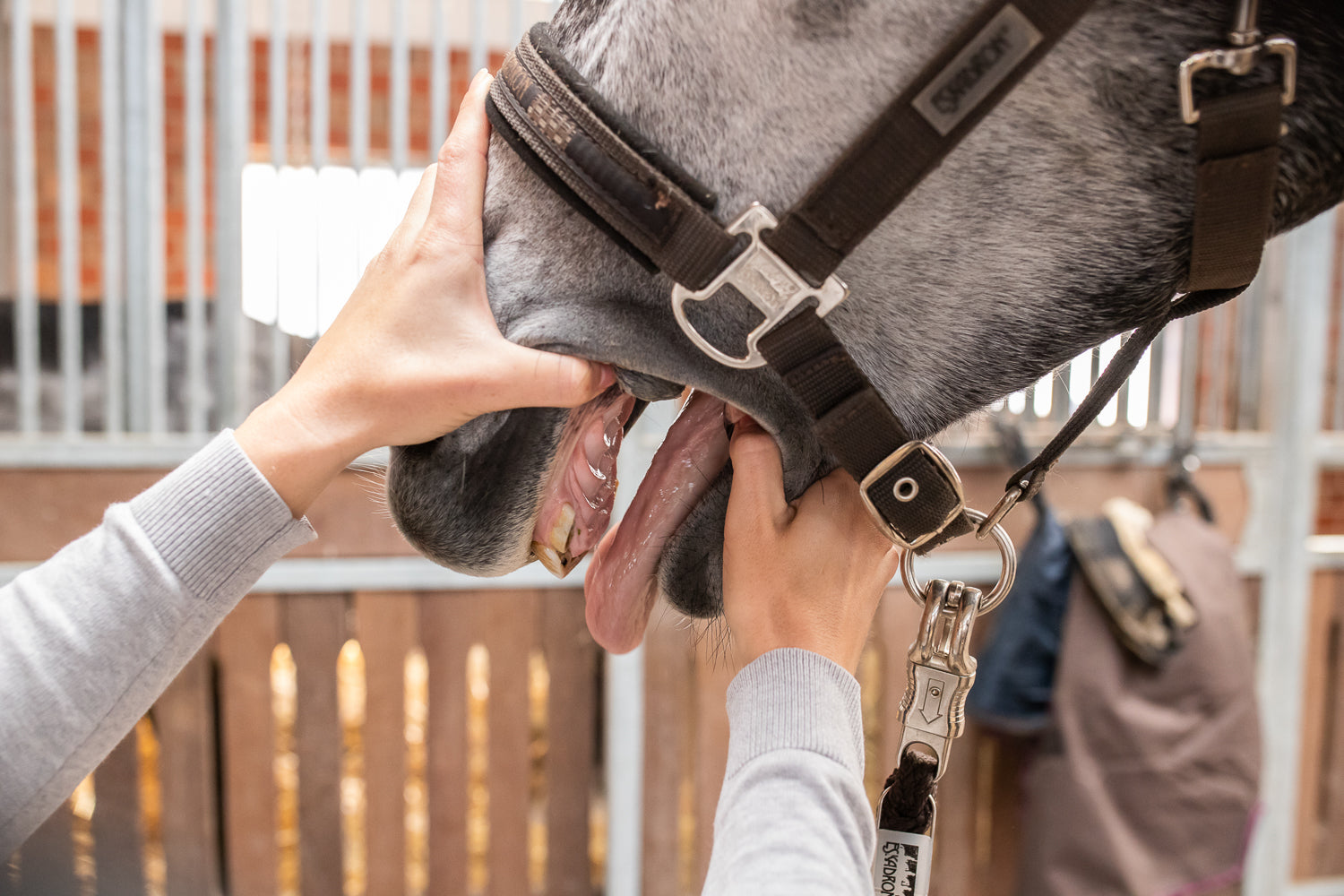
THE RIGHT BIT FOR A MOUTHY HORSE
Does your horse tend to be mouthy? Put an end to it! We offer you the best tips and recommendations so that you and your horse can master this challenge together. With SPRENGER, you two are perfect...
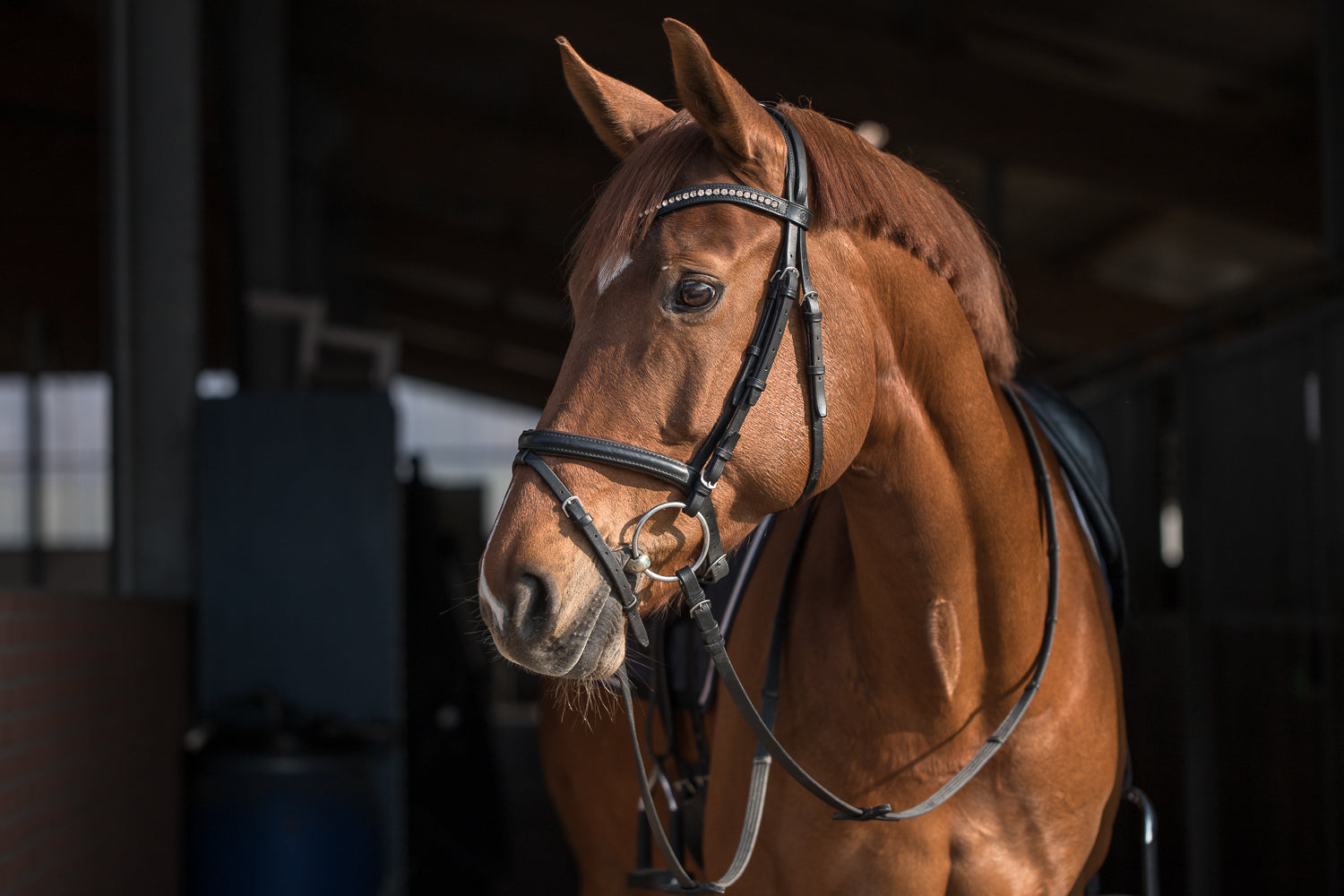
THE RIGHT BIT FOR A HORSE THAT CHEWS TOO MUCH
Does your horse tend to be mouthy? Put an end to it! We offer you the best tips and recommendations so that you and your horse can master this challenge together. With SPRENGER, you two are perfect...
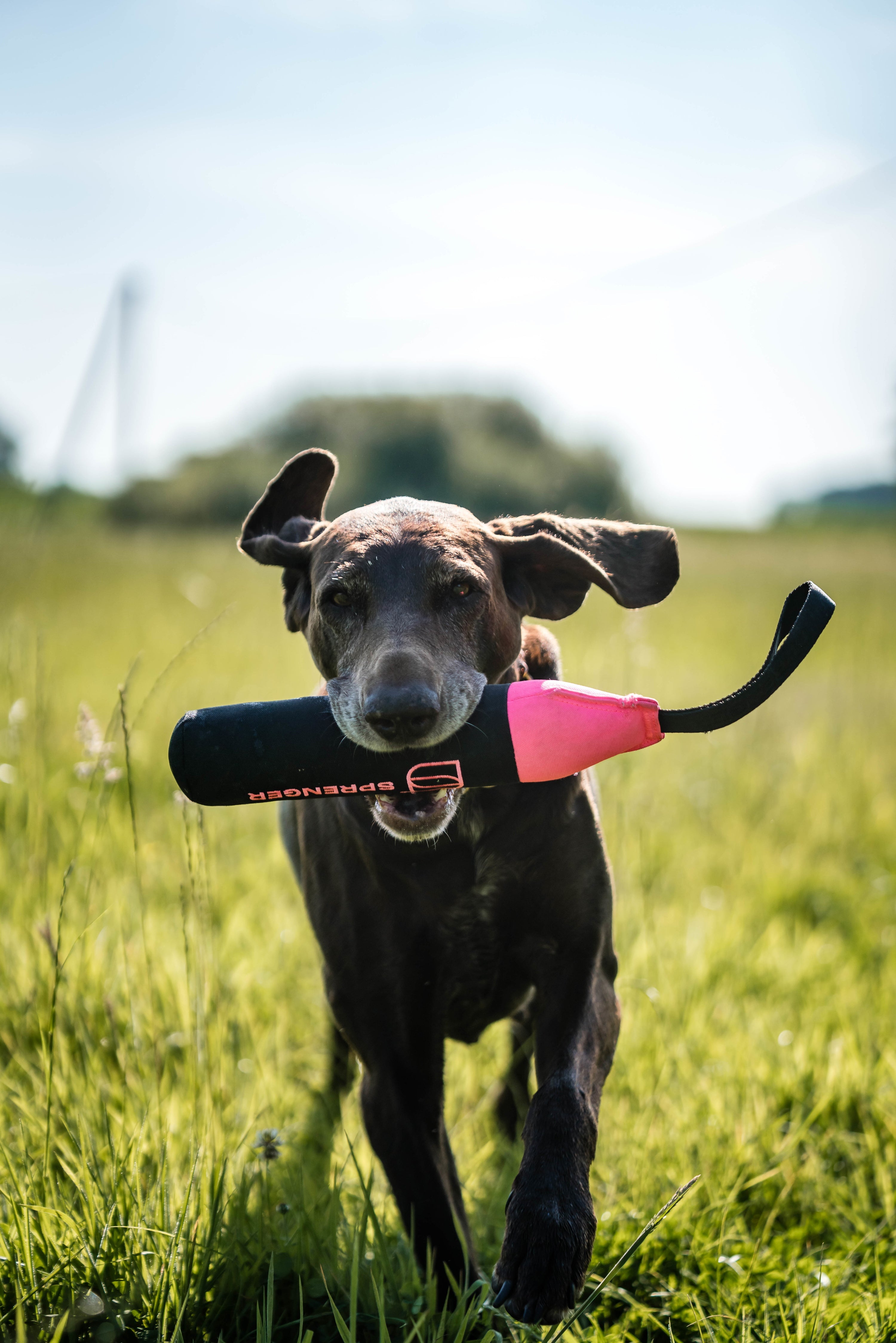
Dummy training is nowadays used by many dog owners as a dog sport and dog activity. In this blog post, we'll tell you everything you need to know about dog dummy training and how you can get starte...
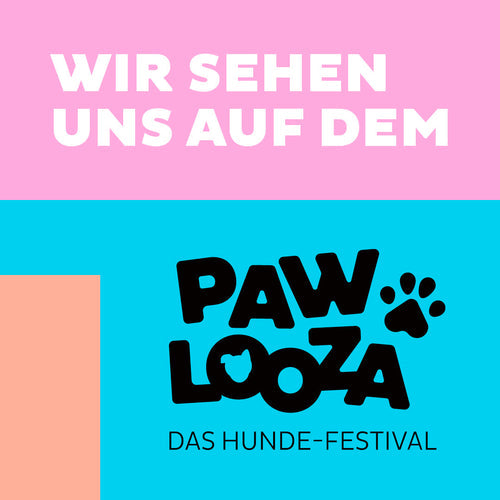
Das PAWLOOZA Hunde-Festival ist der perfekte Abschluss des Festivalsommers 2024! Was genau Dich erwartet und warum Du es auf keinen Fall verpassen solltest, verraten wir Dir hier!
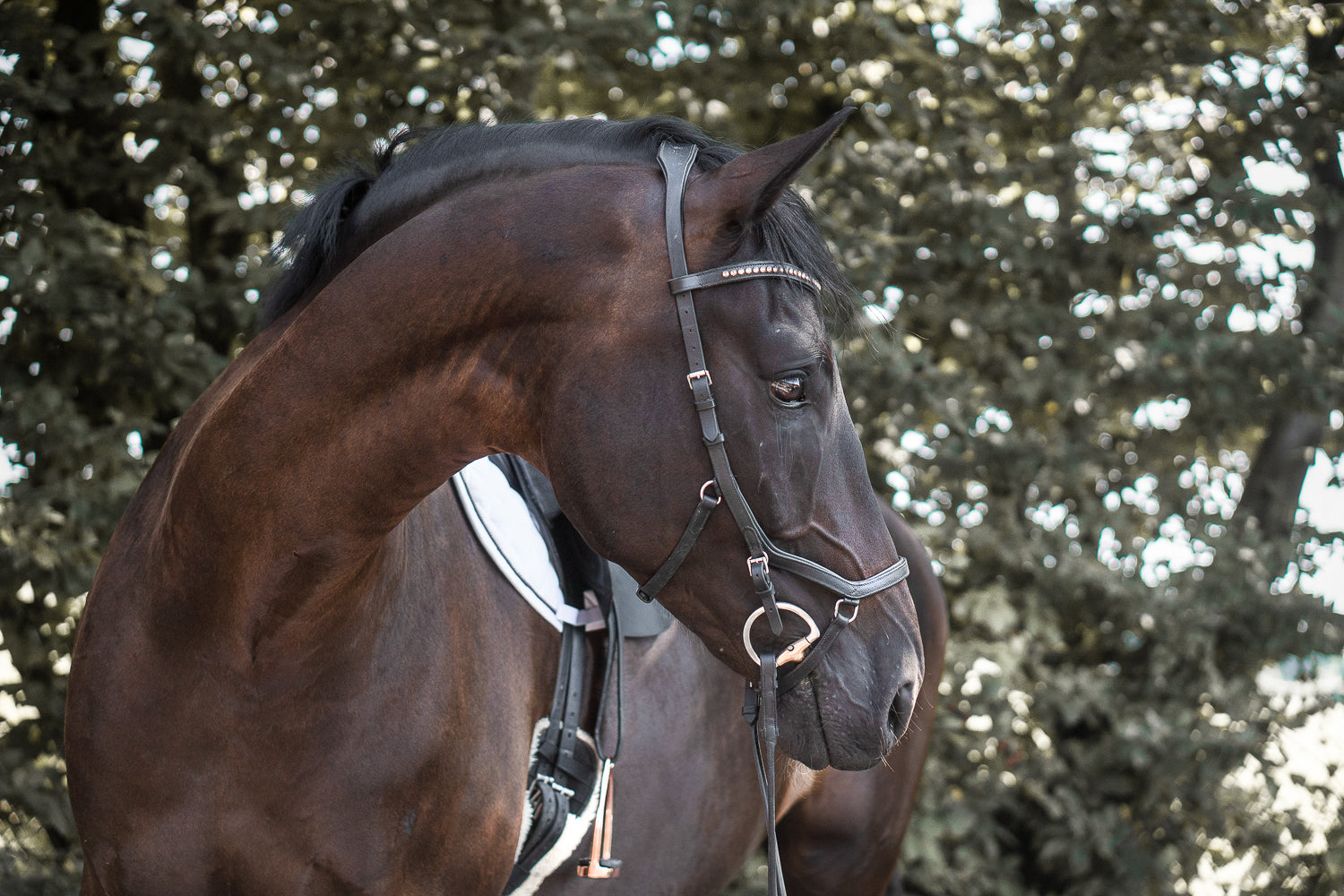
Which bit when horse leans on bit?
Your horse leans heavily on the bit and you are wondering whether this could be due to the bit? We look at possible causes and offer solutions.
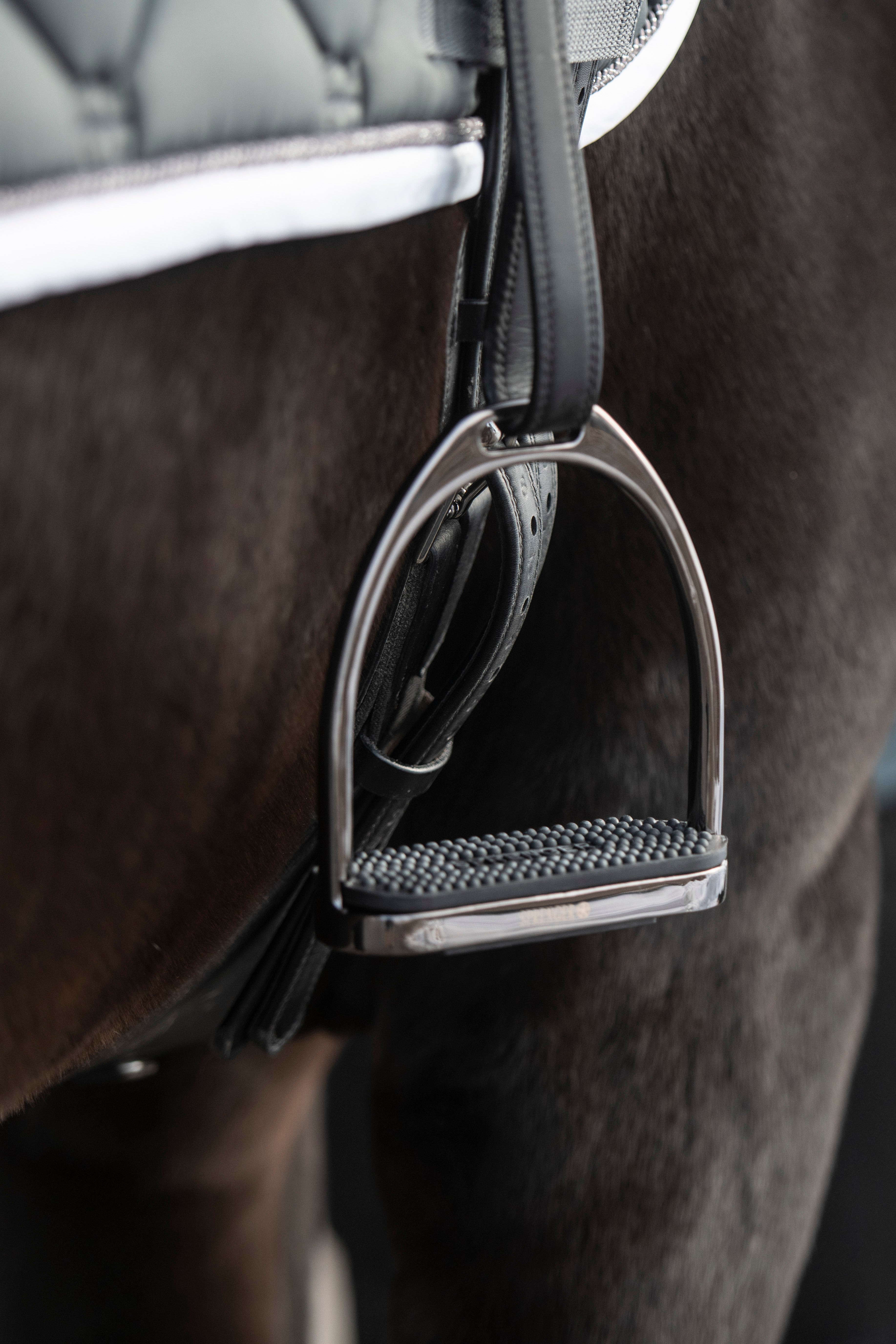
Discover the SPRENGER stirrups that offer safety, comfort and elegance for every rider! Our high-quality models are perfect for leisure and competition riders and guarantee durability. With SPRENGE...
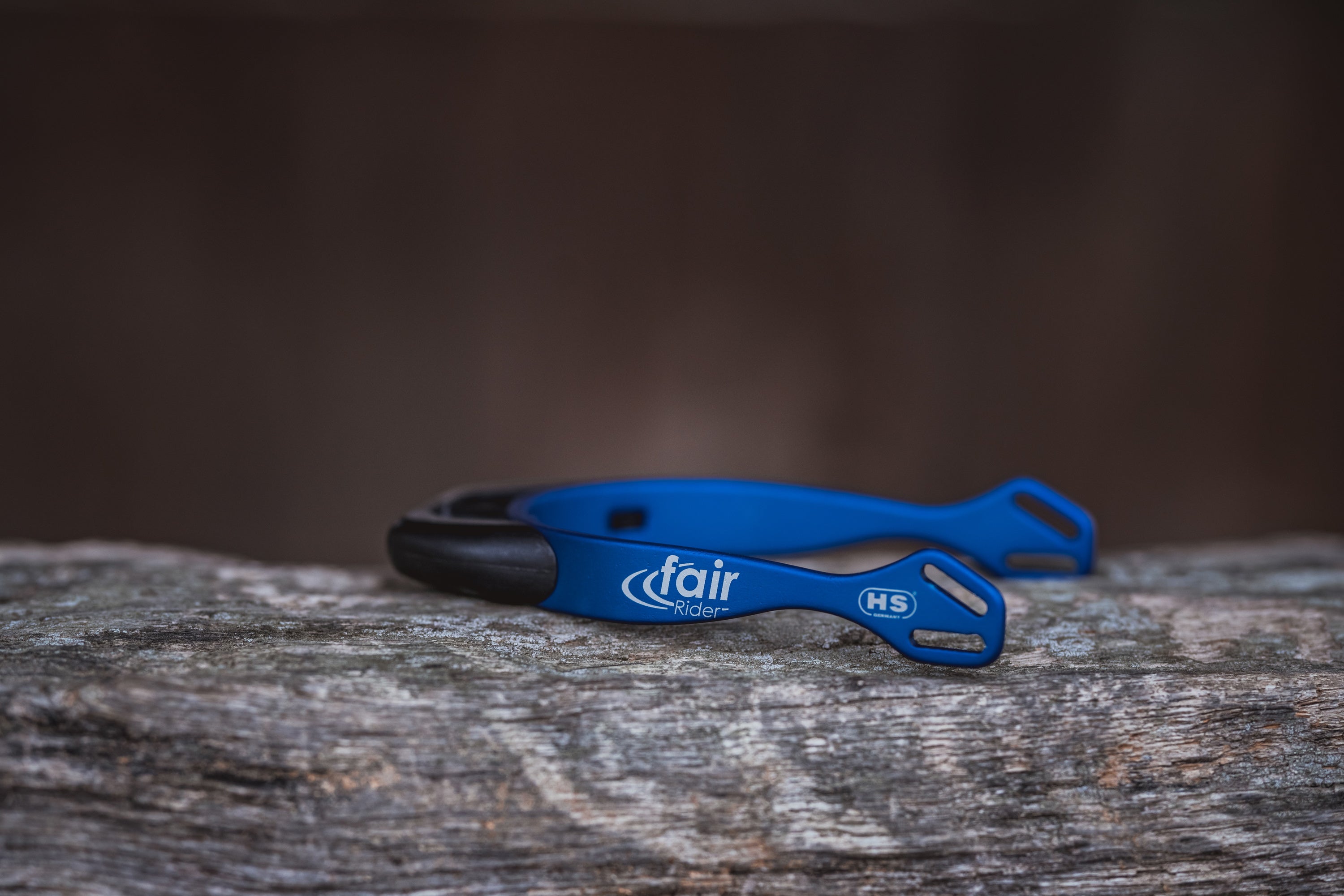
Do you already know our fair rider spurs? They are pioneers in horse-friendly riding and, with their wide impulse area, offer particularly gentle yet effective aids.
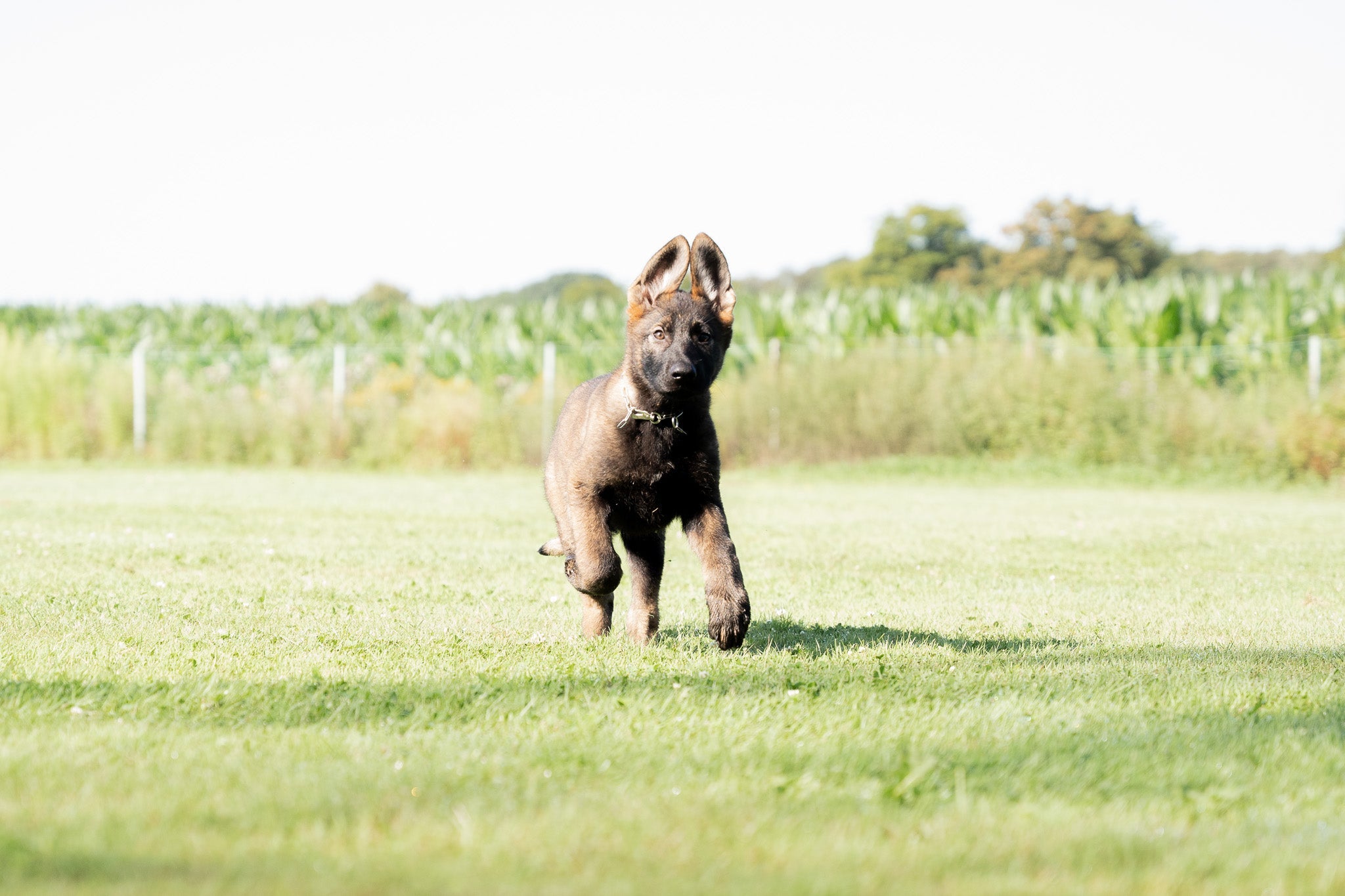
Puppy equipment: Gear, tips & formalities
When a new puppy moves in, an exciting time full of fun and doubt begins. We'll tell you everything you need to know!
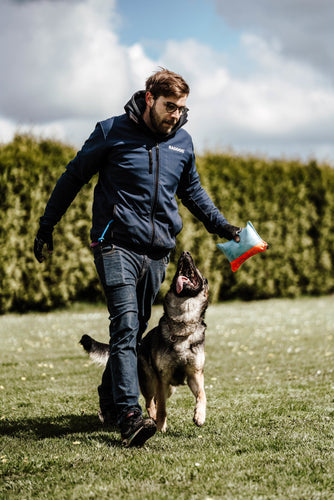
From agility and canicross to dog dancing - there is a suitable sport and the right equipment for every dog and dog owner. Find out what these are in working dog sports here!
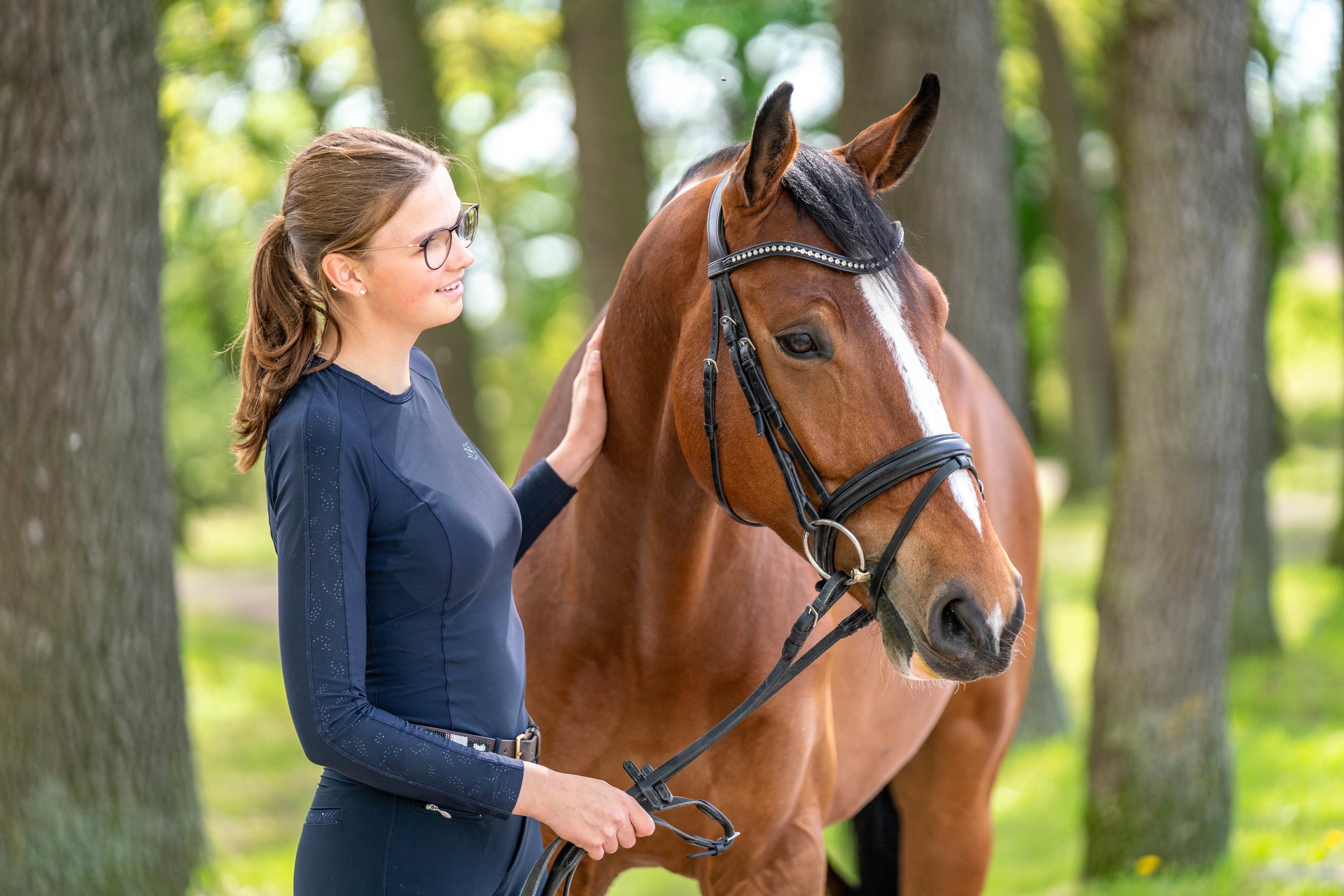
Bits are the most widely used means of communication with horses. In this article, you will find out what you need to consider when choosing the ideal bit for your horse. This is the only way to en...
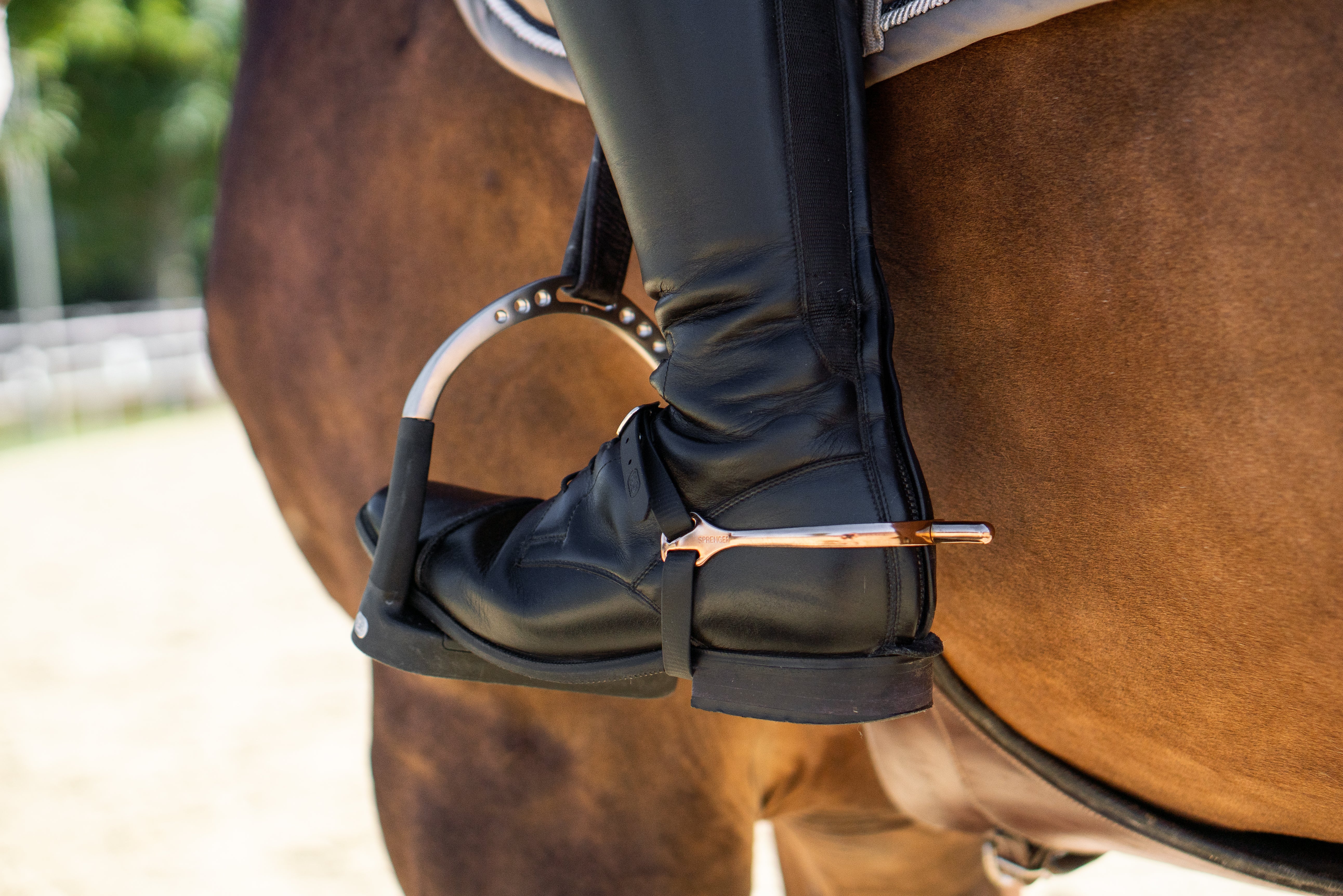
Spurs have to be earned. But what happens when you have reached that point? What do beginners need to bear in mind to prevent the horse from becoming blunt due to improper use of spurs? There are s...
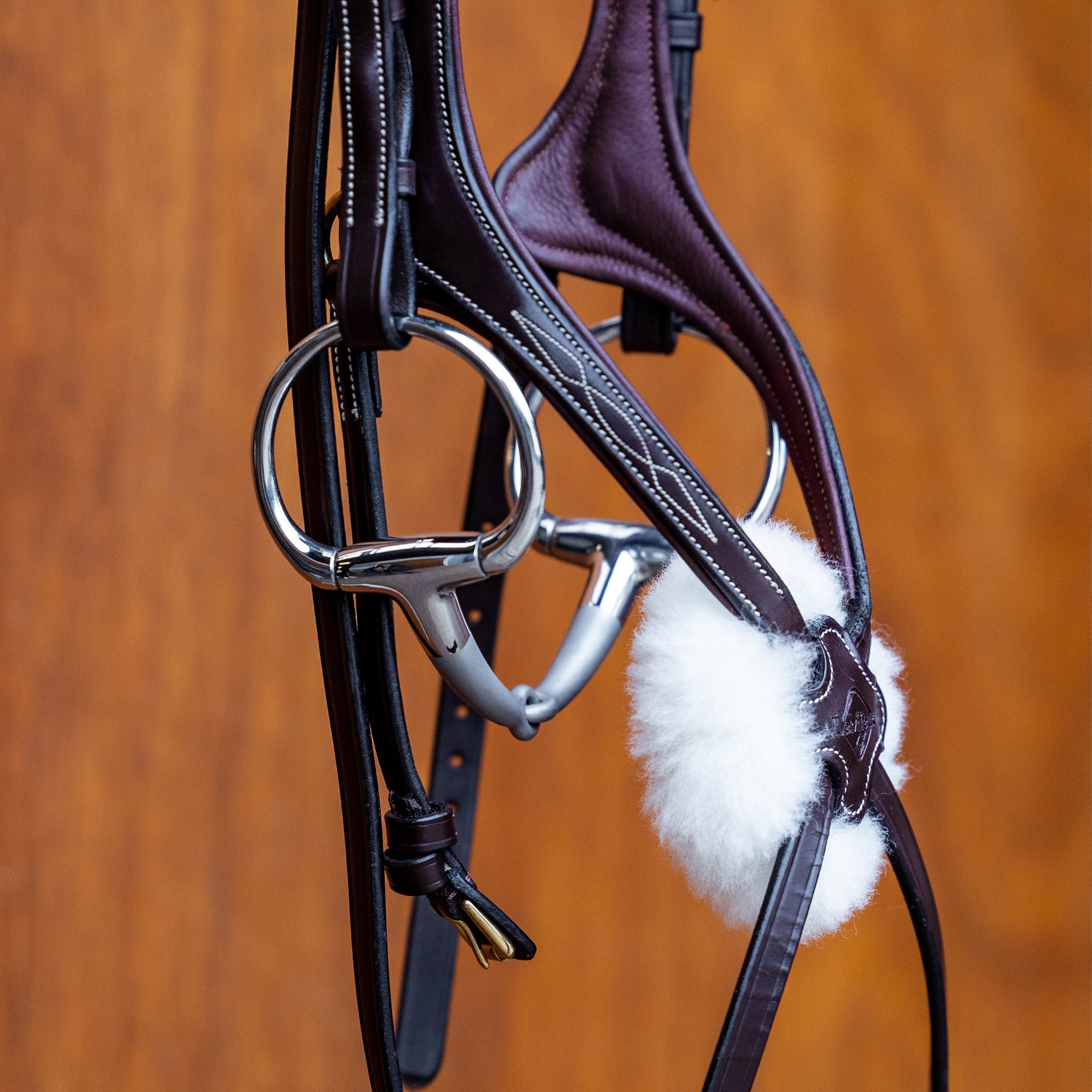
Eggbut & D-Ring Bits – The perfect framework for All Levels of Training
Eggbutt bits are an absolute all-rounder and can probably be found in every stable. Here you can find out which mouthpieces are available, the advantages of an eggbutt snaffle or D-ring bit and whi...
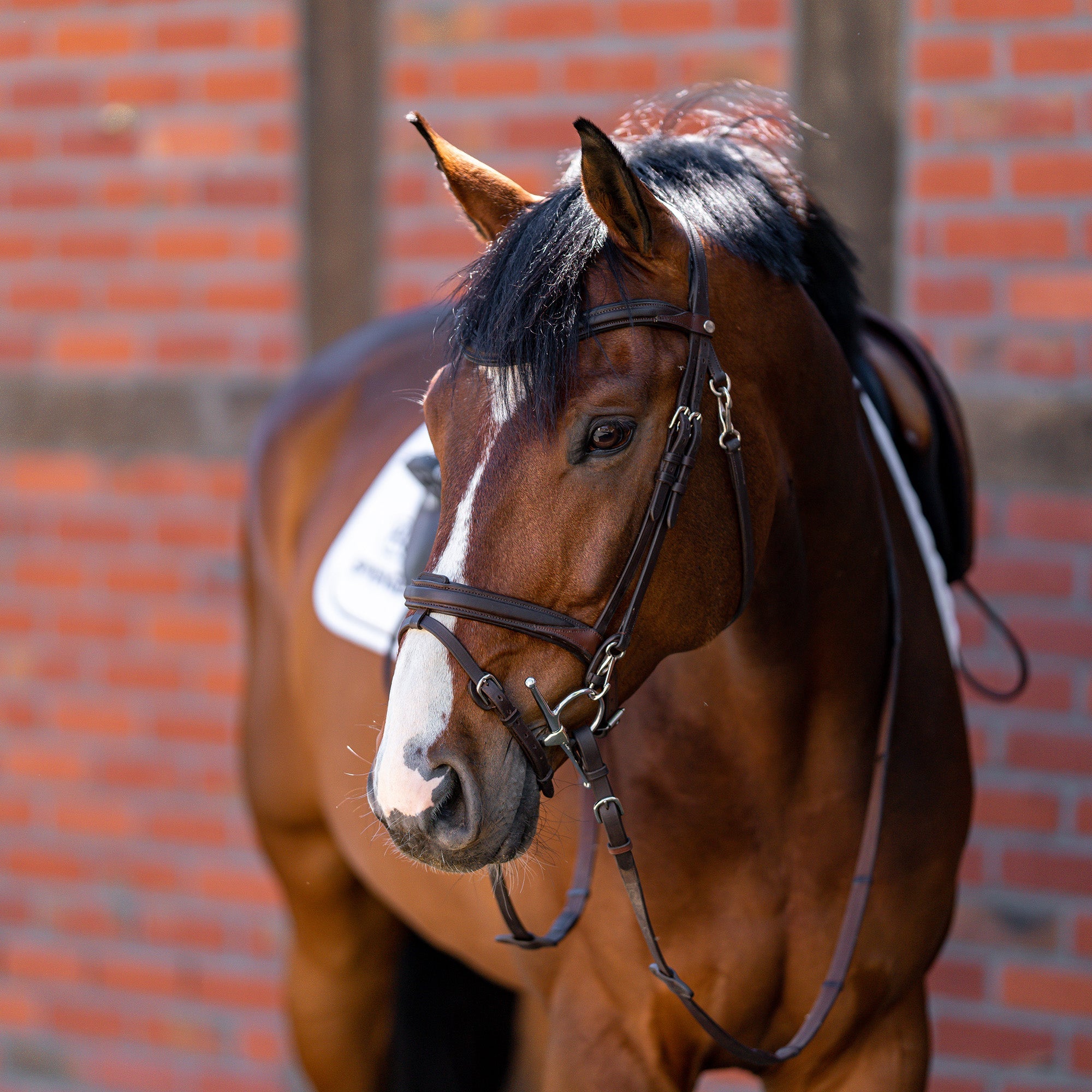
Why use a full cheek snaffle bit?
With its pronounced side pieces, the full cheek snaffle is even more restrictive than eggbut bits. Here you can find out which mouthpieces are available, what advantages a full cheek snaffle has an...
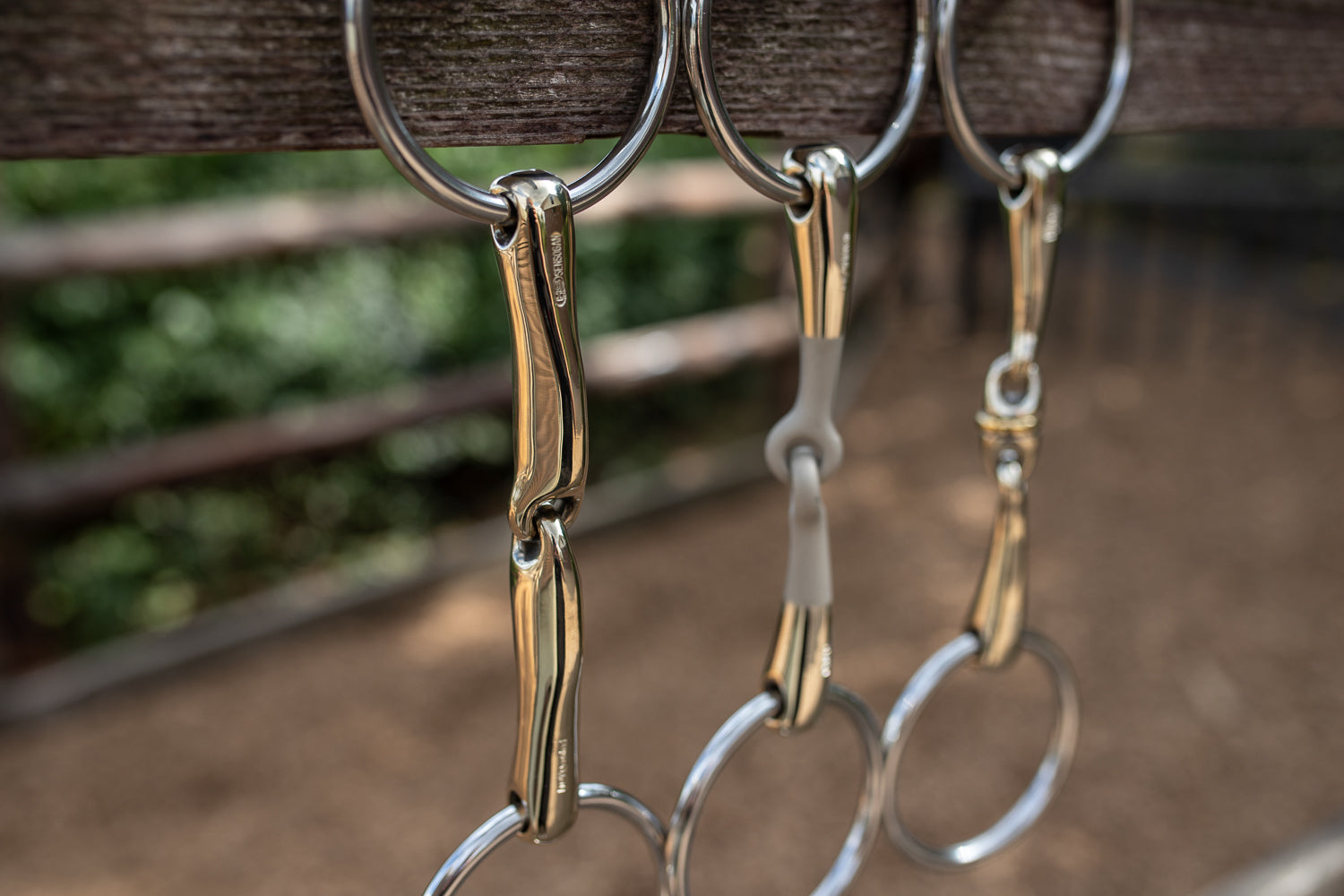
Wondering which bit is right for your horse? We can help you! With bit fittings, test centers and lots of videos and blog posts, we explain what you should look out for when choosing a bit.
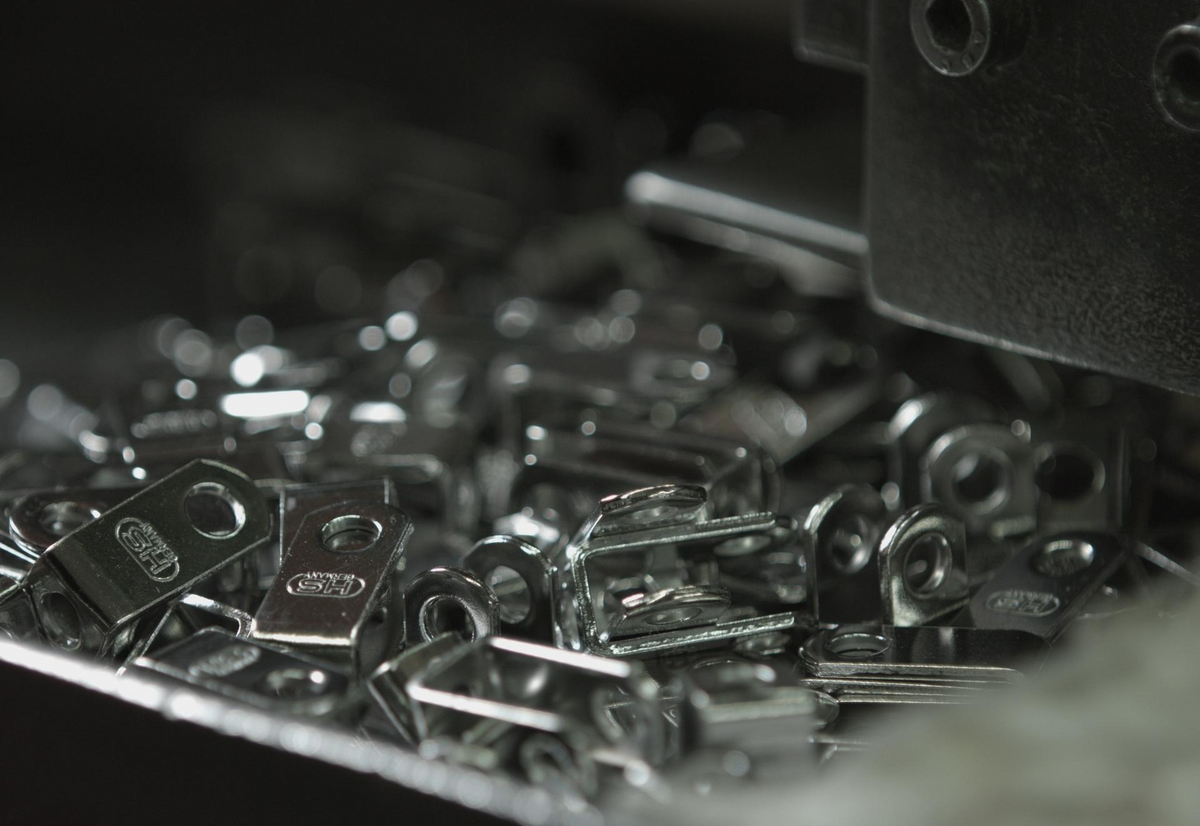
Individual solutions
For SPRENGER, the focus is on long-term partnerships with our customers. This enables us to respond individually to the requirements of our customers from various industries and to design optimally tailored solutions.